摘 要
TPM是全员生产保全(Total Productive Maintenance)的英文缩写,TPM是一种渐进式的的管理体制,它继承了美国的生产性维修(Productive Maintenance),又吸取英国“设备综合工程学”的思想,又借鉴中国“鞍钢宪法”中工人参加管理的方法等基础上形成的。在20世纪60年代后期,日本汽车电子元件制造商——日本电装(Nippon Denso)最早将TPM技术引入生产领域。经历了二战惨败后的日本,在短短几十年间跃为经济强国;同样是隔海之邦的韩国,60年代经济完全不如朝鲜,如今不但远远超过了朝鲜,还成为各国学习的典范。其原因不仅仅是科学技术的应用,实践证明有效的管理方法和制度对公司的发展更为重要。近年来,福特、柯达、飞利浦等西方大公司纷纷推行TPM,推行TPM正逐渐成为生产型企业的潮流。 在TPM“东风西渐”的过程中,随着技术和管理领域的不断发展,TPM与TQM、ISO9000/14000、JIT、ERP等现代管理模式不断地融合发展。TPM从开始生产部门单纯的自主保全活动,逐步扩展到规划、采购、生产、设备、安全、销售等各个方面,已经逐步形成了由 “自主保全”、“计划保全”、“品质保全”、“个别改善”、“MP体系确立”、“事务改善”、“教育训练”、“安全环境”等八大支柱。各支柱都有一套完整的推行方法,对企业进行全方位的改善。在实际推进中,依企业具体情况,一般选取其中一个或几个支柱推进。 TPM是以设备的维护管理为切入点,通过所有员工积极参与的自主保全活动与不断改善的过程,为企业构筑防患于未然的机制,它对降低生产成本,提高生产效率,改善企业经营管理,增强企业竞争力起着重要作用。TPM改变了维修无法盈利的传统观念,追求生产系统效率最大化,以实现设备缺陷为零、故障为零、事故为零为管理目标。 中国石油化工股份有限公司天津分公司是我国特大型石油化工联合企业,是我国为数不多的年原油加工能力超千万吨的石化企业之一。天津分公司拥有炼油、乙烯、热电等10余套生产及配套装置和科研、信息、经销、消防等4个直属单位,生产规模、产品产量、质量、市场占有率都有相当的竞争实力,在中国的石油加工行业中处于领先地位。但随着我国正式加入世界贸易组织,关税的减让及石油市场开放的承诺,加速了我国炼油业和石油市场国际化的进程,同时也加剧了竞争的剧烈程度。政府保护的壁垒正在逐步消失。天津分公司面临着越来越激烈的市场竞争。天津分公司与国外石化大公司相比,无论是在生产成本控制、产品质量控制,还是在企业管理、资源利用等方面都存在着一定差距。要想在日趋激烈的市场竞争中求生存、求发展,只有采用先进的管理模式,提高企业核心竞争力,才能适应快速变化的竞争形势的要求。经过积极的准备,天津分公司成为中国石化股份有限公司第一个推行TPM单位。 结合TPM的基础理论和其发展过程,以及国内外一些成功推进TPM活动企业的经验,分析了天津石化公司管理中存在的问题。公司聘请了专业从事TPM咨询的韩国TMI管理咨询公司指导天津石化公司的TPM推行工作。在TPM的准备阶段,咨询公司TMI对天津石化各生产装置的生产情况、设备的维护保运体系和现场设备的管理情况、备件材料的管理情况等进行了诊断。通过诊断分析掌握了现场的管理水平,有针对性的提出公司TPM活动主要改善的领域和改善的目标。同时公司专门成立了以公司经理为组长的推进领导小组及TPM推进办公室, 在深入分析现有TPM活动体系的基础上,制定了天津石化公司TPM活动的推进计划、推进方针和目标。 在TPM的导入阶段,我们采用了“试点先行,先进带后进”的指导思想,在公司设立了9个试点小组,率先对TPM活动体系的基础活动进行了导入,在推进TPM活动的过程中,首先要使企业内形成良好的改善氛围,创建利于革新创造的企业文化,设法促进员工广泛积极的参与是顺利推进TPM的前提条件。促进员工积极参与的最有效办法就是开展小组活动和5S活动,通过5S和提案改善活动逐步引导员工寻找设备和生产现场缺陷,使员工经常思考如何去解决这些问题,通过与生产现场的持续改善和合理化建议活动融为一体,配以持续不断的培训和教育,使员工的综合素养进一步提高,为自主保全活动的推进创造条件。 在TPM推进过程中,确定了从自主保全、个别改善、事物效率、安全环保、事务改善、教育培训等几个方面的逐步推进,按照5S活动为基础,改善提案活动作促进,自主保全活动成规范,不断改善是核心的思路推进TPM活动。在TPM活动体系建立的研究中,深入分析了推动TPM活动的必要性和困难,确立了既切合实际又行之有效的活动体系。在活动推进实施的研究中,我们认识到如果孤立地去推行TPM,那么TPM只能是附加的工作任务,甚至会造成与现有管理的冲突。推行TPM就必须将TPM与公司其它的管理体系有机融合,建立起自己的体系。天津石化从80年代以来一直推行由政府部门倡导的TQM,2000年通过ISO9000认证,2002年通过ISO14000认证,2002年推行HSE管理体系, 2003年导入TPM。2005年3月在全公司内启动了ERP(企业资源计划)。天津石化在推行TPM的同时,从全系统的观点构建企业管理模式,整合了HSE管理制度,对ISO9000内控文件进行了修正,将TPM方面的规范化文件整合为ISO贯标的C级、D级文件。 在推行过程中,我们发现TPM的三大指标对于化工企业不太适合,由于化工生产过程均在密闭容器进行,属于连续化生产,一般的设备都有备用设备,OEE缺乏系统性,对于有备台的设备片面追求MTTR和MTBF缺乏经济性,造成保全活动中,为了追求维修速度产生了“以换代修”、“集装配件”等现象,导致维修费用大幅提高。针对这些问题我们提出了基于 TOC理论的 IEE 应用模型,将定性与定量相结合,有效地弥补了OEE的不足。 企业文化对TPM的影响也不容忽视。由于任何一种企业管理理论和管理模式都是特定的社会、经济、文化、历史传统等诸多因素共同作用的结果。中国和日本、韩国等国的国情不同,这是不争的事实 ,TPM的本土化已成为TPM成功与否的关键,对于TPM的本土化方面我们作了一些尝试,取得了一些宝贵的经验。例如对于困扰大多数推行TPM企业的“全员”问题,我们通过实际分析认为,在天津石化这样的中国国企内完全依靠所有员工的自主参与很不现实,我们通过研究,采取了提倡和鼓励“全员”参与意识,但不完全寄托在员工的“自主”参与上,而是根据企业的设备状况、工人素质和技术水平,制定可以指导操作工人、维修人员及生产辅助人员“全员”参加作业规范,通过宣传、推广和培训,形成可执行的制度准则。在具体工作方式上不是从一开始就一味地追求“全员”的概念。 运用运营管理及相关的工商管理理论知识,在对天津石化公司进行详细调研的基础上,研究了天津石化公司TPM实施过程,对实施中遇到的问题的进行了深入分析和实际论证,并提出了相应的对策。解决了在国有企业推进TPM活动遇到的一些问题。作者希望此项研究能对今后天津石化公司的TPM推进工作有所启示和帮助,能对情况相类似的中国企业推进TPM有一定的借鉴意义。 第1章 绪论
