一.TPM的发展趋势 所谓的TPM,是由「全员参与PM」Total Productive Maintenance这几个英文字的字首“T”、“P”、“M”的简称。也称全面生产保养,中文名词因翻译问题各企业有所不同。自从TPM开发以来至今已有25年的历史。TPM是在1971年由日本电装(株)开始实施,且成果丰硕并进而得到「PM优秀事业场奖」,这也是日本TPM的起源。 1.TPM的发展历史 在1950年之前,设备处于事后保养时代,设备保养有如灭火队一样,保养人员随时待命出发。 1> 第一代的TPM 在1951年,日本导入预防保养(PM)后,设备管理便脱离事后保养(BM)的时代。而预防保养也可以说是设备的预防医学,利用预防保养可使设备的故障(疾病),防患于未然,并藉此来延长设备的使用寿命。对于设备的全体寿命而言,进行保养预防(MP:自新设备计量、设计开始、即将免保养的设计考虑进去)→预防保养(PM:设备健康管理)→改良保养(CM:将设备加以改良或更容易保养,是比设备健康管理更进一步的设备体质改善),总称提升设备的生产活动为生产保养(简称PM)。此后20年间,设备管理导入了改良保养(CM)与保养预防(MP)的观念,发展成生产保养。在此过程中,「我是制造者,你是保养者」的设备保养分业体制,透过对作业人员的设备保养教育,发展出以作业人员为主的自主保养。 在设备自动化的演进中,第一代TPM的特色,即是自主保养,换言之,就是以自主保养为开端,因此使得故障大幅降低、设备效率快速提高,TPM时代,将作业员的自主保养(自己的设备自己保养的观念及作法),利用重覆小集团的观念及作法全面展开是其特色,重覆小集团对组织规模较大的企业,在推进需全员参与的活动时,有其特殊的效果。如前所述在1971年时,日本电装最先实施TPM并获得优秀事业场奖。此后第一代的TPM在丰田关系企业中逐渐普及,南海橡胶工业(株)粉尘现场的改变及故障1/50的逐减实例、爱新精机(株)草席工厂的实例,亦倍受瞩目。 备注:重覆小集团的说明
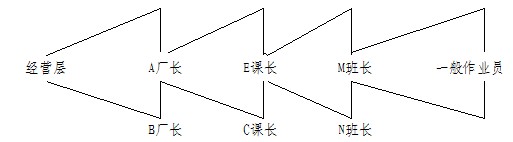 说明:1.经营者与厂部是一个小组。 2.各厂厂长与所属课长是一个小组。 3.各课课长与所属班长是一个小组。 4.各班班长与所属作业员是一个小组。 5.运用上述重覆小集团的运作方式,使上情下达、下情上达,推动全员参与的活动。 2>第二代的TPM 到了1980年,「设备总合效率」问世,以作为评价设备效率化的评估标准。 设备总合效率是时间稼动率、性能稼动率及良品率的相乘结果,在设备效率化的评价上是极为有效的指标。将这些效率指标分别加以探讨,可以发现影响时间稼动率的是故障损失、换线换模调整损失;影响性能稼动率的是速度损失、短暂停机空转损失;影响良品率的是不良修复损失、成品损失之六大损失所构成。而这些稼动率的手法之所以被开发出来,目的就是要分别向影响它们的损失,做「零损失」挑战。 其中特别值得一提的解析手法是PM分析(由JIPM常务理事白势国夫研发而得)以及对应各损失的改善手法。 TPM的推进是以五大支柱(自主保养、个别改善、计划保养、运作保养之技能提升训练、设备之初期管理)来展开。在各支柱中也各有其推行步骤,此为其特色之一。 而最近比较值得一提的,是在自主保养方面,有不二越(株)的保护盖局部化(保护盖少量化)的开发,以及品质之预防保养(品质保养)之开发。 3>第三代的TPM 进入1990年代,在泡沫经济崩溃的同时,为了能于营业额下降仍可维持并保有获利的企业体质,因此「成本导向的TPM」在此时代就显得重要了,JIPM为因应成本导向的TPM时代之来临,便把成本构造与损失结构的关联加以明确化,所以,能够反应成本降低的TPM就因而发展出来。 因此,JIPM提倡TPM的新定义(如图1),甚至把过去的五大支柱再加上三大支柱(品质保养、间接事务部门的效率化、安全卫生与环境)成为八大支柱,让内容更加扩大、更充实,如图2。
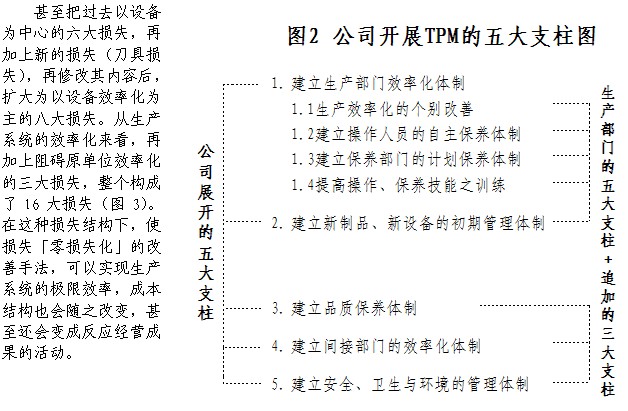 图1 TPM的定义(全公司的TPM) TPM就是: 一. 追求生产系统效率化之极限(总合的效率化),以改善企业体质为目标。 在现场现物架构下,以生产系统全体寿命周期为对象,追求三「零」目标,也就是零灾害、零不良、零故障,并将所有损失在事先加以预防。 二. 生产部门以外,还包括开发、营业、管理等所有部门。 三. 上自经营层下至第一线的员工全员都参与(TOP TOWN方式)。 四. 经由重复最小集团来达成零损失的目标 A. 清扫检查 B.等待批示 C .等待材料 D.等待人员安排 E.等待品质确认/测试调整
 2.TPM现状 1>全球化的TPM 自此以后,TPM便以汽车关联企业为中心而广普及。如今则从机械加工逐渐拓展到家电、半导体、印刷、化学、食品、加工组立型产业,以及大型设备业等。近几年来,TPM优秀奖(1995年开始将「PM优秀事业场奖」正式更名为「TPM优秀奖」)的得奖企业急速增加(如图1),而且,不只是在日本国内,欧洲、北美、南美及亚洲等世界各国亦纷纷导入TPM并加以推行。全球真正推行TPM的企业总数究竟有多少无法精确掌握,日本JIPM协会直接派遣顾问赴海处进行指导的企业约有70家,而日本以外获得TPM奖的企业(如图2)也逐年增加。

 2>赚钱的TPM 最近,TPM的“P”已衍生出“Perfect Production”(完美的生产)的意义;在“M”方面也从过去的“Maintenance”拓展到“Management”(管理)的涵义,而且这种现象均渐趋强烈。 这是因为TPM是针对故障损失、短暂停机损失、速度损失、不良损失等现象进行改善的一种手法。「以零为导向」是它的一大特色;「生产系统的极限效率化」是它的目标之一。而且TPM是以保养为基础,从生产系统的极限化革新开始,反应在企业整体经营革新上,最后表现出成本大幅降低、生产性能提高、不良成本降低、前置时间缩短、库存减少及间接部门的生产性提高等经营成果,凡此种种均可视为管理上的一大革新。 每个企业均会在成本、品质、交期等方面与其它国内外企业产生竞争,特别是在经营策略上,努力追求营业额的增加与成本的降低,以使企业本身拥有获利的能力及条件,对各个企业而言都是极为重要的,日本在泡沫经济崩溃陷于长期经济低迷中时,印证了TPM对于协会企业创造利益而言是十分有效的方法。特别是当时有许多TPM优秀奖的得奖厂商虽因处于经济不景气中而营业额降低,但企业盈收仍持续增加,由此可见TPM的主要特色。另外在无形的成果上,职业环境已改变为零劳动伤害及人性化的工作场所,因而可以提高作业人员的工作满意度。 3>培养人才的TPM TPM活动是使生产系统上的损失结构、设备(工程)及部位之间的关联明确化,进而追求设备环境及设备部位之应有状态,加以复原、改善,并防止再发生,透过这个改善活动,培养过去只会开关及操作设备的作业人员,成为管理设备的生产作业人员。 除了要培养作业人员理解设备、工程加工之原理原则外,还要让他们对这些原理原则的机构、构造及零件名称与机能了若指掌。在这样的设备知识基础上,培养点检设备健康状况的技能、判断异常与设备复原的能力,作业人员便能够达到了「自己的设备自己维护」的境界。 目前,一级的机械保养技能人士(电气类保养除外)有11,626人,二级技能人士有17,963人(截至1994年日本之统计),每年参加考试申请者持续增加(见表1)。其中有许多女性最近也取得机械保养技能士的资格。
