摘要:通过监测往复压缩机组相对于曲轴转角的压力、振动、超声波信号,将气阀开启与关闭、汽缸压缩与膨胀等和监测信号对应起来,更加有效地分析和判断事件具体性质,掌握机组运行状况,合理调整参数,及时发现故障隐患,达到改善机组工况、减少运行故障、提高综合经济效益的目的。
关键词:压缩机;监测诊断;实践
中图分类号:TH45 文献标识码:B
DPC800型机组是低速重载整体式往复压缩机组,主机为两级三缸双作用压缩机,动力部分是以天然气为燃料的发动机。目前累计运行时间均在10万h以上,达到设备效用年限,处于事故高发期,运行效率偏低。我公司从2004年开始,利用性能分析方法对其进行监测诊断,取得了明显成效,已成为压缩机日常管理的重要技术手段。
一、监测与诊断技术原理
通过监测相对于曲轴转角的压力、振动、超声波信号,将气阀开启与关闭、汽缸压缩与膨胀和监测信号对应起来,综合分析和判断事件具体性质,得到有价值的信息。
监测发动机缸内压力相对于曲轴转角的变化关系,得到一组反映燃烧释放热能转变为机械能完善程度的性能参数,如平均有效压力Pe、指示功率Pi等。分析发动机缸内的压力曲线和性能数据,能够判断各缸不平衡、死缸、爆燃、软点火、早燃等性能状况;同时结合各缸相位振动、超声波曲线,还能判断进排气阀、燃气门、缸套、活塞环、轴瓦等故障,详见表1。
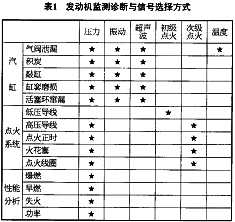
通过压缩机汽缸压力一容积曲线(pV曲线),可以计算出汽缸功率、容积效率、进排气阀的功率损失以及排气量、活塞杆负载荷、反向角等性能参数。分析PV曲线、Logp-LogV的n值、流量平衡和超声波信号,判断进排气阀是否漏气、活塞环是否窜漏;通过分析气阀相位振动、超声波曲线和温度,分析气阀开启关闭状态,判断气阀颤振、弹簧折断、阀片断裂等故障;通过分析汽缸和十字头的振动信号,判断缸套擦伤、活塞环断裂、十字头损伤、间隙过大和机械松动等故障。
二、监测与诊断技术应用
依据上述原理,在DPC800型机组上做了两项有效工作,一是利用监测信息对机组进行性能分析,以确定设备运行状况,为合理调节参数提供科学依据;二是对监测发现的异常信息进行故障诊断分析。
1.性能分析
(1)发动机性能分析。通过对发动机性能状况的监测分析,判断其工作是否正常,分析查找影响性能的原因,采取有效措施加以排除,提高和改善发动机性能。受点火提前角、空燃比、缸温、进气温度、转速、负荷等诸多因素影响,经常会出现汽缸工作不平衡、振动超常、噪声大、发动机性能下降的现象。
从某发动机燃烧测试报告知,各缸平均峰值点火压力PFPs、与发动机平均峰值点火压力PFP偏差达到16%(正常情况应在10%以下),转速波动达到6%,说明各缸工作不平衡。4#缸峰值点火压力循环变动偏差较大,平均为0.53MPa。由于点火正时不稳定,各循环之间及同一循环中各缸混合气时空分布不均匀,各燃烧室内气流运动变化,每循环实际进入燃烧室内燃料组分差异的影响,汽缸各燃烧循环之间在压力值与相位、燃烧起始点与燃烧持续期以及图形大小与形状都存在差别,差别越小,汽缸工作就越平稳。4#缸变动超出正常范围,且在负荷只有84%的情况下,排气温度却比满负荷高出30°多,燃烧起始角和峰值点火压力角都比较靠前,这说明可能存在死缸和爆燃倾向。
图1的压力曲线反映发动机点火提前大约5°~6°。数据统计显示,在所采集的40个循环周期中,1#缸各循环点火燃烧正常,2#、3#、4#缸有近1/4的死缸和爆燃,受其影响发动机工作不平稳,转速波动较大,排气温度偏高,并伴随严重的敲缸,无法正常加载,造成频繁停机。一可能的原因包括燃气组分变化、空燃比不合适、点火不正常、负荷过重、进气温度过高或冷却不够。