1.1 引言
随着科学技术的进步,生产设备向大型化、精密化方向发展,复杂的设备维护起来相当困难,其本身的品质以及组合精度严重左右着生产中的产品,由于掌握设备的工人不熟悉设备性能而造成的误操作、延误处理等问题也屡见不鲜,现代生产企业的设备维护成本呈不断提高趋势。生产设备的高速正常运转是取得产品高质量和企业取得高经济效益的根本保障,而如何使设备处于高效运转状态,降低设备维修成本,是摆在企业面前的一个重要问题。 自从工业革命以来,对设备管理与维修方面的研究随着管理理论的发展不断深入。TPM的产生对设备管理乃至企业管理都具有深远的影响,它彻底改变了人们对于设备管理与维修的认识,它通过整合全体人员形成巨大的力量来实现企业体质的革新。TPM所追求的是整个生产系统的综合效率,它是排除一切灾害、不良、浪费的挑战极限的企业革新活动。 石化企业设备自动化程度高,具有高温高压、易燃易爆,操作连续性强等特点,随着石化工业的飞速发展,近年来中国石化对于先进的工艺和设备引进越来越多,而在多年的生产实践中,我们发现单纯依靠引进新技术、新设备往往达不到预期的效果,建立与新技术、新设备相适应的管理模式同样重要。
1.2 本文选题意义
日本于1961年导入GE公司为代表的美式PM生产保全,以此为母体开始探索日本式的PM活动,1968年开始确立全体生产和维护人员参与的PM活动,经过2年多在日本电装公司的实践探索,成功地创立了TPM,即全员生产保全(Total Productive Maintenance )。 TPM在日本至今已有三十多年的历史,通过长期的实践积累,已形成标准化的管理程序。有专门研究TPM活动的组织,编写了大量这方面的指导性著作,并不断将新的管理方法融入到TPM活动中。二十世纪八十年代开始,TPM作为一套有效的管理系统,得到了人们的广泛认同,世界上许多公司先后引进了TPM。在此期间TPM系统本身也在不断发展完善,从最初的设备维护管理,发展到安全、健康、环保、质量、产品开发、供应链、人事培训、办公室管理等各个领域,成为了一套综合性的企业管理系统。 TPM在日本取得了巨大成功,之后在世界各地得到广泛应用,1991年在日本东京举行了首届TPM世界大会,有23个国家700余人参加,瑞典VOLVO(沃尔沃)及新加坡的NACHI INDUSTRIES PTE.LTD.公司作为非日资企业,首次获得了日本TPM管理协会的TPM认证。 TPM在韩国三星、美国福特、P&G等世界各地企业导入并取得了令人震惊的效果。许许多多推进TPM活动成功企业都取得了巨大的效益。主要体现在以下两方面: 有形效益 (1) 设备利用率、生产效率有明显提高; (2) 维修成本、备品库存大幅度减少; (3) 设备故障及对环境污染基本达到0的程度; (4) 废品减少,产品质量提高,客户投诉减少; (5) 员工合理化提案成倍增加。 无形效益 (1) 自主维修引入之后,操作工会自主地关心设备,正确使用设备; (2) 实现了设备的零故障、零缺陷后,员工对自己的能力充满信心; (3) 员工工作环境得到充分改善,消除污染,改善社区环境; (4) 公司形象有大幅提升,同行业竞争力明显增强。 天津石化公司是中石化股份公司的分公司,属于典型的国有大型企业,和大多数企业一样,采用前苏联的计划维修模式,在实际生产中存在着设备维修不足和维修过剩的问题。另一方面,操作工只管操作,修理工只管修理的传统分工,很大程度上影响了设备基础保养和深入维护,已经不能满足企业持续发展的要求。面对这些机、电、仪一体化、高度自动化的复杂设备,如何进行管理,如何使这些先进装备更好地发挥作用,为增强企业的核心竞争力服务,是企业新形势下设备管理工作中急待解决的问题。为适应设备的技术进步以及市场竞争日益激烈的要求,天津石化公司推行了TPM,从系统工程角度出发,建立企业全员生产维护管理体系,对设备实行全员、全系统、全过程管理,把设备寿命周期成本最小作为追求目标,充分发挥设备的综合效能,建立适合本企业特点的设备现代管理体系,以实现企业生产经营目标,提升公司核心竞争力。 TPM涉及到企业的方方面面,每一个单科甚至步骤几乎都有专著问世,但由于各个国家、各个企业的具体情况各不相同,并不可能有可供我们直接使用的固定模式,我们必须根据自身实际,找到适合企业实际情况的TPM模式。如何在国有大型企业中,结合国际上先进管理理论,通过研究分析建立适合本企业的管理体系。这正是本文将 TPM作为研究课题的主要意义和根本出发点。
1.3 本文研究方法
TPM 的理论和实践起源于上个世纪70年代,在发达国家的企业,尤其是日本企业中已经有了大量的实践,也形成了一定的模式。近几年,TPM理论传入我国并迅速为企业界所认同,但是关于 TPM的理论研究和实践经验还处于比较、消化、吸收等初步探索的阶段,远没有形成对于企业而言具体可操作的针对性指导。我国大多数引进TPM的企业完全按照日本或韩国的TPM手册来推行TPM,TPM本土化的研究不足。我国石化企业改革正逐渐深入,但是针对大型化工生产领域,并结合企业内部现行的HSE、TQM、ISO9000、ERP等管理体系,如何有效推行TPM的研究尚处空白。本文希望通过对这一课题的研究,为我国大型石化企业推进TPM提供一定的理论和实务参考,同时更希望通过这一研究引发国内学术管理界对这一课题的高度重视和深入研究,以此达到抛砖引玉的目的。 基于上述研究角度,本文的研究方法是: ①理论研究与实证研究相结合。 本文对TPM推进理论部分仅作必要的论述,侧重于实际推行过程和方法的研究,本文不是TPM推进步骤指导手册,而是力求从管理角度对TPM的推进进行分析。 ②个案研究与比较研究相结合。 TPM推进是一项复杂但又非常具体的工作。仅仅通过理论的阐述和一般性的现象分析,得出的结论显然容易流于抽象,对于企业实践难以产生具有针对性的指导。为此,本文对天津石化TPM推进的具体过程进行了分析,并提出了一些可操作性的新方法。同时就IE研究方面对中国与美国及日本等国进行了比较研究,以期读者更深入地理解。 ③定量与定性相结合。 本文论证过程中,重视理论运用和定性研究的同时,也注重实际的量化研究,引用了大量的数据,通过定量分析停机次数、IEE、库存费用等指标,定性与定量相结合,使结论更具严谨性。