机械类保养(机械保养)作业 |
级 数 |
1 级 |
2 级 |
年度 |
检定申请人数 |
合格人数 |
检定申请人数 |
合格人数 |
1984 |
1,170 |
193 |
760 |
240 |
1985 |
1,866 |
823 |
1,598 |
749 |
1986 |
2,265 |
661 |
2,022 |
571 |
1987 |
2,390 |
870 |
2,657 |
800 |
1988 |
2,491 |
1,274 |
2,675 |
948 |
1989 |
2,553 |
785 |
3,252 |
1,032 |
1990 |
2,850 |
1,140 |
4,090 |
988 |
1991 |
2,838 |
972 |
5,534 |
1,984 |
1992 |
3,530 |
1,496 |
7,214 |
2,051 |
1993 |
4,465 |
2,045 |
9,395 |
4,604 |
1994 |
5,377 |
1,367 |
11,452 |
3,996 |
合计 |
31,840 |
11,626 |
50,649 |
17,963 | 二.TPM与品管手法 据说某家企业在应征大专新进人员,QCSTORY(解决问题的步骤)为必考题,解决问题的步骤(现状把握→目标设定→原因分析→对策拟定与对策实施→效果确认→标准化),各家企业名称或作法虽有所不同,但整个架构与逻辑大同小异。当然在解决问题的过程中,所使用的手法有QC七大手法及QC新七大手法、IE、VA/VE、QCC等。 为了让TPM的特色能呈现出来,兹将其定义说明如下: 1. 追求生产系统效率化的极限(总合的效率化),以改善企业体质为目标。 2. 在现场现物架构下,以生产系统全体寿命周期为对象,追求“零灾害、零不良、零故障”并将所有损失在事先加以预防。 3. 生产部门之外还包括开发、营业、管理等所有部门。 4. 上自经营层下至第一线的员工的全员参与。 5. 经由重覆小组集团活动来达成零损失的目标。 TPM所使用的手法与QC STORY观念与逻辑有异曲同工之妙,尤其是WHY!WTY!分析手法,只是表格设计各有不同,就算同样是使用QC STORY各家企业展开的表格也有所不同,在此就不多加说明。 PM分析手法是TPM活动中较为特殊的手法,即然是日本设备协会发展出来的手法,当然它的特色就是站在设备的源头作分析的一种手法。 PM分析是将现象(Phenomena)作物理(Physical)分析,并从结构上(Mechanism)作分解说明,并取其第一个字母组成,最适合用于改善慢性损失,以下示意图说明:
 在解决品质问题时,如果品质不良率很低,但基于某些市场因素或其它因素的考量,必须加以解决时,这时PM分析就是你的好伙伴,当然能够用原有的品管手法解决,就不要刻意用PM分析手法,因为这样会提高工作的复杂程度。 三.TPM活动的品质保养 社会对品质的需求日益提高,因此产品品质的维持与改善以及均质性的确保已成为生产活动中的重要课题。另一方面,生产现场的自动化与省力化日新月异,因而带动了生产主体亦由人工而转移至设备,促使品质的确保与设备状态的优劣具有密切性的影响。 在上述的背景下,以「进行具效率性的设备保养、追求并维持高水准的品质提升」已成为品质保养的基本理念;从设备的管理层面来探讨品质问题,亦是品质保养活动的准则,也是TPM活动八大支柱的重要环节,藉此能建立品质保证体制。 品质保养的定义: 所谓品质保养是「为了保持有完美的产品品质(100%良品),就要保持设备之完美」为其基本思想,从而开展下列各项活动: 1. 以不产生品质不良之产品的设备为目标,来设定零不良之条件,并依时间序列点检及测定该条件。 2. 确认该测定值在标准以内,藉以预防品质之不良。 3. 观察测定值之变动情形,预知发生品质不良之机率,以便事先采取防患对策。 为了防患由于设备及加工条件所引起的品质不良于未然,可将品质保证活动与设备管理活动结合起来,藉以探讨品质特性与原材料条件、方法条件及设备精度等之关联性,以便设定不产生不良之设备条件。这种条件设定,就是将不良要因明确化,亦即为了生产良品,就应该设定并维持其原材料、加工方法及设备精度等条件,且以自主保养活动与技能教育训练所培养出对设备专精的操作人员为基础,进而谋求对所设定之条件进行维持管理,以实现零不良之目标。以上所述就是品质保养的基本思路(参考下图)。 品质保养的基本思路:
 此一测量值在超过所设定基准值前就能采取对策之做法。 推行品质保养的前提条件 要实现「经由设备制造品质」,就必须做到以下几点: 1. 彻底排除强制劣化,而保持只有对自然劣化所进行之「安定的设备状态」。 2. 从管理者到操作人员对设备具有专精为其前提条件,且必须满足下列四项条件: 1> 实施排除强制劣化:在设备具有强制劣化的状态下,即使要管理设备精度也会受所构成零件寿命变短,且很难进行点检。 因此,必须透过自主保养活动,彻底推行排除强制劣化,并减少零组件之寿命不均匀,并追求寿命之延长,才易进行品质保养。 2> 培养对设备专精的人才:管理者理应要使操作者对本身的设备很了解,同时也要使他们具备维持管理之能力;换言之,为了要实现「零不良」必须维持「人、机系统」的平衡状态来从事生产活动。 因此,必须培育具有能及早发现「似乎会产生不良」之异常原因及能迅速对该异常采取正确措施之操作人员。为了使生产部门的操作人员能对设备具有专精,实施自主保养、个别改善、PM分析研习会及技能训练就变得很重要了。 3> 设备「零故障」运动:在推行品质保养上极为重要的是要将设备停止型故障及机能降低型故障减少到「零」,尤其是要将品质与设备(设位、零件)条件之关联明确化,并能开发与应用诊断技术,期能以此诊断技术判断其劣化之条件。 4> 新产品或新设备之MP设计:从产品设计或设备设计阶段,就必须建立起不会产生不良产品或设备之制造体制。 有关品质保养与TPM活动中各支柱(各活动)的关系,可如下图所示:
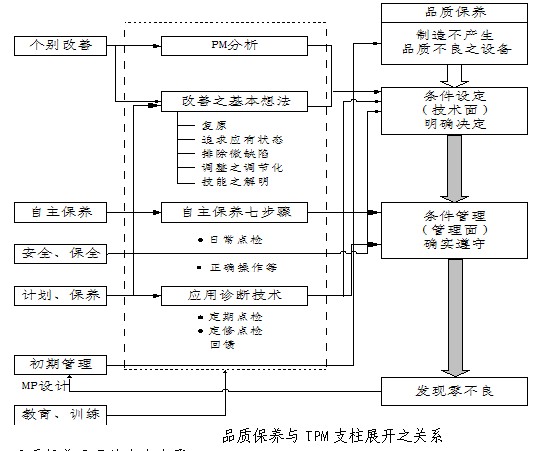
品质保养展开的十个步骤 品质保养的十个步骤展开如下表所示,其活动手法旨在于进行不良现象之确认、不良发生工程调查、3M(原料、设备及方法)条件调查分析、3M条件不适合之对策检讨和复原、良品化条件不确定者之解析评估与3M条件缺陷改善。 品质保养的十步骤
步骤 |
内容 |
注意点 |
品质改善 |
准备 |
1 |
现状确认 |
(1) 确认品质规格、品质特性
(2) 制作QC单位工程流程图
(3) 品质不良状况与现象之调查层别 |
应维持之产品品质特性值要明确化
设备系统机构、机能加工原理、顺序等要明确
掌握工程品质不良发生状况
层别不良现象
发生不良现象单位工程要明确化 |
调查分析 |
2 |
发生不良工程调查 |
制作QA矩阵,并对不良项目这发生单位工程调查 |
单位工程与不良项目之关联性调查 |
3 |
3M条件调查分析 |
(1) 单位工程别之3M条件调查
(2) 指摘出现场调查上的不完备点 |
依图面、标准、指示书等调查3M条件
依加工原理、设备、机能,追求3M应有条件
现象调查后,要明确3M条件设定,掌握不完备点 |
改善检讨 |
4 |
问题点对策检讨 |
(1) 制成问题点一览表,加以检讨对策
(2) 设备状态之确认与复原改善 |
于自主保养活动之维持状态的确认与调查加工条件,换模方法,并复原问题点
不能只满足设备条件之设备改善 |
5 |
解析良品化条件不确定者 |
(1) 良品制造条件不确定者之解析
(2) 以实验来设定应有状态 |
回归加工原理原则,毫不遗漏的追求加工条件与设备精度之关联
整理同一设备有复数之品质特性问题时,设备之各部位对品质特性之影响程度
依PM分析、FMEA、实验计量法来追求不良要因与3M之关联,并设定品质制入3M条件
为保证品质特性值保持在规格内,应决定设备精度,加工条件之暂定容许值(暂定基准值) |
改善 |
6 |
改善3M条件缺陷 |
(1) 将3M条件之缺陷显示出来
(2) 实施改善
(3) 评估结果 |
依解析结果之3M条件项目实施3M之点检、调查
指摘出问题点,追求复原与改善
将所有点检项目纳入暂定容许值进行确认品质特性是否能满足规格值 |
7 |
设定3M条件 |
设定能制造良品之3M条件 |
|
品质保养 |
标准化 |
8 |
点检法集中化改善 |
点检法集中化、固定化之检讨与改善 |
将点检项目分为静态精度、动态精度、加工条件,以期将项目能集中以便归纳
同时可进行短时间、容易进行点检之改善 |
9 |
决定点检基准值 |
(1) 点检基准值之决定
(2) 制作品质保养矩阵图
(3) 点检依赖性提升、简单化、省人化 |
为将品质特性值纳入规格内,把设备精度容许值(基准值)以振动测定法等来设定代用特性值
除了需要特别和测定技术或分解点检需要技能与时间的项目外,皆作为生产部门之点检项目
检讨点检依赖性之改善、简单化、省人化,并实施改善 |
10 |
改订标准 |
(1) 改订原料标准、点检标准及作业标准
(2) 标识可遵守的Q组件
(3) 倾向管理与结果之确认 |
管理者应对圈员说明为什么要做这些点检,并依据设备机构、构造、机能或产品加工原理实施教育
点检基准之追加由圈员自行追加
透过倾向管理,在未超过标准值之前实施对策
在所决定之标准以外的品质问题发生时,应进行基准值之修订与点检项目、方法之检讨 |
以品质保养活动来设定不产生不良的3M条件,并使其易于遵守,且以点检项目之集约化、点检基准值之设定来落实条件管理项目之标准。上述条件管理与倾向管理为品质保养的两大活动。 品质保养展开,所牵涉范围广泛且技术层次较高的宜以「课长」为中心来组织专案小组;比较顺利的做法则是以组长为主体设定「零不良」之条件,并采取以维持管理为主之自主保养活动的方法来进行极为重要。 品质保养展开的要点 以下用实例说明有关品质保养各步骤展开的进行方法。 第一步骤:现状之确认 这个步骤是为了设定品质保养活动之基准点和目标值而所进行的现状调查,并且也是使品质保养活动顺利进行之推动计划的一个重要步骤。 经由确认对象产品之规格值,发掘可能达不成规格之所有品质特性不良项目;其次,进行制作品质制造、工程流程图、不良发生状况与现象之调查与层别,并将这些不良、客户投诉以及因不良而进行的检查,全部均换算为损失成本,让全员都知道。总而言之,品质保养的第一个步骤的注意要点有: 1. 品质规格、特性值之确认:掌握产品规格、特性值与制造规格、检查规格,并应将其维持的品质特性自确化。 2. 制作单位工程QC图:制作单位工程QC流程图,使设备、系统之机构、机能、加工原理顺序等明确化,并调查在单位工程中为维持品质之管理项目(如基准、方法等,如下图示例)。
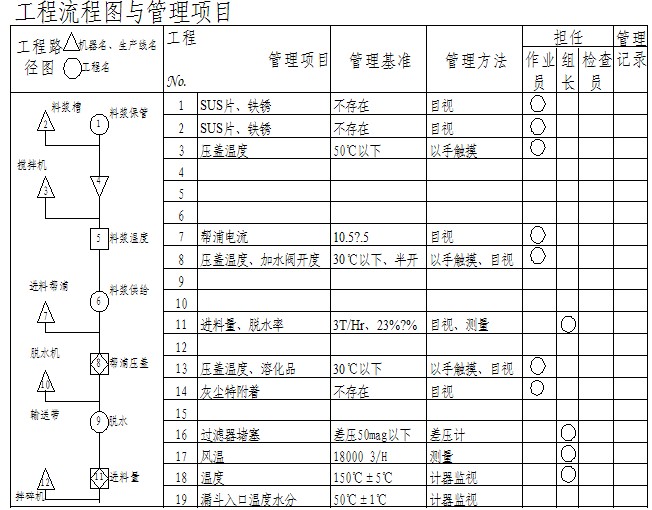 3. 品质不良之发生状况与现象之调查与层别:在工程中掌握不良发生状况,并将该现象作层别,使其发生的单位工程明显化。简言之,将不良现象彻底做层别,是不良对策之第一步。 4. 目标设定与拟定品质保养活动推行计划:以现状调查结果为基准来设定活动之目标值,并拟定活动推行计划。推行计划可以主要产品为示范。先行实施,然后再向其它产品水平展开。 第二步骤:发生不良工程之调查 在这个步骤中,就是将在第一步骤所要明显化之单位工程与不良形式的关联性进一步加以分析,再作成下图所示的QA矩阵图,以便调查分析可能在哪一个工程会产生品质的不良,哪一个工程的设备或方法条件变化时会发生不良等关联性。并与过去实际不良情形做重要度分析。
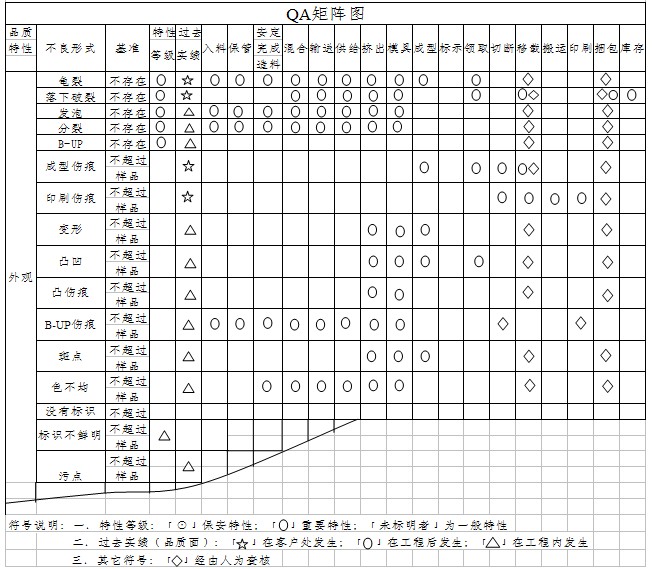 第3步骤:3M条件调查分析 这个步骤是经由所建立的QA矩阵图来掌握单位工程的品质不良形式,进而去了解使用什么样的原材料?什么样设备?什么样的方法及什么样的点检以防止再发生不良。传统上,4H条件是以「什么」为开端,调查图面、标准与现场现物,如下图所示,进而找出不会产生不良之条件,再就这些条件调查与基准相比较,或是否与基准实行上模糊不清,或是否基准法无法遵守,或是否缺少必要的基准等而来加以判断。 一般而言,条件、标准尚未决定或在不明确的情况下,任由现场人员加以判断进行者占20%-40%,宜改善之。
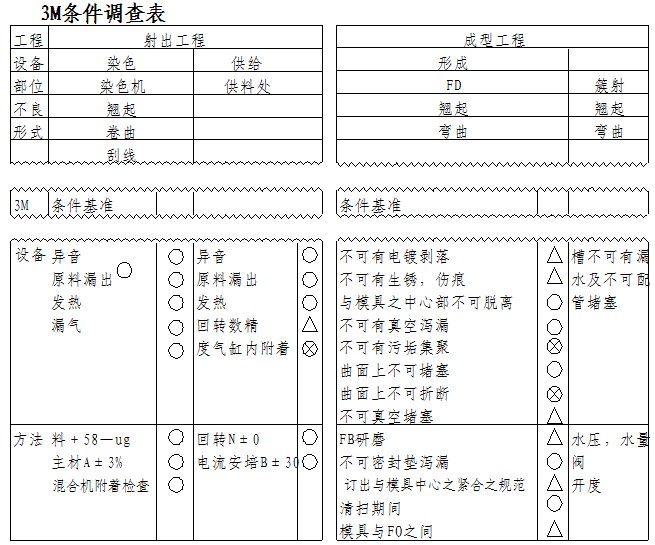
