|
设
备
管
理
网
s
b
g
l
.
j
d
z
j
.
c
o
m
|
 |
汽轮机转子疲劳–蠕变损伤的非线性损伤力学分析 |
|
|
汽轮机转子疲劳–蠕变损伤的非线性损伤力学分析 |
|
作者:佚名 文章来源:不详 点击数: 更新时间:2008-9-26 19:54:30  |
|
摘 要:转子是汽轮机的核心部件,往往要在高温、复杂应力情况下工作,易产生裂纹萌生。除疲劳作用外,蠕变在转子的寿命损耗中也占有相当的比例。一般低周疲劳约占转子总寿命的80%,而蠕变则占转子总寿命的20%。事实上,对汽轮机转子而言,疲劳和蠕变往往是同时发生并存在着相互的作用。该文采用非线性损伤力学模型估算了国产600MW汽轮机高压转子在实际启停功况下的疲劳-蠕变寿命,考虑了疲劳与蠕变的耦合作用以及多轴应力的影响,并与当前汽轮机疲劳-蠕变寿命估算普遍采用的线性累积损伤理论进行了对比。结果表明:非线性连续损伤力学模型正确地反映了疲劳-蠕变交互作用以及损伤演化的非线性机制,其分析结果比现行理论方法更为准确、可靠。 关键词:疲劳-蠕变;损伤;汽轮机转子;损伤力学
1 引言 现代电力工业的发展要求汽轮机各部件要承受更高的温度和更大的工作载荷。因此,汽轮机高温材料的蠕变以及疲劳-蠕变耦合损伤行为和破坏机制受到高度重视。而目前蠕变-疲劳耦合寿命的分析方法主要有两种:只计算疲劳所消耗的寿命,大致认为疲劳损伤占总寿命的80%,蠕变损伤约占总寿命的20%。由于这种方法缺乏有力的理论支持,所以,目前甚至在汽轮机工程界内对该法也有异议。第二种方法将疲劳和蠕变的作用在时间上看作是连续的,即在启动和停机过程中只考虑低周疲劳损伤,而在运行的过程中只考虑蠕变损伤。这种方法虽然比第一种方法精确,但由于疲劳和蠕变损伤是各自单独计算的,并将其简单的线性叠加。因此,该方法并没有反映出蠕变-疲劳的非线性交互作用对损伤演化的影响。 近二十多年发展起来的损伤力学,最初是由预计高温蠕变、构件的寿命而发端的。它提出了连续度的概念,把损伤纳入热力学框架,采用宏观唯象方法考察微观缺陷对材料的机械性能、结构应力分布的影响以及缺陷的演化规律,这一学科的出现,为损伤的定量描述提供了理论基础,并有着广泛的应用前景[1-2]。 汽轮机转子要在高温、高转速下工作,易产生疲劳和蠕变损伤。本文将对当前蠕变、疲劳-蠕变损伤分析理论和连续损伤力学方法进行对比分析。利用600MW汽轮机转子在典型启停工况下应力场的瞬态热弹塑性分析结果,采用连续损伤力学模型分析汽轮机高压转子的蠕变、疲劳–蠕变损伤,并同现行的损伤理论所得结果进行比较,以得出有益的结论。 2 理论模型 2.1 线性累积损伤理论 目前在汽轮机行业这一工程领域中处理疲劳-蠕变耦合寿命的方法主要是线性累积方法: 在时间上将疲劳、蠕变作用看作是连续的,即在启动过程中只考虑低周疲劳损伤的积累,而在运行的过程中只考虑蠕变损伤的积累。二者的耦合采用Miner定律,可表示为
 式中 ti为定应力和温度下的工作时间;tci为同样条件下的蠕变寿命;ni为定周变应力下的循环次数;Nfi为同样条件下的低周疲劳寿命。 该方法认为耦合情况下寿命仍以线性的方式消耗,而真实情况下损伤是按非线性的方式累积的。 蠕变寿命tc可由下式获得