1.4 本文框架结构
从逻辑内容上看,本文主要分四个个部分:第一部分包括第一章和第二章,主要介绍TPM的产生历史、发展现状与应用;第二部分包括第三章,介绍了天津石化的现状,以及推进TPM的必要性;第三部分包括第四章和第五章,主要叙述了天津石化TPM推进的计划、基础活动和推进过程;第四部分包括第六章,重点对天津石化TPM推进中存在的问题进行分析,进而提出了解决方法,这是本文的主体部分。 第2章 TPM简介
TPM是全员生产保全(Total Productive Maintenance)的英文缩写,在1971年TPM由日本工业设备管理协会(Japan Institute Of Plant Maintenance,简称JIPM)提出并推行。TPM日文和海外华语地区表述为“全员生产保全”,早年曾被翻译过成汉语为“全面设备管理”,后多译为“全员生产维修”,在李葆文教授2000年所著的《全面生产维护-从理念到实践》一书中,又被译为“全面生产维护”。 这并不是简单的名称变化,它从一个侧面反映出国内理论界对近年来日益发展完善的TPM,认识上一步一步深入的过程。 TPM是以提高设备综合效率为目标,以全系统的预防维护为过程,全员参与为基础的设备保养和维修体制,即通过员工素质与设备效率的提高,使企业的体质得到根本改善。日本设备管理协会于1989年对TPM具体定义表述为: (1)以建立追求生产系统效率化的极限和改善企业体质为目标。 (2)以生产系统全体寿命周期为对象,追求零灾害、零不良、零故障,并将所有损失事先加以防范。 (3)从生产部门开始,扩展到开发、经营、管理等所有的部门。 (4)公司全员参加。 (5)利用重复小集团活动,达成零损失的目标。
2.1 TPM理论产生与发展
二战结束后,TQM在日本得到广泛推广,但当TQM要求将设备维修作为其中一项检验要素时,发现TQM本身似乎并不适合维修环境。这是由于在相当一段时间内,人们重视的是预防性维修(PM)措施,多数工厂也都采用PM,而且,通过采用PM技术制定维修计划以保持设备正常运转的技术业已成熟。然而在需要提高或改进设备状况时,这种技术时常导致对设备的过度保养。这样一来,要提高设备运转率必然会导致维修成本大幅增加。 TPM诞生之前,日本企业曾经历过以下维修阶段: 事后维修阶段:1957年之前,事后维修 BD(Break Down),即被动维修。 改良维修阶段:1957年一1960年,改良保全CM ( Corrective Maintenance ),强调设备能力、性能的改善。 预防维修阶段: 1960年一1963年,保全预防MP ( Maintenance Prevention ),强调设备的预防改善。 生产维修阶段: 1963年一1971年,生产保全PM ( Productive Maintenance ),强调经济性、生产性的提高和保全。 20世纪60年代至70年代,美国诞生了生产性维修(Productive Maintenance)体制,在此基础上,日本设备工程协会又吸取了英国“设备综合工程学”的思想,和中国鞍钢宪法中提出的“台台有人管、人人有专责”的工人群众参加管理的方法,于1971年正式提出TPM管理模式。TPM是在质量管理(TQM)、准时制生产(JIT)等现代企业管理基础上逐渐形成的,成为当代企业管理的重要组成部分。其演化过程如图2.1所示:
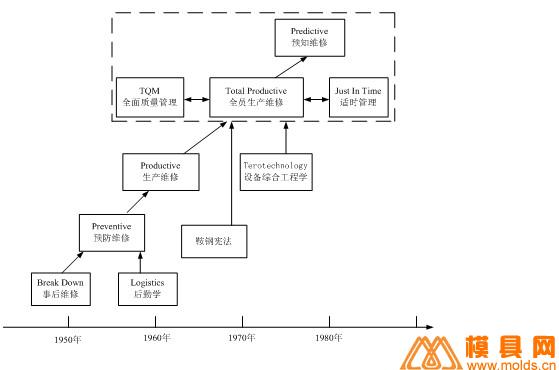 图2.1 TPM的历史进程
最早将TPM引入维修领域的是日本的一家汽车电子元件制造商——日本电装(Nippon Denso)在20世纪60年代后期实现。80年代起,韩国等亚洲国家、美洲国家、欧洲国家相继开始导入TPM活动。90年代,中国一些企业开始推进TPM活动。 TPM以生产部门的活动为中心,现在也如此,但为了追求企业经营的最高效率,单靠生产部门的活动当然是不够的。最近TPM逐渐扩大到生产部门以外的部门,成为从最高经营者到现场员工、事务员、技术者全员参与的活动。TPM的定义也从设备的框架扩展到整个生产系统乃至整个经营范畴,全面推进TPM成为企业改善经营活动的新课题。日本在推行TPM活动的进程中,不断充实活动的内容: 1971年,日本设立了PM奖,奖励那些在TPM活动中取得优异成果的企业。 1982年,第一本标准化(字典式)的TPM专著问世,即《TPM活动程序》,可以说,这是对日本企业界过去10年开展TPM活动的总结。 1989年,TPM活动的定义被修改,活动本身被注入了更多的内容。从这个时期起,TPM活动在日本得到较大范围的普及,并从日本逐步走向世界。 今天TPM活动还在继续发展之中,它作为企业降低生产成本,提高生产效率, 改善企业经营管理,强化企业竞争力的有效工具正在发挥着积极的作用。我国己经有一些企业开展TPM活动,并且取得了比较良好的效果。
2.2 TPM理论精要
企业的综合生产力是以投入和产出来衡量的。具体地讲,产出的产品越大于投入的3M(材料、人、设备),生产就越具有实际意义。TPM是人与设备、生产协调的产物。它通过对设备、业务的改善,促使人的思想发生理性变化,特别是促进员工形成自主意识,从而给企业带来更大的效益。
2.2.1 TPM基本理念 TPM管理模式是一种倡导企业完全“自我保健”体制的模式,已经逐渐被全世界所接受,成为了企业管理的重要概念,甚至被不少企业确认为一种主导的管理模式。其理念如下: ①提高企业经营素质 追求经济性,零灾害、零不良、零故障 ②预防哲学(防患于未然) MP(维修预防)、PM(预防维修)、CM(改善维修) ③全员参加(参与经营、人格尊重) 操作者的自主保全 ④现场现物主义 建立可视化管理,及干净的工作场所 ⑤智能化、无人化 建立智能化工作场所
2.2.2 TPM的三“全” TPM概括为三全,即全效率、全系统、全员参加。全员是基础,全系统是载体,全效率是目标,三个“全”之间的关系如图2.2所示:
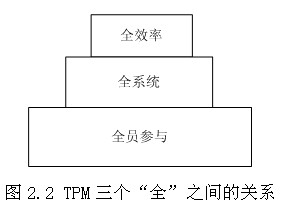 2.2.3 TPM的5S活动 所谓5S,是指对生产现场各生产要素不断进行整理、整顿、清洁、清扫和提高素养的活动。由于整理(Seiri)、整顿(Seiton)、清扫(Seiso)、清洁(Seiketsu)和素养(Shitsuke)这五个日语词对应的罗马拼音的第一个字母都是“S”,所以简称5S。5个S以素养为中心,前4个S均靠素养而形成。而其外部环境是良好的企业文化,如图2.3 所示:
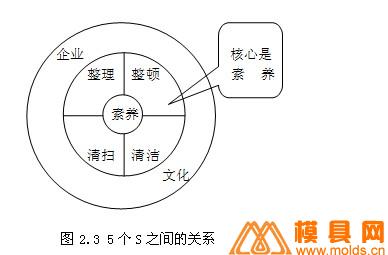
5S最早起源于日本,指的是在生产现场中对人员、机器、材料、方法等生产要素进行有效管理。5S是日式企业独特的一种管理办法。1956年,首部5S著作问世,从而对整个现场管理模式起到了巨大的冲击作用,并由此掀起5S热潮。日式企业将5S运动作为工作管理的基础,并辅以推行全面质量管理,使二战后日本产品质量得以迅猛提升,奠定了日本经济大国的地位。由于5S对塑造企业形象、降低成本、准时交货、安全生产、高度标准化、创造令人心怡的工作场所等方面的巨大改善作用。开展5S活动,是TPM的基础,推动5S可以营造一种整体的氛围,使组织或企业的每一个人都养成习惯并积极地参与,就能很容易地获得员工的支持与配合,也有利于调动员工的积极性来形成强大的推动力。 2.2.4 TPM活动体系 1980年设备综合效率指标问世,成为评价设备效率化的重要标准。这期间TPM也从开始的自主保全逐步发展到五大支柱(自主保全、个别改善、计划保全、教育训练、MP管理)。进入日本泡沫经济崩溃的1990年代,企业为了在营业额下降的同时保持盈利,“成本导向的TPM”在此时代就显得重要了,通过成本构造与损失结构的关联并加以明确化,能够反应成本降低的TPM就因此被提出和发展。1989年JIPM提出了TPM的新定义,把过去的五大支柱再加上三大支柱(品质保全、间接事务部门的效率化、安全卫生与环境)成为八大支柱,让内容更加扩大、更充实。按照TPM标准指导书,小组活动、提案活动和5S活动是八大支柱实施的基础,通过自主化的活动,建立标准化操作和管理规范,最终形成系统化的公司制度。由此构成的TPM活动体系如图2.4所示:
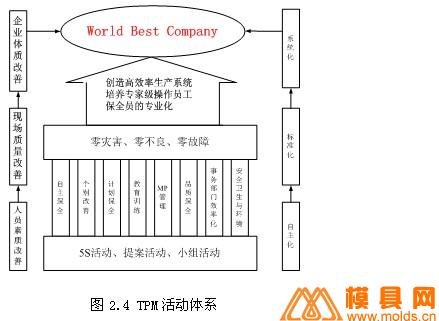 2.2.5 TPM的主要指标 TPM有大量的指标参数,核心指标为OEE(Overall Equipment Effectiveness)即设备综合效率,常用的维修考核指标主要是MTBF与MTTR。TPM以OEE来度量企业的管理水平,目前OEE已经成为了国际上评估企业管理水平的常用指标。 设备综合效率(OEE)=时间开动率×性能开动率×合格品率 其中:时间开动率=开动时间/负荷时间 负荷时间=工作时间-计划停机时间-非设备因素停机时间 开动时间=负荷时间-故障停机时间-初始化停机时间 性能开动率=净开动率×速度开动率 净开动率=(加工数量×实际加工周期)/开动时间 速度开动率=理论加工周期/实际加工周期 合格品率=合格品数量/加工数量 平均故障间距 (Mean Time Between Failure : MTBF),体现设备可信赖性的指标,表示设备故障处理完成到下次故障的间隔时间的平均值。 计算公式: MTBF=开动总时间/停止次数 平均修理时间 (Mean Time to Repair : MTTR)表示修理时间的平均值。是体现设备故障保全部门的对应能力的“保全性”指标,指从故障开始到处置结束所需的“每个故障的平均修理时间”。 计算公式: MTTR =故障总时间/故障次数
2.3 TPM的应用
由于TPM首先是在丰田公司的关联供应商日本电装开始的,因此TPM很快在丰田公司普及。继而在汽车产业、机械、半导体等加工组装产业迅速推广,80年代再普及到化学、食品、烟草、建筑、陶瓷、钢铁、医药品、造纸、印刷等行业。TPM具有广泛的适用性,如今几乎涵盖了所有行业,在各行各业均取得了良好效果。
2.3.1 TPM在国外的应用 经过30余年的发展与实践,TPM在日本工业领域的采用率已经超过了65%,日本知名大企业如:三菱重工、丰田汽车、雅马哈、川崎制铁、住友重工、富士、松下等均已经推行TPM。在意大利,20%的生产企业推行TPM;丹麦、瑞典等地区国家成立了TPM中心;英国有TPM协会;美国福特公司在全世界的300多个厂推行TPM;韩国三星把TPM作为主导管理模式。 欧美成功实施TPM的公司还有很多,其中包括许多世界驰名公司,如柯达公司、飞利浦公司、戴纳公司和艾雷•布雷德利公司等。这些公司有关TPM的报告都说明了公司实施TPM后,生产率有显著提高。尤其是柯达公司,它声称自公司采用TPM技术后,获得了500万比1600万的投入产出比。另一家制造公司则称其冲模更换时间从原来的几小时下降到了20分钟。这相当于无需购买就能使用两台甚至更多的、价值上百万美元的设备。德克萨斯州立大学声称通过研究发现,在某些领域采用TPM可以提高其生产率达80%左右。而且这些公司均声称通过TPM可以减少50%甚至更多的设备停机时间,降低备件存货量,提高按时交货率。在许多案例中它还可以大幅减少对外部采办部件、甚至整个生产线的需求。国外部分企业TPM推进成果如下: 北海道制油:劳动生产率提高58%、故障件数减少81% 理光(沼津):劳动生产率提高130%、生产周期缩短77%、开发周期缩短35%、市场投诉件数减少88% 大日本印刷•赤羽工厂:劳动生产率提高80% 车体工厂:劳动生产率提高90% 新日轻北陆事业所:劳动生产率提高120% 小野田:成本降低30%、故障件数减少98% VOLVO:劳动生产率提高30%、设备维护费减少50% 法国钢铁:设备效率提高50% 美国•雅玛哈:设备效率提高28%、工程内不良率减少80% 韩国现代汽车:设备效率提高25%、每台车制造工时减少28%、工程内不良率减少44% 韩国起亚特殊钢:设备效率提高50%。
