滚动轴承故障诊断的方法很多,除了前面介绍的对振动信号进行分析诊断外,以下再介绍几种其他监测诊断方法。 一、光纤维监测诊断法 精密轴承对轴的回转精度要求极高,如果回转运动误差过大系统就无法正常运转,即认为出现了故障,而此时振动信号并不一定很强。由于振动监测法是在轴承座、轴承盖或机器外壳表面拾取信号,这样故障诊断的灵敏度就受到了限制。最好的方法是直接监测回转轴心位置的变化,但这样做传感器安装难度很大,仪器也较复杂。 有一种替代的方法是监测轴承外圈上一点相对于轴承座的位移。即使是高精度轴承,在载荷作用下转动时,轴承外圈也会发生接近于简谐变化的弹性变形。对精度降低或有故障的轴承(如滚动体尺寸不均匀、滚道精度丧失、表面粗糙度增大等),外圈上的径向变形幅度将会进一步增大,如能测得外圈表面的变形,就能够对轴承状态加以判断。涡流传感器和光纤传感器都能够测量这种变形,但后者径向尺寸小很多,灵敏度较高。 1.光纤传感器的原理 光纤位移传感器的构造如图1所示,它由多根光导纤维组成,可分为发送光纤束和接收光纤束两种。两束光纤在横截面中的分布方式有多种,在图1(a)中为随机分布,图1(b)中为相间分布,图1(c)中则为圆环形分布。在这三种分布中,圆环形分布最常用,等间隔分布最灵敏,但制造最困难。 光纤位移传感器的安装方式如图2所示。

图1 光纤传感器的横截面形式 图2 光纤传器的安装方法
光纤传感器的基本原理如图3(a)所示。光线由发射光纤束射出,在端口有一发散角形成发送光锥。光线从轴承表面反射回来,再由接收光纤束接收。它所能接收到的光线被限制在一个锥面内,此锥面称为反射光锥。被接收的光线被光电元件转换为电压输出。间隙d改变时,发送光锥照射在轴承外圈表面上的面积随之改变,接收光纤束所接收到的光线强度也随之改变。光纤传感器输出电压一间隙特性曲线如图3 (b)所示。特性曲线开始有一段较陡的线性区(灵敏度较高),这是因为当间隙d从零开始增加时,发送光锥在轴承表面上照射面积迅速增大,接收光纤束所接收的光量不断增大,直到达到峰值。此后,若间隙进一步增大时,接收光纤束所接收的光量反而减少,它与间隙的平方成反比。在特性曲线的后段呈缓慢下降的趋势,灵敏度较低、线性差。

图3 光纤式位移传感器的原理及特性曲线 1—光送光纤束;2—接收光纤束;3—发送光维;4—反射光锥;5—轴承表面
采用光纤监测技术进行滚动轴承故障诊断具有以下优点。 (1)光纤位移传感器具有较高的灵敏度(可达50mV /μm),且外形细长,便于安装。 (2)可以减少或消除振动传递传递过程中噪声的侵入和信号的衰减影响,从而提高信噪比。 (3)可以直接反映滚动轴承的制造质量、工作表面磨损情况、载荷、润滑和间隙的情况,反映直观明确。 2.故障诊断指标 采用光纤监测技术进行滚动轴承故障诊断的指标主要包括有效值、峰值有效值比、轴承速率比等。 (1)有效值φx 轴承由于其制造缺陷,如表面粗糙度、波纹度和圆度误差等,会形成不规则的轮廓,运行时就会产生振动。这一振动由光纤传感器接收后,即可得图4所示的φx脉动波形。
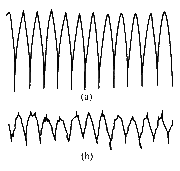
图4 均方根幅值的变化反映轴承制造质量的不同
图5 滚动轴承的BSR值
图4(a)为一个接近理想的高精度电动机轴承形成的波形,其套圈的弹性变形接近简谐波形,其波数等于通过测点的钢球数目;图4 (b)为精度级最低的轴承形成的复杂波形,这种轴承不但表面粗糙度大,几何形状误差大,而且钢球直径也有明显不同。由此可见,可用光纤传感器直接检测在用轴承的质量,这是一种简单而有效的测试方法。 (2)峰值有效值比XP/φx), 对于经过一段时间运行的滚动轴承,其工作表面会由于磨损而变得粗糙。虽然此时轴承表面粗糙状况也可以用上述有效值指标来表示,但是当轴承零件上有局部的剥落、凹坑一类缺陷时,有效值就无法反映出来。这时通过峰值有效值比则可以明显地反映出来。一般来说,当XP/φx>1.5时,就认为轴承零件上有局部缺陷产生。 (3)轴承速率比BSR 轴承速率比BSR定义为钢球通过频率与轴的回转频率之比,它取决于轴承的载荷和间隙的大小以及轴承的润滑状况,图5为BSR值与轴承载荷的关系。图中的阴影部分是轴承正常工作时的BSR值,当BSR值偏高时,则可能是载荷高、润滑不良或者轴承间隙过大;当BSR值偏低时,则可能是载荷不足、润滑过多(例如润滑脂加注过多)或者轴承间隙过小。由此可见,BSR值是反映轴承运行性能的直接指标。 由于载荷是由钢球与滚道传递的,当钢球通过滚道上的监测点时,滚道将以钢球的接触点为中心产生弹性变形区,这样,光纤传感器就可以直接测量这一变形,从而确定钢球的通过频率。而轴的回转频率则可以利用另外安装一套位传感器作为时标加以确定。
|