第4步骤:问题点对策检讨 本步骤是将第3步骤的3M条件的问题点,依工程类别加以抽出,并制成问题点检项目一览表,然后再检讨问题点之对策,就应决定对策改善之担任者,并付诸实施;而不能立即采取对策者,将于第5步骤中再予以检讨。 第5步骤:良品化条件不确定者之解析 本步骤是为了解析第4步骤之问题点对策中制造不良品之不确定条件,再加以调查分析。再运用PM分析、FMEA及实验计划法等手法来检讨对策。 下图为PM分析之案例介绍,以供参考。
 第8步骤:点检法之集中化改善 本步骤是将第7步骤所设定之3M条件全部明确化,其条件必须全部加以点检,为使点检出之不良情形不再发生,因而其点检项目较一般点检项目还要多,更要全部做点检。但其在维护管理上实有困难,所以必须依下图之步骤,将它集中化与固定化。

 第10步骤:标准之修订与倾向管理 本步骤系为了不产生不良,对所设定之各要因条件是否有效维持及按规定的周期、方法确实点检,并对其变化的程度必须进行倾向管理,且为了建立这种条件管理体制,除了生产部门外,保养部门也有必要实施有关点检教育训练,并依下图所示之步骤进行指导,并让其反应各种基准书、标准书。 基准化之展开概要:

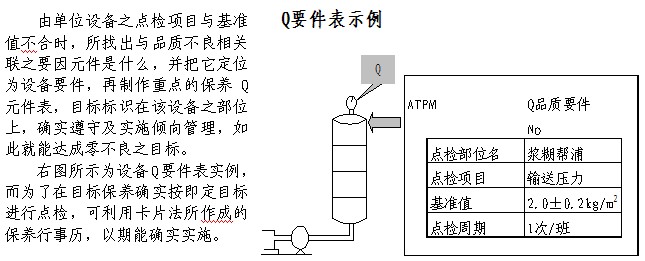 四、追求工业安全零事故的新思维(TPM之有效运用) 日本最近在TPM的改善范畴里,有关自主保养、个别改善的进步非常惊人。「目视管理」、「机器设计改善」、「发生源对策」、「少人化」、「作业改善」,甚至「工厂全体的损失分析」等,其水准都是以前的TPM活动所不能比拟的。目前工厂的生产革新或因为TPM活动的导入生根而有所进步,但关于工业安全的部分,TPM却未得到有效运用。本节将探讨如何藉由TPM的运作,使工厂的生产革新与工业安全的提升能够同时达成。 以TPM来确立工厂安全管理的目标 工厂的生产革新与工业安全的提升表面上看来互不相干,想要同时达成通常会被认为是不可能的。另外工厂的生产力提升与少人化要同时完成,一般出认为有困难。 然而却可由推动TPM活动同时解决这种互相矛盾的问题。整理TPM的特征,可以归纳为以下四点: 1. 能够以步骤方式来展开(如自主保养等); 2. 目视管理、机械设计技艺、发生源体系化; 3. 损失的指标、改善顺序的建立及成果的定量化; 4. 环境与安全的重视。 在日本工厂里工业安全管理活动中经常运用的方法有:惊吓警惕法(near-accident activity)、危险预知训练及动作复诵确认法等。这些方法是与作业员个人或小集团为中心来主导推行。其效果仅止于螺旋上升式;结果,使得大部分的工业安全活动流于公式化,而少有新意,故对新工业安全活动的开发显得更为重要。 TPM活动的自主保养、个别改善、计划保养、品质保养活动里,步骤展开的顺序已被建立,同时,操作人员教育步骤的课程内容也整理完成。所以如能确实地实施TPM,在三年的活动中可以完成上列所要求的六大步骤。对于工业安全的部分,TPM出是非常的重视,只是目前步骤展开的方式仍未建立。此外,关于「安全的目视管理」、「对防呆法下的工夫」及「发生源的指南与对策」等战果,若与自主保养及个别改善相互比较,TPM发展显得较慢。 比如说经常提到的自主保养,是将一些慢性的状况问题点以PM分析来使真正的原因明确,然而TPM的工业安全活动中,PM分析用于事故原因分析的情况却不多。这主要是人的思考方式的表现。 正视工厂安全管理上的诸多问题 一般工厂在日常生产活动中安全管理主要存在下列几个方面的问题: 1. 追究事故的原因时,常有一种为了责任不要波及管理者或作业人员的心态,以致发生的原因常混沌迷离而呈模糊状态,而真实的原因(发生源)无法被明确认定。 2. 未培养在工业安全方面专精的技术人员,故无法系统的追究事故的原因及建立对策。工业安全活动未在强有力的领导能力之下被推动,也没有相关的权限设定。 3. 即使是主管或是工业安全方面的技术人员,也无法将事故的发生源以「现场、现物、现象」三个方面来使其明朗化,往往仅以护栏、扶手、或安全防护罩等治标不治本的方法来作为解决对策,最后不了了之。 4. 并未开发出除惊吓警惕法、危险预知训练、动作复诵确认法之外的新的工业安全活动。即使发生许多工伤事故,但仍然重复着类似的作业,并未以作业解析的结果来对应废止哪些属于不良作业或危险作业。 所以,从未开展TPM活动前的种种限制因素,即使到了现在,TPM在工业安全方面的活动仍未充分展开。在以前利用三种工业安全活动来减少工业安全事故的发生,在过去还显得很有效,然而基于现在的设备规模扩大、自动化的提高,人的思想也跟着改变。在工业安全方面,特别是「自己的安全自己保护」这一类,到目前仍非常闭塞,问题点仍未被解决。 举例来讲,对电车司机而言,运用「动用复诵确认」来确保安全的达成是较为有效的方法,而类似的土木建筑(或几乎每天的作业现象都在变换的状况下),则是采用「危险预知训练」会更具有效果。那么,惊吓警惕法适用于什么情况呢? 在日本有一家工厂,曾出现一年高达一万件惊吓警惕案例(惊吓警惕法),在过去十五年间,该厂工业安全案例不间断地被发现,工厂安全负责人这时在想,有这么多的工业安全案例的话,工厂何不运用一年或更长的时间把它(工业安全隐患)全部指出来,然后再专心思考对策,但对于这样的建议,得到的回答却是「如此一来没有预算会很困难」,得不到明确的答复,到最后还是不了了之,另外一个例子是,在经常会发生夹伤事故的工厂里,让它们以「夹伤」为主题,将所有作业及设备的安全问题点整理出来,结果也几乎没有回应,或许站在工厂的角度来看,这种被夹伤的作业及设备在工厂一直存在着,本身就属于工厂的内部问题,如果太深入追究,反而会引起不必要的困扰,如资金投入等方面。 惊吓警惕案例是指将现场内潜在的危险、不安全的动作及状态等由各作业员指出来。然而,事实上危险的问题(如夹伤事故)并没有被指出来,另外即使指出来了,也会出现「自己的安全要由自己来保护」的推诿之词,结果使工业安全管理变成形式的活动,或只是工业安全小组车间行事历上的一件例行公事罢了。 不过事实上也有些工厂用关键字(如以常出现异常状况的部位、夹伤……)提出工厂日常生产活动中可能会发生工业安全问题的部位。再汇集近几年的案例,并依「重、轻、微」等级加以分类,再针对「重」的部分来实施对策。这种情况也有部分工厂在实施。 如果要求工厂的计划保养小组「使用惊吓警惕案例、危险预知训练及动作复诵确认等方法,使事故或故障变成零」的话,一般会被以「这样的事是没有办法的」的回答来拒绝,所以工业安全上所使用的手法亦有其特有的部分,有些并不适合应用于其它的领域上。 