2.3.2 TPM在中国的应用 通过长期的实践积累,TPM已形成一整套标准化的管理程序。有专门研究TPM活动的组织,编写了不少这方面的图书,并将很多新管理方法引入到TPM活动中。TPM在中国的推行也取得了很好的效果。 1979 年 9月 ,长春第一汽车制造厂召开了现场会和培训班 ,推广学习日本汽车制造公司的 TPM 管理体制。 中国企业管理协会在八十年代开始,向设备管理活动中导入PM及TPM。 莱芜钢铁集团有限公司(简称莱钢) 也在 1993年系统地推广 TPM管理。通过 10多年的实践 ,降低设备故障率 ,提高职工整体素质 ,使企业获得了巨大的经济效益。 1996年天津奥迪斯(OTIS)电梯有限公司推进TPM。 1997年深圳理光推进TPM,2年来全公司改善提案件数37354件,其中四个代表事例的改善效果如下: A生产线效率改善 效果:效率提高40%,人数减少70人。 B仓库动力叉车台数减少 效果:物流量30%上升,动力叉车台数反而从33台减至22台。 C制造部工程内不良损耗金额降低。 效果:1年内不良损耗金额减少96.6%. D品质不良预测活动 效果:新品种品质稳定时间从6个月缩短到2个月。 1997年, 秦皇岛戴卡轮毂制造有限公司开始推进TPM的活动,取得了很好的效果,生产和设备管理水平有很大的提高,数据如下: ①设备完好率由1997年的96%提高到1999年的98-99%。由1999年1月的98%提高到12月的99.55%。 ②设备可利用率从1999年1月的97.66%提高到12月的99.46。 ③从单件轮毂分摊备件成本费用来看,由1997年的6.97元/件降低到1999年的4.73元/件。以1997年年产量和单件分摊备件成本为基数,1999年产量增加75%,而单件分摊备件成本费用却降低32%。 从1997年至1999年在实行TPM前后,在设备基本没有扩充的情况下,企业各项指标的变化如下: ①质量综合成品率指标:1997年为81.1%, 1998年为86.5%, 1999年为88 .1%。 ②产销量指标:1999年为1997年的1.75倍,是1990年的22.51倍。 另外赛格-三星公司、上海宝钢集团、广东科龙集团、广东美的集团、济南将军集团、青岛海尔集团、山东荷泽卷烟厂等公司正在推行TPM。中国台湾的不少企业如康师傅、台塑等都在推行TPM。 除了在许多企业推广应用TPM以外,国人还致力于发展TPM理论,使其具有中国特色。例如:广州大学机电工程系李葆文教授根据调研提出“全员规范化生产维修(Total Normalized Productive Maintenance,简称TNPM)”方式;秦皇岛戴卡轮毂制造有限公司申涵清工程师根据企业实践提出“全员主动规范生产维修(ANTPM)”方式等。这些都为国内企业实施TPM提供了宝贵的经验,也促进了企业的发展。
第3章 天津石化设备管理现状分析
天津石化位于天津市大港区,东临渤海油田,南靠大港油田,占地面积1324万m2,处渤海之滨,扼京、冀、鲁之咽喉,环境优美,公路、铁路、水路、空中交通十分方便。天津石化公司1983年12月28日成立,隶属于中国石化集团公司。天津石化公司下设乙烯、化工、化纤、炼油等8个生产厂,物装、运销、电仪、工程等12家二级单位。固定资产总产值220.78亿元。生产装置分以下四个部分: 炼油部分: 原油加工能力1000万吨/年,对二甲苯生产能力8万吨/年,二甲酯生产能力13万吨/年,聚酯生产能力10万吨/年,聚脂切片生产能力3万吨/年。 乙烯部分: 有乙烯、聚乙烯、聚丙烯、乙二醇等生产装置。乙烯生产能力20万吨/年,聚乙烯生产能力12万吨/年,聚丙烯生产能力16万吨/年,环氧乙烷生产能力2.2万吨/年,乙二醇生产能力4.18万吨/年。 化工部分: 有大芳烃、PTA、聚丙烯、聚醚多元醇等装置,重整加工能力75万吨 /年,年产对二甲苯33万吨; PTA装置,生产能力25万吨/年;聚丙烯装置,生产能 力2.9万吨/年;聚醚多元醇装置,生产能力3.5万吨/年。 化纤部分: 有聚酯、涤纶短纤维、涤纶长丝、膜用切片、新品、废丝纺等生产装置,聚酯切片 生产能力3万吨/年,涤纶短纤生产能力16万吨/年,涤纶FDY、POY 长丝生产能力9万吨/年,DTY长丝生产能力6000吨/年,膜用切片生产能力8000吨/年,差别化涤纶短纤维生产能力2000吨/年。
3.1 天津石化公司设备管理体系
天津石化采取三级管理模式,即公司、厂、车间三级管理。车间主要负责现场设备的日常管理,包括设备的使用、日常维护保养等运行管理,并配合检修部门实施设备的大、中、小修工作,负责本车间设备技术档案的管理、以及按照分厂职能部门提出的要求统计上报有关信息;厂设备管理部门贯彻落实公司设备管理的规章制度,制定相应实施细则,建立全厂设备档案,负责组织设备技术状况分析,统计汇总全厂设备信息,落实考核工作;公司设备管理处负责制定公司设备管理的相关制度,在工作中加强监督考核;并负责提出公司全年设备管理的工作目标,下达各单位年修理费用指标,以及在设备的基础管理、专业管理方面,采取的具体措施,以保证各项指标的落实。设备管理系统组织机构设置如图3.1所示:
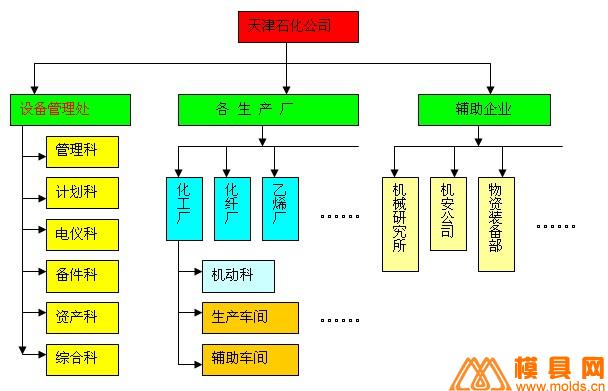 图3.1 天津石化公司管理机构设置图
公司设一名副经理主管设备管理工作,一名电气副总协助设备管理工作;各生产厂设一名设备厂长负责设备管理,并设有机动科负责设备的日常管理工作,机械研究所、机安公司负责生产系统的日常生产保运、维检修等任务,保运系统由设备部门负责协调、任务安排。物资采购、储存及领取由物资装备部统一管理。
3.2 天津石化公司设备管理现状分析
设备管理是企业管理的重要组成部分,设备管理业务可分为技术管理和经济管理两部分。现代企业设备管理的任务就是要保证为企业提供最优的技术装备,使企业的生产活动建立在最佳的物质基础上。设备管理强调运用系统的观点实行全过程的管理,把最大限度地控制影响设备运行效果的各个因素。通过综合分析,笔者认为天津石化公司设备管理存在以下几方面的问题: (1)管理机构设置存在问题 由于实行总厂、分厂、车间三级管理,行政色彩浓厚,业务上按照设备、电气、仪表、安全、操作、维修等专业分工管理,这种职责分工明确、等级分明的设备管理过程,指令信息传递速度慢、信息容易失真,难以充分发挥职工的主观能动性。 (2)设备管理与设备经济管理脱节 目前的设备管理工作主要以维持正常生产为主,而没有完全融入整个资产管理系统,设备全寿命周期费用只停留在认识上,工作中缺少系统性的经济分析,往往只关注修理费用、购置费用,而不关注运行费用,对全寿命周期的效益重视不够。将设备管理看作是技术服务保障工作,而不是一项直接影响企业经济效益的管理工作。 (3)缺乏完善的设备管理考核体系 目前,中石化炼化企业的设备管理考核仍沿用老的计划经济体制下的考核方法,往往只设置一些中间过程的考核指标,而缺少对设备管理人员、使用人员、维修人员的行为考核,存在考评制度不健全,绩效目标不明确,衡量标准没有量化等问题。 (4)缺少自主管理意识和全员设备管理观念 无法科学地保障生产设备经常处于可用状态。计划维修工作还带有一定的随意性和盲目性,不能预防由于随机因素而引起的偶发事故,故障停车得不到较好的控制;维修不足和过度维修的情况时常出现。