据此,首先重新标定调整发动机点火正时,更换磁电机、高压导线、点火线圈及磁电机至接线盒间接触不良的电缆线,保证正确点火;维修或更换机组损坏的注气阀,重新调整燃气注入量,吹扫更换空气滤芯,确保进入各缸的燃气和空气连续、均匀、平稳;定期对燃气分离缓冲罐排液,确保燃气组分稳定;冲洗空冷器的管束翅片,清除积垢和尘土,检查和调整空冷器风扇皮带,确保换热效果。
通过采取以上措施,机组爆燃敲缸次数明显减少,带载能力增强,各项参数基本恢复正常。四个缸做功基本平衡,各缸平均峰值点火压力PFPs与发动机平均峰值点火压力PFP偏差下降到6%,转速波动下降到2%;各缸平均峰值点火压力循环变动偏差降为0.197MPa,降幅达84%。燃烧起始点、平均峰值点火压力角、排气温度均在正常范围之内,在相同条件下发动机功率提高了10.9%。
(2)压缩机性能分析。据统计,压缩机60%以上故障发生在气阀,25%重大事故是由活塞杆断裂造成,能够及时发现此类故障对于压缩机的安全运行十一分重要。
通过测试汽缸压力,利用性能分析方法能实时快速计算出压缩机实际排气量、消耗功率、活塞杆负荷、流量平衡等性能参数,准确掌握压缩机工作状况。根据实际操作条件调整压缩机负荷,更换或维修失效部件,可提高压缩机运行效率和可靠性,延长维护保养周期,减少材料消耗,降低运行费用。
正常情况下汽缸的吸入体积流量与排出流量大致平衡,应在0.95~1.05间。某压缩机3#缸曲轴端流址平均为1.148,即通过吸气阀进入气缸的气体大于排气阀排出的气体,在Logp-LogV曲线(图2)上n值大干1.05,表明吸气阀泄漏。从图3的pT曲线和曲轴端3CS1和3CS2两个吸气阀超声波信号也能得到印证。3CS1吸气阀在汽缸排气过程中有较强烈的振动信号,这是因为排气过程中在强大压差作用下气体通过吸气阀泄漏所致。
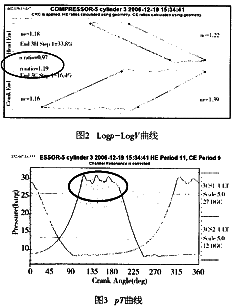
2.故障诊断
(1)活塞环断裂。图4、图5、图6分别是发动机动力缸超声波曲线、低频及高频振动曲线。超声波曲线中,3#缸在排气口开启和关闭时其振动信号幅值明显小于1#、2#缸。正常情况下排气口打开瞬间,缸内高压气体在汽缸与排气道压差作用下会产生气流激振,排气口随活塞运动逐渐增大,压差逐渐减小,激振信号减弱,关闭时也会因流道变小产生同样的效果。如果活塞环断裂或磨损过大导致汽缸泄漏,内外压差减小,排气时激振幅值会大大减弱,并持续较长时间。从图5可以看出3#缸图形基带较宽,幅值较大,可能是活塞环断口有毛刺或缸套存在划痕使活塞在汽缸内运动摩擦增大。图6显示排气过程中振动幅值比其他缸大,活塞环断裂或接触面的毛刺将加剧振动。通过综合分析,初步认为是活塞环断裂或缸套磨损。停机检修时,发现有两道活塞环断裂,更换活塞后测试信号恢复正常。

(2)连杆瓦失效。图7是压缩机气缸十字头VT1振动曲线,可看出十字头振动曲线在活塞力换向时出现了异常信号。对于往复双作用汽缸,活塞往复运动一次,活塞杆反向受力两次。

正常情况下润滑良好的摩擦副运动时会产生高频宽带噪声,基带较窄。润滑不好致使摩擦加剧,振动幅值会变大,基带变宽。轴瓦配合间隙变大时会出现松旷,活塞力反向时产生幅值较大的冲击信号,结合运行情况分析认为,可能是连杆大小头轴瓦或十字头间隙不合适,也可能是十字头、活塞杆等连接部位松动。为了确保机组安全运行,进行了停机检查,发现连杆瓦巴氏合金涂层全部脱落,瓦背在受力部位有细小横向裂纹和轻微的局部拉伤。更换损坏的连杆瓦后数据恢复正常。
三、应用效果分析
对压缩机进行监测诊断以来,取得了非常明显的效果,已成为该型机组日常管理必不可少的重要技术手段。
1.改善了运行工况。通过对压缩机组的监测分析,实时掌握机组性能状况,及时调整工艺参数,减少不必要的功率损耗,使机组平均效率保持在90%以上。
2.消除了故障隐患。大大降低了机组故障停机率,由2004年的1.01%下降到2006年的0.29%。
3.创造了良好效益。机组运行效率和可靠性提高,维护保养周期延长,作业次数减少,降低了材料消耗和人工费用。
参考文献:
[1]Dnalco Corp of America.RT9240往复压缩机分析系统用户手册[K].
[2](美)Paul C.lon. Compressor Handbook[K].
[3]盛兆顺,尹琦岭.设备状态监测与故障诊断技术及应用[M].化学工业出版杜.
[4]郁永章.容积式压缩机[M].机械工业出版社.
[5]刘永长.内燃机原理[M].华中科技大学出版社.
|