另一方面,计划保养里虽然开发能使故障及问题达到零的手法,但却不一定适用于工业安全方面的问题,为什么呢?会出现此种现象的证据就是,在保养的施工现场、工厂的作业场所里,常常只是不假思索地依照工业安全小组的指示,信依样画葫芦地进行了三项活动,而丝毫没有对这种方案抱怀疑的想法。此外,包括制造、研发的小组在内,对于工厂全体的安全活动也少有关心,造成这种现象的产生。 在这里需要重新界定清楚的是,并不是在谈论这三项活动(惊吓警惕案例、危险预知训练、动作复诵确认)对工业安全没有确实的帮助,只是,并不是代表实践了这三项活动,就可达成工业安全零的目标。 依TPM活动来进行工业安全管理的原则 依据TPM的工业安全管理,其基本原则为:「凡可能导致劳动灾害、工业安全事故的发生源,务必使其明确化,且要用心考虑其对策并加以实施」。正如将「以设备来确保品质」的TPM活动之品质保养运用在工业安全上的话,那么TPM的工业安全管理即成为「工业安全的达成要以设备来确保」,以达到「设备本质的安全化」为工业安全管理的终极目标。 在「夹伤事故」经常发生的工厂里,若不改善可能发生事故的作业方式,则欲使安全事故降到零乃是缘木求鱼。而如果将发生源置之不理,只是要求「要小心操作」的话,也不可能了解到要注意什么才好。即使是询问「在工厂里可能会产生夹伤事故的场所有几个?可能会衍生如此情况的是哪些作业?是否已将其全部指出来」,这些方面经常会被遗漏。 如下图所示,对工业安全的处理上有欧美式的Top Down及日本的Bottom Up两种类型,Top Down的研究是采用故障树(Fault Tree)分析的手法,可以定量地评价大规模系统的安全性,诸如运用于航空、核能、化工产业的问题上。Top Down研究是宏观的、战略性的、理论性的。为了能显现出定量的评价,收集故障数据,示范统计并予以数据化仍是必要的,然而此项举措可使设备的故障降低,但对现场的工作进行方式要求不是很强,可以请专业的顾问来工厂进行推广。

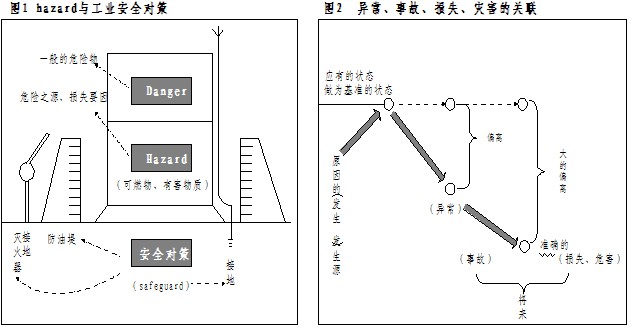 即使是发生事故也不见得一定会产生灾害。惊吓事件即是一例。不过只要是事故发生,产生灾害的比例相当高(这一点由惊吓警惕法则可以获得证明)。 灾害为巧合所支配,有许多不确定因素。为了要使灾害消失,消灭事故较具有效果,这也是惊吓警惕法则的结论。换言之,灾害、损害可以用下列公式来表示之。【灾害、损害】=【事故】+相当比例的【损失、灾害】。如能防止所有的安全事故,则任何灾害将无由发生,此为最有效的工业安全政策;我们称之为预防对策。工业安全的研究对象为人祸(人为灾害)的部分,人祸是可以预防的,最有效的方法便是重视预防对策。防止产业灾害(损失),除了人为灾害的预防对策外别无其它更有效的办法。 灾害统计的参考数值 为了要将工业安全管理的实现成果,做出比较或判定以建立对策,针对过去几年的劳动灾害数据加以统计是必要的。现在常被使用的灾害率有:年千人率、度数率、强度率三种(如下表): 经常运用的灾害统计公式:
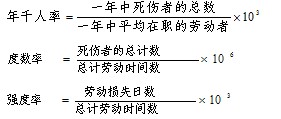 「度数率」指的是:劳动时间每百万小时,依劳动灾害发生所导致工作能力丧失的伤害件数。假设一个劳动时间为两千小时,从业人员有五百人规模的工厂,合计劳动时间一百万小时,如果每年内发生一件伤害事故,则度数率为一。 至于在「强度率」的劳动损失日数的论定方面,死亡或永久无法劳动的7,500日计,其它残存的伤害,则依程度不同而有一定的日数基准。在这里所提的无法到职工作灾害,是指为了治疗因业务上所造成的病痛或灾害而无法工作,必须停工(休养)的工伤或疾病而言。 不停业灾害指的是因业务上造成的病痛或灾害,虽然将来还可以工作,但从发生到治愈,必须持续十日以上每天到医院接受治疗。如果十日以内可以完全治愈的,则称为轻伤灾害。此外,若轻伤灾害中,有只涂药水不需要特别加以处理的,也可以称之为经红药水灾害。 机器设备本质的安全化 是人,就会犯各式各样的错误,因为机器或设备的设计、制作、运转、保养、变更等,时而会发生误操作、误动作、误判断等,并且机器或设备也会发生短暂停机、故障及出现其它状况的可能性。 度想像下列这样的情况: 一. 即使操作人员发生误操作、误判断的情形,也可以在酿成事故或灾害之前,让机器或设备停止的「防呆设计」(fool-proof)。 二. 机器或设备的一部分发生了异常、故障,或有不可控事件发生时,但并不会波及全体,因为其中设定的只在安全范围内运用的安全装置(fail-safe)。 类似这类化学安全化对策的内容,就是所谓的「本质安全化」。而「防呆设计」指的是如果自动机械的安全栅栏门被强行打开时,运转中的机器就会立即停止运行;或是动力传导装置的安全盖被拆卸时,运转中的机械便会自动断电停止的一种装置。至于「fail-safe」方面,例如铁路列车在侦探到线路或架线出现异常时,会自动停止一种特殊安全装置,有了本质的安全化装置,其工业安全管理才能落到实处。 TPM最重要的一点,就是要把所有所谓的问题发生源,很明确的将之凸显出来,然后再去做出对策(所谓「发生源」一词的用语,在TPM设备管理用语辞典中是以「the source of problems」来表示,但是就企业的经营者来看,应用「root cause」的英文来表达更为贴切。换言之,TPM的首要任务就是要了解「问题根源」之所在。 其次是,为什么推行TPM要用三年的时间,这是因为从恶性循环转变为良性循环所需要的时间,必须经过如此长的时间才能毕尽全力,而事实上不管是哪一家工厂,在TPM导入前,都经常会发生问题与故障。而作业人员与保养人员也非常的忙碌,由于工作繁多,再加上检讨不够充足,所以结果就是根本无法找出解决发生源的对策。有时甚至只中为了因应紧急处理的需要,而采取治标的解决办法。为了能彻底杜绝这样的恶性循环,并使其转变为良性循环,企业就更需要在导入TPM后,以三年的时间来进行改善活动。 依此进行后,一种初斯的良性循环才能形成,而且这不仅可以使故障与问题的发生相对减少,工厂也就能更进一步进行更有前瞻性的工作。这是因为有了充分的检讨作业,所以能够批出发生源的对策而彻底解决问题,一旦故障与问题减少了,企业就会更专注在创造高水准的品质与工业安全问题上。 为何TPM可以使工业安全变得更为完善 每个企业有库存管理、工程管理、物流管理、作业管理、目标管理、工厂管理及单价管理等,其它还有左图所示的种种管理技术。
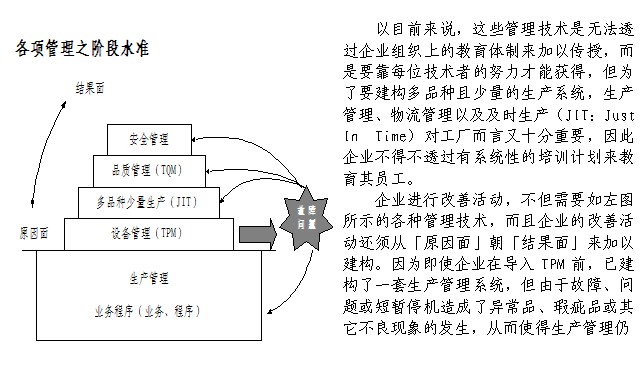 无法充分发挥其机能,更与其管理机能是否能够完全发挥有着密切的关系,就企业的整体运作而言,如果无法摆脱恶性循环的事实,随后所衍生的问题将持续接踵而来。 事实上,在一个故障与问题频繁发生的工厂中,想要奢谈提高品质与工业安全的水准是绝不可能的事。