3.3 推进TPM活动的必要性
基于以上设备管理各方面的诸多问题,其根本原因就在于设备管理缺少一个具有明确指导思想的规范化、标准化、科学化的保证体系,所以我们在设备管理中引入TPM,通过改善人和设备的“素质”来充分发挥设备的效能,使技术管理和经济管理有机地结合,并逐步建立、完善设备管理保证体系。 由于TPM活动能带给企业巨大的有形效益和无形效益,在美国、欧洲许多国家及亚洲日本、韩国等许多大、中型企业及跨国公司都已经开展了TPM活动,不少企业还成立了“TPM俱乐部”,专门从事TPM活动的研究与推广工作。这些年来,天津石化公司已经成功推进TQC活动、通过了IS09000质量体系认证,为什么还要推行TPM活动呢?进一步分析可知: TQC活动主要是从发生的问题着手解决问题,侧重提高产品质量,而TPM活动是以从现场设备为切入点,预防或预知对策型的改善为主,持续提高管理水平。IS09000标准系列的导入本来可以与内部的业务改善进行有效结合,帮助企业不断提高质量管理水平。当然,能在IS09000质量体系认证之后,积极推进TPM活动,并将标准化活动与改善活动有机地整合,必将为企业带来很好的管理效益和经济效益。 所以,要真正推动企业内的生产变革,开展TPM活动是及其有必要的。推行TPM活动不仅在提高劳动生产率、减少停机率、减少次品和顾客投诉、减少员工及维修成本、节能、减少污染等有形效益方面有明显的影响,而且在无形效益方面如改善工作环境、在顾客中树立良好形象,治理环境等方面也具有良好的社会效益。
3.4 天津石化推进TPM的困难和优势
对企业来说,推进TPM是一个痛苦的历程,不是一蹴而就,一朝一夕就能成功的。这要靠全体员工一点一滴的工作积累。
3.4.1 天津石化公司在推进TPM活动中所面临的困难 (1)人员思想上的困难 许多生产厂的一线操作工没有进行过TPM知识的培训,对TPM活动认识不足,常常会问:“为什么我们非要做这些工作?保持如此干净的状态是困难的!这些工作原来一直是他们来做的”等等;而保运人员会感到“一旦生产人员开展了自主保全活动,他们的工作量就会减少,就会有人员精简的压力”。 (2)体制机制上的问题 原有管理模式中存在着设备的“用、管、修”脱节,各自为战,操作工普遍存在着“我使用、你维护”的观念,加上原来各单位的机、电、仪检修及运行人员并入机安公司,成立了新机安公司,已和天津石化不存在行政管理关系,只有经济关系,保运人员难免会出现支援的主动性不足等困难。
3.4.2 天津石化公司推进TPM的优势 (1)设备管理基础较好 公司成立20多年来,在设备管理方面积累了大量的先进经验,技术上有较严密的管理规范和检修作业规程。 (2)公司领导层的大力支持 公司领导对推进TPM活动有着强烈的愿望和决心,成立了以公司经理为组长的推进领导小组,把“全面推行TPM,改进生产和施工现场直接作业环节的管理”作为公司的一项重点任务。 (3)技术支持 为确保TPM活动的顺利进行,公司聘请了韩国TMI咨询公司为我们的TPM各项活动提供技术指导,负责公司TPM活动导入培训及现场咨询工作,指导建立天津石化TPM管理程序,完善TPM活动评价体系。
第4章 天津石化公司TPM活动导入
天津石化在2003年8月26日第21次公司经理办公会上,确定了在公司范围内重点推行TPM。明确了TPM的基本方针,即通过自主保全活动,造就有能力的现场职工队伍;建立设备寿命周期费用最经济的管理体制;实现设备综合效率最大化。同时提出了“提高员工素质,改善设备状况,创最具竞争力的一流石化企业”的活动目标。 为了更好地在公司内全面推行TPM管理工作,公司聘请了专业从事TPM咨询的韩国TMI管理咨询公司指导天津石化公司的TPM推行工作。公司专门成立了以公司经理为组长的推进领导小组及TPM推进办公室,制定了公司TPM工作的推进计划、推进方针和目标。各生产企业也根据本单位推进要求,成立了厂TPM推进委员会和推进办公室,专门确定了一名专职干事。 参照TPM规程要求,结合天津石化企业实际情况,并经咨询公司建议,天津石化TPM推进按表4-1所示的12个阶段来进行:
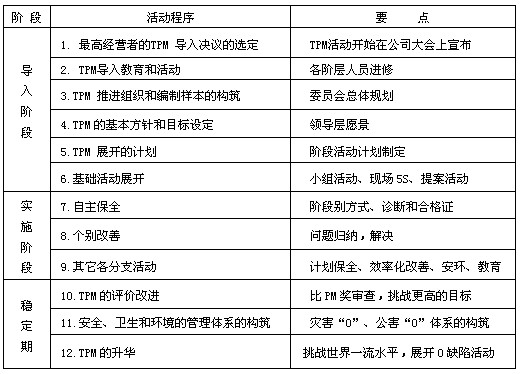
表4-1 天津石化TPM推进12个阶段
从2004年2月份开始,天津石化公司开始在全公司范围内正式启动TPM,选定化工、化纤、乙烯、热电等单位9个小组作为试点。 为了提高各单位TPM活动推进员及一般小组组长对TPM活动理念的理解,尽快掌握开展TPM活动的方法、程序,保证在全公司范围内有效、有序地推进TPM活动,公司TPM办公室与培训中心联合举办“TPM活动组长培训班”。随着TPM基础活动的展开,TPM的进入实质性导入阶段。
4.1 开展TPM小组活动
小组活动的开展标志着TPM活动进入了导入实施阶段。小组(也译为小集团)活动是TPM最活跃、最具特色的团队行为。TPM 小组活动是把企业的发展和每个员工素质的提高作为其目的。通过相互尊重、全员的参与来实现系统的综合性效率。具体来讲,彻底地排除影响设备效率的损失,把设备运行到最佳状态,从而来确保生产计划的完成以及质量的稳定。 天津石化是采用行政主导型小组来开展活动的。所谓行政主导型小组活动,并不是丢弃现有的行政架构而另起炉灶建立单独的组织,是与行政兼容或一体化的小组。TPM进行与编制一体化的小组活动,以厂长、车间主任、工段长、班长、一般员工等为成员的不同阶层的推进会或小组,各自承担不同任务进行小组活动。各阶层小组组织图如图4-1所示;
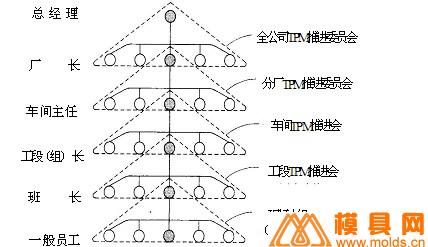
各阶层小组的作用分别如下: ①全公司TPM推进委员会的作用 全公司TPM推进委员会占重要的地位。在推进TPM过程中,要在大局上把握方向是否正确、推进方法是否合适等。 ②各分厂TPM推进委员会的作用 构成各分厂TPM推进委员会的成员是隶属个分厂的车间主任。根据公司的方针结合本厂实际积极贯彻设定的TPM基本方针和目标。 ③车间和工段等中间小组的作用 根据全公司TPM的基本方针,结合本部门实际设定本部门的方针,并把大的目标详细化,赋予现场小组具体的目标。 ④TPM小组(现场小组)的作用 现场小组是具体展开自主保全活动的部门,担负着指导他们小组内的成员自觉地参与自主保全活动的任务。一般来讲,TPM小组也专指这类现场小组。 各小组的命名,则由小组自己决定,以热电厂为例,详见表4.2,