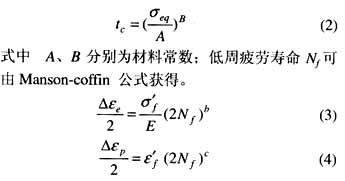 线性累积损伤定律是建立在以下假设基础之上的:① 载荷必需是对称循环;② 对于每一应力水平,不论在寿命的前期或后期,每次的蠕变损伤应该是相同的;③ 无论是由高到低或由低到高,加载顺序的变化不应该影响寿命。 2.2 损伤力学理论 根据卡钱诺夫-拉博诺夫的经典损伤理论,对于一根受单轴拉伸的试样,可以构思成三种状态,既初始无损状态、损伤状态和虚构无损状态。损伤变量D(0≤D≤1)表征着微裂纹和微空隙导致材料损伤过程中有效承载面积减小的程度,即由于分布的微裂纹和微空隙的形成与扩展,试件的横截面积A减小到有效承载面积A*。由此损伤变量D和A*的关系为
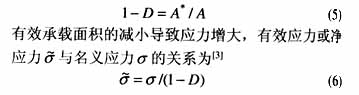 可以认为:材料的损伤是由材料内部的微裂纹和微空隙导致有效承载面积减小、材料的承载能力降低,从而使材料的力学性能劣化[3-4]。 令Df表示疲劳损伤,Dc表示蠕变损伤,则两种损伤的增量表达式可以写成[3]
 材料中不同的缺陷不能直接相加,但是根据式(5)、(6)损伤力学有效应力的定义,分别由疲劳和蠕变所造成的结构实际承载截面积的减少量则可以相加[4],因此可假设
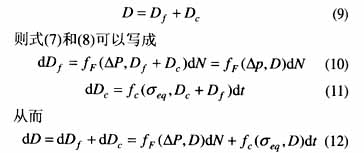 式中fF和fc两函数都是非线性的,而且由于两个函数中都含有损伤变量D,因而式(12)表明了疲劳-蠕变损伤的非线性本质。 fF和fc两函数中,包括一系列材料常数。作为简化计算,分别从纯疲劳和纯蠕变两组试验中确定这些常数并将它们用于疲劳-蠕变交互作用下的损伤增量表达式。其中蠕变损伤的增量表达式采用Lemaitre模型[4]
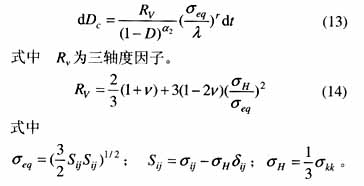 在单轴载荷情况下RV=1。低周疲劳损伤的增量形式则由下式给出[4]
 可以看出:以上的损伤力学模型所描述的损伤累积是非线性的,考虑了多轴复杂应力的影响,而且疲劳与蠕变的非线性交互作用也被考虑了进去。 3 600MW汽轮机转子温度场和应力场分析 600MW汽轮机高压转子的调节级和前汽封以及第一、二压力级、中心孔等区段在机组启、停机和变负荷的过程中往往产生较大的温度梯度,由此会产生较大的交变热应力,因此,该区域的寿命决定着整个汽轮机的使用寿命。本文采用ADINA大型通用有限元程序,根据机组实际运行的冷态启动和滑参数停机曲线,对机组危险区域进行了瞬态温度场及热弹塑性分析。分析采用8节点轴对称单元,局部采用了过渡单元,其有限元网格见图1。启停机曲线如图2所示[5 ]。
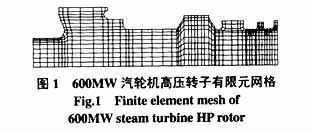
计算过程中,所有的物性参数都被视为时间和温度的函数,其由表1给出,换热系数采用西屋公司的换热系数[6]。由于采用简单拉伸的σ-ε关系进行应力、应变分析,对于循环软化材料,往往会低估其实际的低周疲劳损伤。因此,该分析采用600MW汽轮机转子材料30Cr1Mo1V稳定循环下的σ-ε曲线进行瞬态热弹塑性应力、应变分析,曲线如图3所示。分析过程中考虑了转子和叶片的离心力作用,并将其作为转速的函数。分析结果表明:部分区域进入了塑性,其累积有效塑性应变和三轴度因子值见表2。