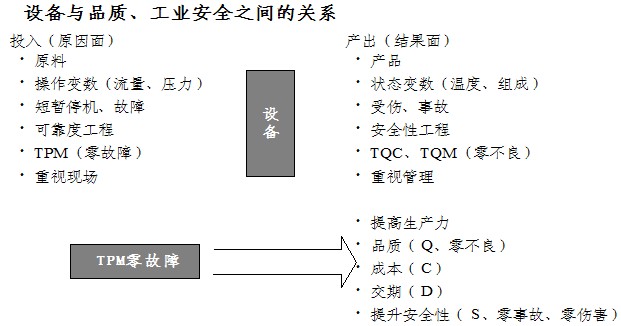 如上图所示,影响设备的变数,可分为「投入」(原因面)与「产出」(结果面)两类。工业安全与品质可归为结果面,而故障、问题与短暂停机则为原因面。以下针对这两个层面做更祥细的探讨。以下图的热水器为例,水的入口温度、水的流量、瓦斯的流量是「投入」。其中,水的流量与瓦斯的流量是可操纵的变数,如果加以调整则出口的温度也会改变,所以出口温度是「产出」。水的入口温度无法直接调节,因为这是由外部的要因来决定,这就是初期的条件。
 管理上的过失与危机的分析 所谓的MORT,就是指“The Management Oversight and Risk Tree”的简称,在此右解释为「管理上的过失与危机分析」。MORT与Fault Tree类似,不过在管理上,Risk Tree的说法更可以把过去及缺点的意义明确的表现出来。 在1969年,W.G.Johnson以系统安全解析的手法,提出MORT的基本概念。1971及1973年,先后出现MORT第一版及第二版,其后更在1980年汇集了MORT的成功案例,发行MORT解说书,同时也发表了一些有关化学工厂的应用实例。 如果将工厂内所经常发生的事故加以分析,不难发现其原因不外在人员、设备、管理及媒介物四类。然而一般说来,调查工厂事故发生的原因中,大部分是针对工厂硬体设备来加以检讨,对于软体方面,如管理等,其重要性并未在调查检讨中充分明确的显现出来。因此,MORT把管理上的问题一并涵括在内,以协助企业全面地去了解事故发生的原因。 但是MORT并非只局限于在事故发生后去思考应对策略,它甚至可以为产业安全提供出预防对策并加以活用。换言之,由于MORT可以针对目前各企业对工业安全问题上的想法、管理上的体制、潜在的危险等问题加以分析,因此,更能明确工业安全上的弱点及对应策略。 依据MORT的概念,所谓的「异常现象(incident)」可能定义为「不希望发生的能量转移(能量变化)」,而所谓的「事故(accident)」,则定义为「对人员造成伤害,对设备形成损害,或在制程中造成运转性能下降的异常现象」。 所谓「异常(abnormality)」的定义通常是指「偏离某一基准」,而在MORT中,则更具体地对其加以定义。例如:人员从楼梯上跌落或物品从高处掉落,这些都是工厂中最不希望发生的能量转移事件。再如有害气体自容器中外泄而导致扩散的情况也是企业最不希望见到的能量释放。 在MORT中,还要考虑到的一点是,「事故的发生是因为多种重要因素所造成的」。这也就是说随着异常现象的产生导致不希望发生的能量转移,而且因为此一能量转移无法被阻止或控制,所以才会发生事故。 通常在初期,首先会在计划时或运转中出现错误,随后再加上未能对人员或环境的要因变化做出正确调整,就会造成事故的发生。像这样如果没有按目的加以调整的话,不安全的条件及不安全的行动就会接边发生,并使得有关的企业活动爆发危机,接着因为不安全的条件及行动,就会造成不希望发生的能量转移。 能量转移的种类 某些不希望发生的能量转移一旦发生时,会造成人员伤亡、设备受损。能量的转移大致分为以下几项: 质量、重力、高度; 直线运动; 旋转运动; 压力、容积; 腐蚀性; 毒性; 病源性; 爆发性、自燃性; 可燃材料、电力; 热辐射; 其它高温物体; 核能辐射; 电磁及电子辐射; 音响辐射。 如能将能量再加以分类,可以归纳出以下几项是可以善加利用的: 异常现象的发生会有助于状况报告书的作成; 以能量(电压、热量及压力等)大小变更作应对策略; 开发防止对策及以系统为对象的情报; 资料收集。 下表将不希望发生的能量代表案例一一列出。就目前来看,劳动伤害如夹伤、滑倒、摔落等事故,都是以现象为中心来检讨其安全对策。但在MORT,则以不希望发生的能量转移与释放出来假设异常现象的发生,这一点与TPM的寻找发生源与对策的想法,如出一辙。 能量转移和释放之代表案例:
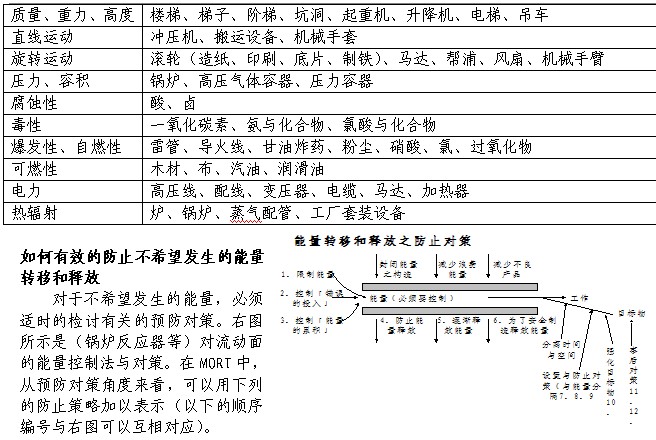
1. 限制能量(使其转换为更安全之事物) 在工作上使用必要的最小能量。例如,必须以手加以取用处理时,应以最轻量进行;有害物质应选择最小容器存放;在某些特定区域中禁止车子的行驶;使用毒气最低的化学物品或采用容易保养乃至不需要保养的设计。 2. 控制「错误的投入」: 以即使是错误操作或错误投入,也不能造成系统故障的方式来控制投入。例如,对过电压装置回路断路器;手术时为防止误认氧气而对病人施放麻醉气体,可以使用颜色管理的方式,同时以不同型式的接收口,来易于区分氧气及麻醉气体。 3. 控制「能量的蓄积」: 亦即以信号的控制装置来防止能量的蓄积。例如,微动控制器、调节器、断路器、气体检知器、温度检出器等设置。 4. 防止能量释放: 是指把危险的物品覆盖起来的一种设计。例如,于管线设置热绝缘体、被覆电线以隔绝热量;再如防呆阀及连锁阀的设计亦是同样的道理。 5. 逐渐释放能量: 例如,破裂板、安全阀、安全带、缓冲机等。 6. 制造释放出能量的管路、分离空间与时间: *在空间的分离方面,如车辆与行人的交通分离;接地、隔离有害的爆裂物质;管路的明确标识、禁止入内的标志等。 *在时间的分离方面,如开警报与撤退、爆破与保养的时间。 7. 阻绝能量的对策: 例如,自动淋水灭火系统、围墙、屏障、防护服、噪音隔离等对策。 8. 阻绝能量与人员、设备间的对策: 能量的释放,要尽量不影响远方,如防火窗、隔音天花板、焊接保护罩、安全网(如马戏团表演中所用的安全网)。 9. 阻绝人员或设备的对策: 例如,人员的防护器具(如护目镜、安全鞋、安全带、防毒面具、手提袋)及汽车的安全气囊等。 10. 提高损害的界限值: 选择抗损力较强的材料及意志力较强的人员。 11. 事故后的对策: *防止二次的灾害:如阻绝能量的释放、禁止通行、隔离危险区域等。 *人员与设备的救护; *灭火; *准备紧急医疗班。 12. 复健 人的健康及工作能力的复原、设备的修理等。 上述各项防止对策采行的具体案例: 大型电动马达、压缩机的皮带、链条的安全罩的阻止对策: 8.中间阻止政策(阿拉伯数字8,系对照前述各项能量转移与释放的控制法与防止对策)。 本章16页的油缸安全对策: 5. 逐渐释放能量:装置安全阀; 6. 制造释放能量的管理:电器接地; 7. 阻绝能量的对策:泡沫灭火器; 8. 中间阻止对策:设置防油堤。 研磨机的安全对策: 1. 