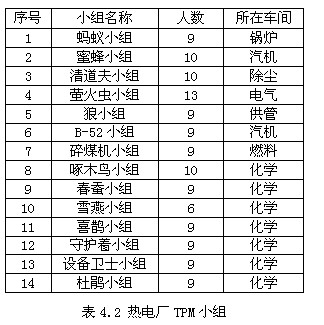 通过开展TPM小组活动,天津石化共建立TPM小组146个,共计1482人。详细数据如下: 化工厂共建立现场小组36个,共324人。 化纤厂共建立现场小组20个,共258人。 乙烯厂共建立现场小组39个,共510人。 热电厂共建立现场小组14个,共130人。 供排水厂共建立现场小组19个,共106人。 空分厂共建立现场小组9个,共77人。 运销部共建立现场小组9个,共77人。
4.2 开展5S活动
开展5S活动是TPM的基础,5S活动是日本企业普遍采用的一种现场管理方法,现在已在世界许多国家得到推广应用。5S具体指整理、整顿、清扫、清洁、素养。 5S是现场管理的基础,5S水平的高低代表着现场管理水平的高低,而现场管理的水平制约着ISO、TQM、TPM活动能否顺利地推动或推行。通过5S活动的开展,从现场管理着手,才能够起到事半功倍的效果。
4.2.1 5S活动具体内容 ①整理(Seiri) 整理是彻底把需要与不需要的人、事、物分开,再将不需要的人、事、物加以处理。其要点是对生产现场摆放和停滞的各种物品进行分类;其次,对于现场不需要的物品要坚决清理出现场。 整理的目的是:改善和增加作业面积,提高工作效率。消除管理上的混放、混料等差错事故;有利于减少库存,节约资金。 ②整顿(Seiton) 整顿是把需要的人、事、物加以定量和定位,对生产现场需要留下的物品进行科学合理地布置和摆放。简言之,整顿就是人和物放置方法的标准化。整顿的关键是要做到定位、定品、定量。对这项工作有专门的研究,又被称为定置管理。 ③清扫(Seiso) 清扫是把工作场所打扫干净,对出现异常的设备立刻进行修理,使之恢复正常。清扫过程是根据整理、整顿的结果,将不需要的部分清除掉,要自己清扫,而不要依赖他人,不增加专门的清扫工。 ④清洁(Seiketsu) 清洁是在整理、整顿、清扫之后,认真维护、保持完善和最佳状态。在产品的生产过程中,永远会伴随着没用的物品的产生,这就需要不断加以区分,随时将它清除,这就是清洁的目的。 清洁并不是单纯从字面上进行理解,它是对前三项活动的坚持和深入,从而消除产生安全事故的根源,创造一个良好的工作环境,使员工能愉快地工作。这对企业提高生产效率,改善整体的绩效有很大帮助。 ⑤素养(Shitsuke) 素养是指养成良好的工作习惯,遵守纪律,努力提高人员的素质,养成严格遵守规章制度的习惯和作风,营造团队精神。这是5S活动的核心。没有人员素质的提高,各项活动就不能顺利开展,也不能持续下去。 实施5S要始终着眼于提高人的素质,要贯彻自我管理的原则。创造良好的工作环境,不能指望别人来代为办理,而应当充分依靠现场人员来改善。5S的意义和期待效果如图4.2所示:
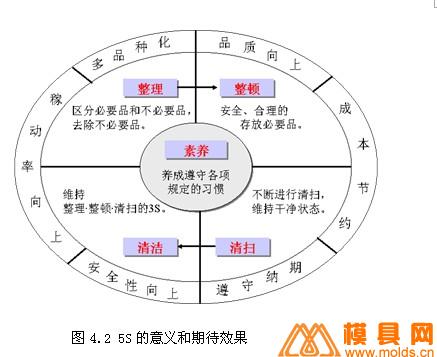 4.2.2 天津石化5S活动 由于5S自成体系,早在2003年3月天津石化公司就在全公司展开了5S活动。为了有效推进5S活动,公司成立了三个具体的实施小组,即宣传培训组、推行实施组、考核评价组,由公司相关处室及各厂相应部门的领导组成,实施小组在公司TPM管理领导小组的支持、指导下,开展宣传动员、培训教育、推行指导、综合考评等工作。 5S活动的实施,重在人员的意识改革,5S活动开展起来比较容易,可以搞得轰轰烈烈,并在短时间内取得明显的效果。但是要长期持续、不断优化却不很容易。不少企业都出现过“一紧、二松、三垮台、四重来”的现象。实践证明,认真、严格地做好检查、评比和考核工作,仅是使5S活动坚持下去并得到不断改进的必要条件。要最大限度地将5S活动的成果巩固下来,还要从制度上下功夫,天津石化公司通过标准化的措施,很好地解决了问题,主要措施如下: ① 红牌管理 在实际工作中,天津石化公司采用了 “红牌管理”方式,“红牌管理”贯穿于5S活动的整个实施过程中,对于预先发现和彻底解决工作场所的问题具有十分重要的意义。具体方法就是不断地找寻出所有需要进行改善的事物或过程,并用醒目的红色标牌来标识问题的所在,然后通过不断增加或减少红牌,从而达到发现问题和解决问题的目的。 ② 目视管理 目视化管理,是指用直观的方法揭示管理状况和作业方法,让全体员工能够用眼睛看出工作的进展状况是否正常,并迅速地做出判断和对策。如图4-1所示,上限与下限之间的区域是正常状态,员工很容易就能分辨出不正常的状况。
图4-3 目视管理的极限可视化 目视管理形象直观,容易识别,简单方便,传递信息快,提高了工作效率。目视化管理在生产现场的应用范围非常广,几乎可涵盖生产活动的各方面。在天津石化的目视化管理主要应用于以下几方面,详见表4.3:
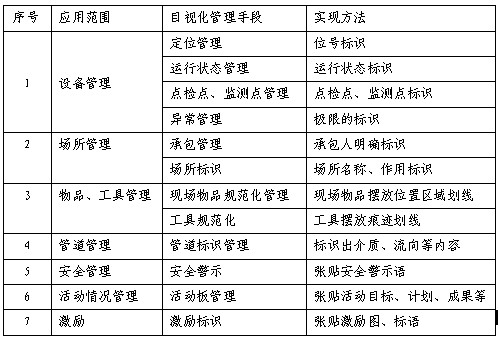 表4.3 目视管理内容
③完善5S活动的标准 检查、考评和奖惩等措施能够较好地推动5S活动的实施,但是要将5S活动长期维持下去,最好的方法是建立5S活动的标准。天津石化公司建立了详细的5S活动标准文件,其中包括现场标准、检查记录、缺陷整改反馈制度等,根据5S的活动标准,工作人员就能在5S活动中发现异常问题,采取措施加以改善,并运用标准化的方法将其固定,从而进一步巩固5S活动的实施成果。标准化可以消除人为因素带来的问题,从而为企业的产品带来稳定的品质,减少产品不良造成的损失。另外5S的标准也不是一成不变的,而是在工作中持续地得到改善,进而形成良性的循环4.3 开展改善提案活动
所谓提案改善活动,指的是公司通过一定的制度化的奖励措施,引导和鼓励员工积极主动地提出并实施任何有利于改善企业经营品质,提高企业管理水平的革新建议、改进意见和发明创造等的活动。并对提案的员工给予适当的奖励与表扬。任何行业的任何工作,不论是现场操作、文书或管理工作,都存在着许多浪费,例如时间、场所、士气的浪费等,这些都直接影响企业的效益。因此,必须对这些不合理的现象加以改善。早期的国有企业曾鼓励员工提出合理化建议,这就是提案改善的前身。但是,合理化建议和提案改善还是有一定区别的,前者不一定对每个建议都进行答复和实施,而后者对每一个建议都进行探讨、研究,并且对比较好的建议进行奖励。 在推进TPM活动的过程中,首先要使企业内形成良好的改善氛围,创建利于革新创造的企业文化,设法促进员工广泛积极的参与是达成这一目的的最好办法。促进员工积极参与的最有效办法就是开展改善提案活动。提案活动可以通过各种办法鼓励全员持续积极地参与TPM活动,促进所有员工关注身边的问题并提出改善提案。