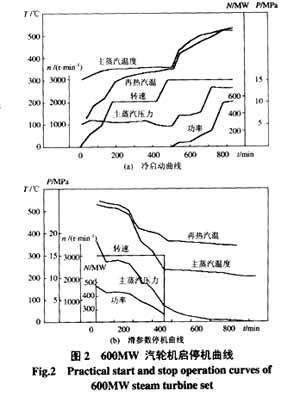
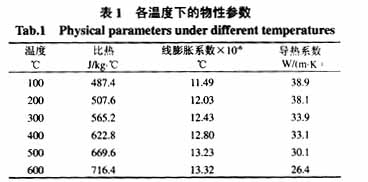
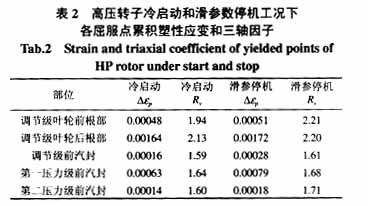
当汽轮机的载荷达到额定值时,蒸汽温度也几乎达到最高值,此时高温蠕变往往产生作用。因此,机组的蠕变损伤,也往往在机组稳定运行时产生。转子在达到额定载荷时的温度场和应力场分别由图4,图5给出。其中,应力集中处的温度和等效应力由表3给出。
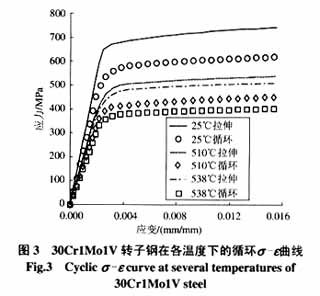
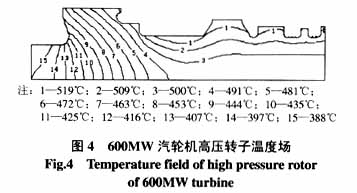
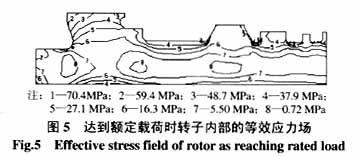
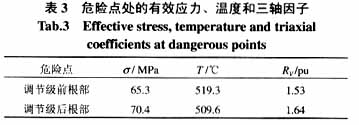
4 损伤分析和模型比较 30Cr1Mo1V转子钢在525℃下的线性累积理论的蠕变寿命预测式可由文献[8]的30Cr1Mo1V高温蠕变试验获得
 根据第二节的损伤力学理论和文献[8]中的试验结果,可得到30Cr1Mo1V 转子钢在525℃下的多轴连续损伤力学模型
 单轴情况下,RV=1。分别将该模型同试验结果和线性累积损伤理论结果进行比较,如图6所示,可以看出,单轴下的蠕变损伤模型与试验结果温和较好,而线性累积损伤理论则与试验结果偏差较大。从试验结果可以看出,蠕变损伤的演化是一个非线性的过程,而线性累积损伤理论则高估了转子的损伤。
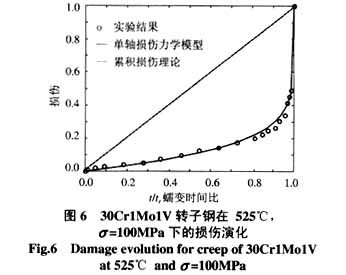
由30Cr1Mo1V转子钢的在510℃下的低周疲劳试验结果[7],可分别得到传统的Manson-coffin公式和多轴的损伤力学模型
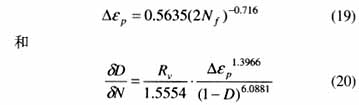 分别应用线性累积理论的寿命预测式(17)和损伤力学模型式(18),预测600MW汽轮机高压转子在稳定运行时的蠕变寿命,其结果见表4。可以看出传统的蠕变寿命预测结果与单轴连续损伤模型比较一致,而与多轴蠕变连续损伤模型的结果则相差较大。这反映出了当前的线性累积理论不能有效处理多轴复杂载荷的缺点。可以看出,三轴度因子对损伤和寿命的预测结果影响较大,它放映了多轴复杂应力对损伤的影响,图7 给出了对应于图5中应力场的转子三轴度因子的分布。 图8进一步给出了单轴和多轴连续损伤模型对蠕变损伤的分析结果,不难看出:多轴复杂应力大大加速了损伤的演化和发展,在蠕变损伤分析中是不可忽视的因素。在低周疲劳损伤分析过程中,可以得到类似的结论,具体分析过程由文献[10-11]给出。
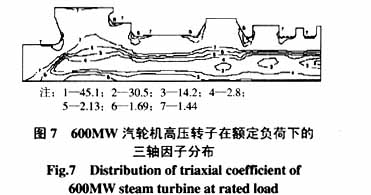
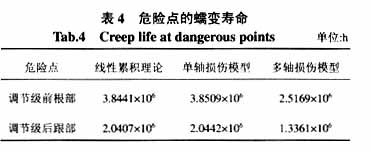