限制能量:降低转速; 4.止能量释放:刀刃的支撑、台架的支撑; 7.阻绝能量的对策:利用保护罩; 8.中间阻止对策:利用玻璃护罩; 9.阻绝人员或设备上的对策:护目镜。 五、案例1:用TPM建构工业安全的良好环境 TPM是一种很好的降低成本及企业竞争力的管理手段,台中三洋公司于1995年2月正式引进TPM的管理活动,并制订1995年2月为导入准备期。紧接着展开了一连串活动。聘请日本生产保养协会(JITM)的顾问来本公司做为期两天的预备调查,确认目前TPM的管理现状,并规划了今后TPM活动的方向及辅导的方法。 为了使整个活动能顺利的展开,三洋公司成立了TPM推动专职单位「TPM推进事务局」,开始展开向TPM优秀奖挑战的目标迈进。在尚未全面展开之际,先由部门主管到基层组长组成了六组的示范设备,并于六个月的誓师大会上向全公司人员发表活动的成果与感想,使全员对于TPM有更进一步的认识。 在举办过TPM誓师大会后,全公司的TPM活动于是正式全面展开,经过全员的努力,现已经取得相当的成绩,在每人生产量、设备总合效率、客户投诉数量、设备短暂停机件数、设备故障件数、修理费用、(在制品库存)前置时间缩短、劳动灾害件数、提案件数等九大项均有杰出的改善成效。 工业安全稳妥下的基础工程 TPM推动的架构是以5S—整理、整顿、清洁、清扫、素养为基础,并以活动的八大支柱:自动保养活动、个别改善活动、计划保养活动、设备初斯体制管理活动、品质保养活动、安全卫生环境管理活动、间接部门效率化活动、教育训练活动的展开来达到全员的意识改革,使人与设备的体制得到改善,进而使企业达到经营的效率化。 在这种架构下三洋公司展开了各支柱的活动,多次请外界顾问来厂辅导,及时发现工作中的不足之处,并做好相关的跟催动作与指导,现场配合整个活动的开展,将所有的设备及人员编成5S小组开始展开活动。从第一阶段初期清扫到第七阶段自主管理,每一步骤均彻底地实施,且要善于利用自主保全的三大利器「活动看板」、「会议」、「一页一心得」(工作报告)来达到这项活动所希求的「自己的设备自己来维护、自己的工作自己来整理」的目标。
至于整个活动过程中,除了自主保养中小组为主干外,并配合一些独特的改善手法,如5W1H、VA/VE、田口式工程等,与PM分析手法等来彻底改善生产系统中所有的损失,提高生产效率,以达到设备总合效率之最高极限为目标。 当然,除了提高生产力之外,对品质保养、设备的初期流动管理、事务间接部门的效率化及全员知识技能的提升均大有帮助,而这些均是在活动过程中必须的项目。然而,这些目标达成后,并不能代表整个活动的成功,因为还有一项最重要的就是「职业安全」,所以在八大支柱中特别强调安全卫生环境的管理。 三洋的工业安全防护措施 三洋电子在导入TPM活动过程中,除了设置安全卫生环境管理分科会来执行整个工厂的安全卫生管理外,还特别指示在「与环境共生」的环境政策前提下,向ISO-14001认证挑战,并设立了环境部,在1995年荣获安全卫生五星奖,在此基础上,从1996年1月起导入系统的认证,短短一年就取得了SGS ISO-14001的认证 然而,取得ISO-14001的认证并不是TPM的满足点,推动此活动的目的是藉由TPM活动来创造出设备、作业、人等无事故系统的架构。从最基本的自主保养小组活动开始,第一步骤初斯清扫(点检),藉由清扫的过程发现设备的问题点,将设备微缺限及强制劣化的场所呈现出来,并将问题点贴上「问题标签」(如下表所示),从而进行复元或改善,且将改善点或问题点制成One Point Lesson,做传达教育及再防止等活动,其它步骤也依序推进。
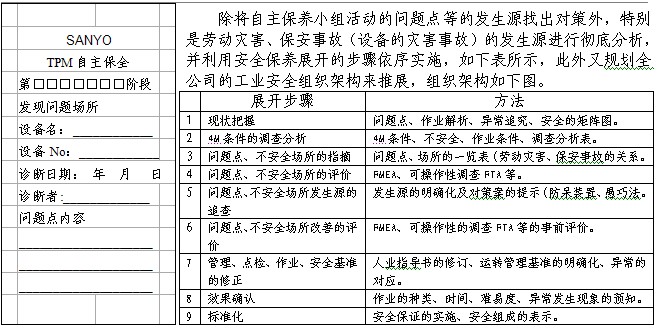
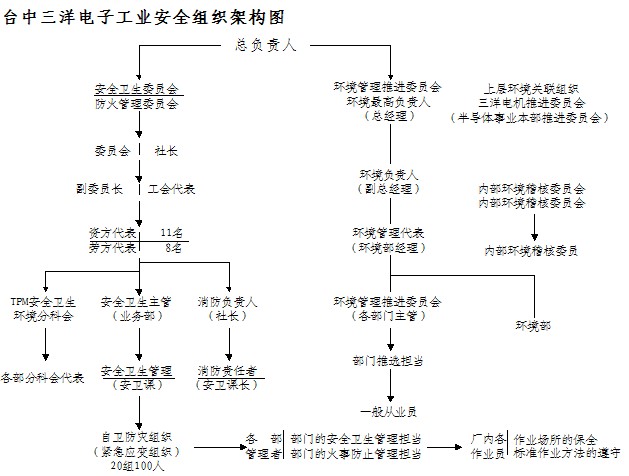
另外,同时也需运用TPM八大支柱之一的安全卫生环境管理分科会的活动,制定了若干活动计划及实施了各项零事故、零灾害的活动,如下表所示:
工业安全活动措施
活动项目 |
活动内容 |
劳动灾害预防 |
.零灾害奖励活动
.安全巡查的实施(回/月)
.定期的自动检查实施
.安全月间之设置与实施 |
健康管理 |
.新入社的健康检查
.特别作业者的健康检查
.一般人员的定期健康检查 |
环境管理 |
.ISO-14001认证取得
.一般环境测定的实施(照明、噪音等) |
安全卫生
教育训练 |
.新人安全卫生教育训练
.危险预知训练
.紧急应变组织的教育训练
.火灾预防的教育训练 |
利用Why5次来找出灾损真因
由上述各项活动及结合个别改善活动,彻底来扑灭现场中的一些人安全事项,经过两年多的努力,台中三洋公司已得到预期之效果,从下图中可以看出。
当然,TPM活动并不是解决问题的唯一途径,但它是一个值去尝试的管理手法,特别在最近连续发生的一连串的工业安全事故及灾害,都是值得大家思考的,它的因果关系是什么?所以大家能利用TPM常用的5W Image的分析手法,也就是说,每一件数均要追求为什么?为什么?Why 5次找出原因。 因此,如果对于每一个问题点均能Why到W-5的话,应该都能找出问题之症结之所在,当然对于事故的发生也可以避免而真正达到TPM的基本目的:从事保养(Break Down Maintenance)转变成预知保养(Predictive Maintenance)。
六、建构化解工业安全危害的标秆机制 台湾德洲仪器公司现有员工两千余人,是一家高科技产品企业。总部设于美国德洲达拉期市,在全球16个国家中,共设有42家工厂,雇用了55,000名员工,1996年全球营业额达99亿美元,是全球最大半导体厂商之一。 在拥有如些庞大产能的高科技工厂里,如何做到零灾害的工业安全措施,都是企业领导视为首在任务,其总经理经常提到「安全健康环保方面的卓越绩效与领导地位,乃是德洲仪器员工的核心价值,这些价值均整合到本公司的生产过程及产品和服务之中,也是德洲仪器维持竞争优势和建构最佳商誉形象的首要考量因素」。这句话清楚地揭于了安全卫生的管理与执行,已然结合本公司的生产活动及员工的日常生活之中。在近日多起重大损失的工业安全事故中更显现了「结合生产活动,落实安全管理」之重要价值。 建构严密而周延的工业安全体系 台湾德洲仪器自96年以来,为了改善经营体质,进行多项安全卫生管理体系的改革,期间经历许多协调,然而其成果是丰硕的。
 首先从其公司的工业安全管理组织谈起,自96年总裁葛杰仁签署了「安全及环保哲学」宣言后,更树立了公司尊重生命与爱惜土地的典范。因此在生产和提供顾客所需产品及服务的同时,其安全及环境保护一定要做到符合下列相关的基准要求: 没有一件事比安全来得更重要; 员工的安全是主管的责任; 自我检查必须不断的实施; 所有的危险都可以防护,所有的伤害都可以避免; 遵守工作安全守则,是每位员工自身必须注意的职责; 厂外安全与厂内是同等重要的。 藉由上述基本理念的宣示及励行体现,从而建立以高阶主管组成的管理暨执行体系。其意义不仅在于只博取高层之重视而已,更势将安全管理的力量上下贯彻并横向连结,在固定召开的高阶安全卫生环保会议中,各责任单位的主管报告各类改善方案进度、新法令规定之实施成效、意外事故之研讨及部门协商仲裁等。让安全管理成为各部门必须要加以落实的工作重点,同时经由一再的检讨改进中,逐步地达到所翼求的尽善地步。在整个工业安全组织体系中建构了三个群,包括技术支援群、顾问群及执行群。各群的任务分述如下: 1. 技术支援群 在台湾德洲仪器公司所建构的技术支援群体系里,由各专业生产、工程、设备主管及工程师分工组成各策略工作小组,并依年度目标来进行规划执行方案及相关技术之支援。技术支援包含了设备安全、训练沟通、减废、事故调查考核、稽核、防火管理、交通安全推广、健康关怀等。这是安全卫生环保改善之主轴,各专业工程、主管、人员依支援百分之百生产力及策略,分别订定可量测之评核目标,经供管理阶层定位及进展。如减废小组订定资源废弃物回收再利用80%;事故调查考核、稽核、交通安全推广组订定降低伤害风险以提升生产力35%。这些技术支援群组各自发挥专业分工的支援领导,为整个工业安全体系构筑了严密而强有力的技术支援网。 2. 顾问群 由原安全卫生环保工程师组及厂内医师所组成的顾问群,负责提供专业谘询、资讯服务、协助目标管理以及量化成果,更兼负内外部沟通之桥梁。此举可避免陷入传统安全卫生环保保持中所出现球员兼裁判的泥淖中,而传统的安全卫生环保人员在那种双重角色中,无法提升自我视界和进行整体性规划与管理,而精力耗损于单一点上,德洲仪器工业安全顾问群的成设,让员工对可能产生的工业安全事件的危害,都能经由顾问群的咨询而得以采取更好的事先防范措施。 3. 执行群 由各生产、厂务、财务、品保等处主管组成执行群,其整合技术支援所规划之方案及将顾问群予以指导方向和执行策略方案推广至全公司。任何细密周延之计划及策略若无各单位管理阶层以责任自许来进行自我诊断、自我实践的话,其效果仅止于浮面。执行群的精髓即在于应用于已规划好之工程计划,自忖最佳化的进行方式,由各单位主管负责跟催及度量,让各项的工业安全活动都能彻底的落实到所有的生产制程中。 将工业安全观念融入日常生活中 将安全卫生观念融入日常生活之中是最为重要的课题。我们已摆脱传统之安全卫生教导方式,进行员工的生活及专业安全教育:在专业上因材施教,依所属制程的不同属性分别实施了化学品安全、设备安全、镭射安全…等课程。在管理方面提供经理级杜邦安全管理、安全稽核、人机工程、承揽管理…等。在生活方面则提供保健讲座、交通安全、旅游住宿安全…等。在灾害防止方面提供全员避难演练、紧急应变小组救灾技术、心肺复术及伤患安全运输演练…等。授课方式采用活泼化、互动式之成人教育形态,让学员藉由实际的参与而有更佳的学习成效。由于上级对这些课程的重视及鼓励,也引燃了学员们对于工业安全课程的高度兴趣,让所学的一切都能将每次可能造成工业安全危害的事件成功地化解于无形。
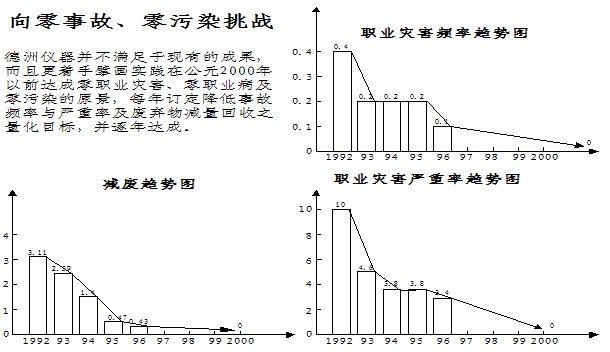 工业安全事件的及时处理与预防 我们都知道工厂发生严重的意外事故,绝非只是偶发事件,往往都是冰山一角,存在于水面下还有巨大的潜在危害,更是我们有兴趣去研究防止的。在德洲公司任何意外事故(含虚惊),不论有封锁伤害或是损失。事故主管皆于二十四小时内填写事故初步报告,其内容包含事故描述及后续处理方法,安全工程师立即将此事故报告总经理及相关高阶主管。为落实主动提案自我完善之政策,事故主管被赋予为此事故调查召集人之职责,相关之制程的设备主管、人事代表、医师、安全工程师及事故调查委员会皆为主要成员。事故主管备妥相关图说,分析基本原因及改善对策,并由成员共同质询,彼此互相脑力激荡出最佳改善方案经完成事故调查的改善报告。总经理亲自参与事故防止之讨论,并评核预防策略的绩效。由于在这方面的诸多努力,其成效也可以用数字来表明,自1996年以来其公伤事故频率降低7%;损失严重率降低98.5%;相关改善方案超过540件。
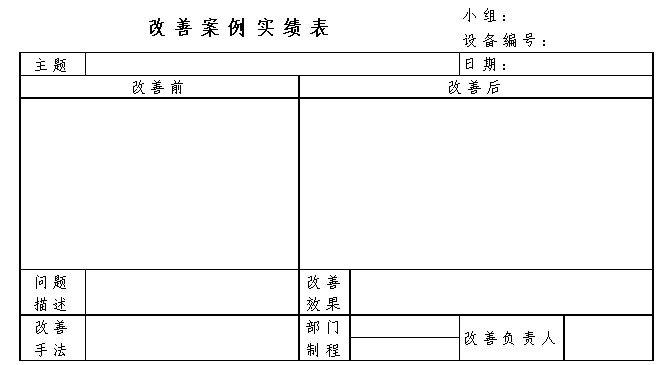 在台湾德洲仪器所有的工业安全活动都必须如制程紧密结合,因为无法灵活结合生产过程的安全活动,便不能显现其最大之价值。德洲公司经历了零灾害之推广,由负责维修之基层人员进行自我提醒、自我协调之安全作业,进而向零事故、零职业疾病挑战,将其终极目标极大化、明确化;至今更整合了所有资源以支援百分之百的生产力为安全策略,将安全与生活结合,将安全与产值之依存关系挑明。其在同时顾及生命尊严、道义考量外,更以量化数据告诉管理阶层既同仁,因安全活动所降低之损失及风险,皆可换算等量成本,换言之,也就是帮老总及公司同仁创造了多少利润。96年与95年相比之下,光是事故的降低就替公司赚进了22.3亿美元。别小看这些数字,如果因人为流失的工业安全措施而造成人员重大的伤亡或损及公司的商业信誉时,则不是用金钱可以衡量的。 安全生产、追求零的目标 以人为本,落实安全生产于生活之中是德洲仪器公司推行安全活动之主要精神。平时结合5S、TPM及提案活动来归纳建言和调整方向,每年均筹办安全卫生宣导周,配合策略目标重点推出一系列精彩活动,如96年该公司的主要目标为降低因交通事故产生之工时损失,其成果可谓十分卓著,自95年的1048天降为 96年的469天。他们的主题为「爱惜生命,关怀交通」,包含海报竞赛、漫画、提案及结合社区学童安全专题演讲等,让主题诉求的观念透过活动的延续伸展而深入人心。同时活动优良人员皆由部门经理奖励。台湾德洲仪器更以企业公民自居,做好零灾害工业安全及热心环保活动,曾多次荣获国内外政府相关单位颁发的劳工安全卫生优良奖项,近几年包括:
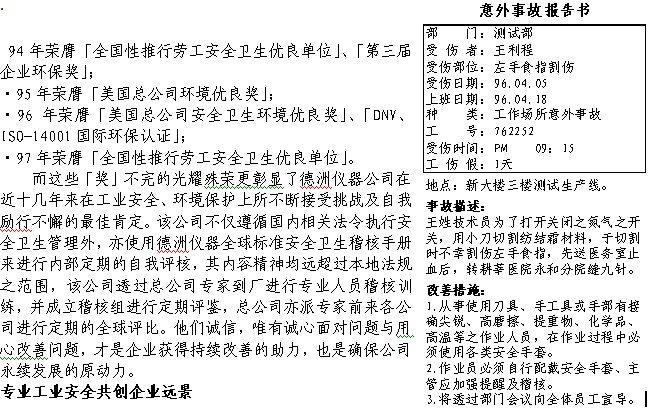 在追求零灾害工业安全的努力过程中,德洲仪器公司秉弃传统安全卫生一味经规定、要求、处罚为手段之管理方式,而以强调专业优质服务及善尽社会责任为指导方向;以自然生活化的方式,结合了第一线的员工共同来规划年度活动;着重经验分享的成人教育,与生产结合降低风险的安全规则,融合各阶专业人士之稽核检点;以听取员工需求兼顾企业稳定发展的安全策略,达成劳资双方共存共荣的目标。企业的远景如果不是建筑在「安全健康」的基石上,则往往会在一夕之间化为乌有。
|