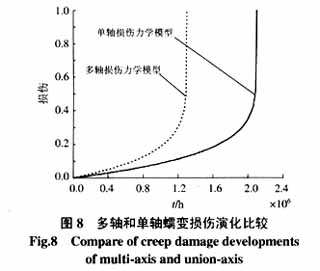
将式(18) 和式(20)合并,可以得到蠕变–疲劳耦合作用下的多轴损伤力学模型
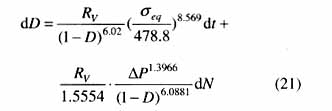 汽轮机的设计寿命一般为30年,按前面的启停机曲线平均1年启停3次,每次启停过程中,稳定运行时间为100h左右。表5给出了分别采用线性累积损伤理论和多轴损伤力学模型计算出的汽轮机高压转子在30年中的疲劳和蠕变的总损伤。
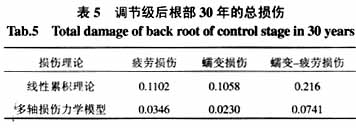 从表5中可以看出,采用损伤力学模型得到的蠕变–疲劳损伤并不象累积损伤理论那样等于疲劳损伤与蠕变损伤简单相加之和。而是明显要大于二者之和,这表明:蠕变与疲劳的交互作用加速了损伤的演化和发展,这与以往试验所得结论相符,而损伤力学模型很好的描述了这一耦合机制。 理论上,累积损伤理论认为当损伤值为1时,构件发生破坏,即Dc=1。而从图8中的多轴应力下的损伤演变规律不难看出,当损伤值达到0.24时,调节级叶轮后根部的寿命实际已消耗殆尽,此时Dc=0.24。因此,虽然采用多轴连续损伤模型计算得到的调节级叶轮后根部的蠕变–疲劳总损伤值为7.41%,但实际上此时已消耗了总寿命的30.88%;而采用累积损伤理论得到的寿命损耗为21.60%。可以看出,多轴连续损伤模型的结果比累积损伤理论的结果更为合理一些。 以上分析表明:损伤力学模型不仅可以考虑多轴复杂应力对损伤的影响,而且可以考虑蠕变与疲劳的非线性耦合作用,并正确地描述了损伤的非线性演化累积过程,其分析结果更接近实际。 5 结论 (1)由于累积损伤理论是基于单轴假定之下的,没有考虑多轴应力的影响,在进行蠕变寿命预测时,高估了转子寿命。 (2)非线性连续损伤模型,更准确地反映了转子材料蠕变的非线性损伤累积发展过程;而线性累积理论则高估了转子的蠕变损伤。 (3)多轴复杂应力大大缩短了转子材料的蠕变寿命,加速了损伤的累积过程。因此,在蠕变损伤分析中,必须考虑多轴应力的影响。 (4)从损伤的分析中可以看出,疲劳-蠕变的交互作用加速了汽轮机转子损伤的演化和发展,非线性连续损伤力学模型,很好地弥补了当前疲劳-蠕变损伤分析理论存在的缺点和不足,正确地反映了疲劳-蠕变交互作用以及损伤演化累积的非线性机制,并考虑了多种因素对损伤的影响。其分析结果比现行理论方法更为准确、可靠。
参考文献 [1] Sedmak A,Sedmak S.Critical crack assessment procedure for high pressure steam turbine rotors[J].Fati[1] [2] 下一页
|
|
文章录入:admin 责任编辑:admin |
|
|
上一篇文章: 汽轮发电机组停机方式、注意事项
下一篇文章: 汽轮机隔板裂纹的分析及焊修复 |
|
|
【字体:小 大】【发表评论】【加入收藏】【告诉好友】【打印此文】【关闭窗口】 |
|
网友评论:(只显示最新10条。评论内容只代表网友观点,与本站立场无关!) |
|
|
|
|