4.3.1 天津石化开展提案改善活动原则 所有的改善和革新活动,要想真正取得效果,员工积极广泛的参与是十分重要的。否则,改善和革新的良好愿望将成为企业高层的一厢情愿。在日本出版的有关TPM改善活动的书籍里面,很少有对如何激活改善活动方法的叙述。原因在于日本企业里,员工爱公司如家,爱工作如命,只要公司号召,员工就能够积极响应并积极投身其中。因此,在日本开展这项活动并不费多少功夫。但在中国企业里,要让员工主动积极地提出改善建议,促成员工的广泛关注和参与,确实不是一件容易的事。但如果没有员工的广泛参与,TPM活动的全员参与就无法激活。 在天津石化我们尝试了开展提案改善活动的办法。制定了以下几个原则。 ① 不限定提案内容,原则上不拒绝任何提案 在这项活动中,不限定员工的提案范围,员工可以从企业经营活动的所有方面提出改善建议。提案内容可以涉及质量、效率、成本、安全、卫生、环境、教育等所有方面 同时也不限定提案水平的高度和提案的大小。对于很多没有价值的提案,也必须回复提案者,说明不受理的理由,不能对提案人进行批评和处罚,相反要鼓励提案人继续提出意见。 ②耐心对员工进行指导,提高提案水平 ③提案活动不以经济效益为追求目标 提案活动最重要的目的是促进员工对活动的关注和参与,营造良好的改善活动的氛围,因此要摈弃或排除任何怀疑提案活动经济效益的意见和想法。
4.3.2 天津石化提案改善活动标准化 改善提案活动是一种通过标准化、制度化的评价、奖励措施来推动的改善活动。因此,开展这项活动最根本的办法就是建立一套提案等级评价标准以及与之相对应的奖励制度。为此在工作中我们对以下方面进行了标准化: ①提案格式的标准化 为了促进员工的广泛参与,使用标准化的提案表格特别重要。标准化的提案格式不仅便于员工填写,最重要的是要使提案有良好的可操作性,我们将提案书格式进行了标准化,表4.4是对所有内容适用的简易型提案书格式。
单位名称 |
|
所在部门 |
|
提案人姓名 |
|
提案时间 |
|
提案名: |
主要改善 |
|
|
实施提案所需条件
(人员、资金、材料、工具) |
|
实施此提案所需时间周期 |
|
此提案预计产生效益 |
|
建议提案实施者 |
□ 本人 □ 本部门项目小组 □ 厂项目小组 |
部门负责人意见 |
|
厂TPM推进委员会评审意见 |
|
公司TPM推进委员会评审意见 |
|
答复提案
人的时间 |
|
提案人确认 |
|
备 注 |
| 表4.4天津石化员工提案申请表 ②提案等级评定办法标准化 通过对提案分等级,达到提高提案质量的目的。一般来说,提案的得分是根据多个项目的评分来决定的。审核评分标准详见表4.5:
评价项目 |
评 价 基 准 |
等级分 |
备注 |
有形 |
5百万以上 |
30 |
以年为单位的预计金额 |
效果 |
3百万~不足5百万(以50万为单位得1分) |
26~29 |
(30分) |
1.5百万~不足3百万(以30万为单位得1分) |
21~25 |
|
50万~不足1.5百万(以10万为单位得1分) |
11~20 |
|
30万~不足50万(以4万为单位得1分) |
6~10 |
|
不足30万(以6万为单位得1分) |
1~5 |
无形 |
安全性、劳动强度、环境或对外形象改善效果明显 |
8~10 |
|
效果 |
以上任意项改善效果一般 |
3~7 |
(10分) |
以上任意项可以看出有改善 |
1~2 |
波及 |
可以在整个中国石化使用 |
11~15 |
|
效果 |
可以在天津石化内推广使用 |
7~10 |
(15分) |
适用于本厂/部(支援、制造) |
4~6 |
|
只适用于本车间/岗位 |
1~3 |
独创性 |
队员全体提案 |
12~15 |
|
(15分) |
独自性的IDEA |
8~11 |
|
计划性的改善(对策) |
4~7 |
|
单纯模仿改善 |
3 |
|
一般业务 |
1 |
活动评价 |
活动难度极高 |
5~10 |
|
(30分) |
活动难度一般 |
1~5 |
|
付出了极大的努力 |
3~5 |
|
|
一般性努力 |
1~2 |
|
改善效果长期有效 |
3~5 |
|
|
改善效果短期有效 |
1~2 |
|
自己实施 |
6~10 |
|
|
其它部门实施 |
1~5 |
合计 |
100分 | ③奖励办法、奖励金额标准化 对改善提案的提案人实施奖励(物质和精神)是激发这项获得的最根本措施。为此天津石化公司建立了一套有效的和可操作很强的奖励制度和提案审查标准。提案审核标准是用来核准员工提案的有效性和效果的。奖励制度就是通过制度化的奖励措施对员工的提案进行精神和物质的奖励,激发员工特别是一线员工参与提案活动的积极性。对各个级别的提案发放多少奖励金如表4.6所示:
等 级 |
等级分 |
奖励金额 |
备注 |
1等 |
96以上 |
¥1,500.00 |
等级分由各部门经理及评审委员会根据提案等级审核 |
2等 |
95~93 |
¥1,000.00 |
3等 |
92~90 |
¥500.00 |
4等 |
89~85 |
¥300.00 |
5等 |
84~80 |
¥200.00 |
6等 |
79~75 |
¥100.00 |
7等 |
74~70 |
¥50.00 |
8等 |
69~65 |
¥30.00 |
9等 |
64~60 |
¥20.00 |
10等 |
59~50 |
¥10.00 |
| 表4.6提案级别和奖励标准
④提案受理、处理流程标准化 有效收集员工提案并及时评级,奖励提案员工是激活改善提案活动的前提条件。为了持续推进这项活动,还需要对提案受理、处理流程进行标准化,改善提案流程,天津石化公司对提案受理、处理流程进行了优化,其工作流程如图4.5所示:
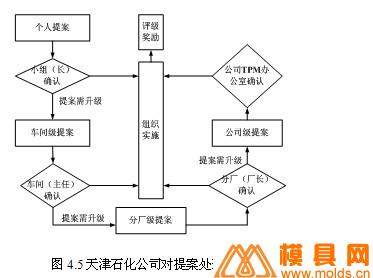 4.3.3 天津石化提案改善活动分析和改进 天津石化提案改善活动自2004年9月开始,到2005年5月改善提案数量如表4.7所示:
日 期 |
2004.9 |
2004.10 |
2004.11 |
2004.12 |
2005.1 |
2005.2 |
2005.3 |
2005.4 |
2005.5 |
改善提案数量(件) |
950 |
1553 |
1250 |
4460 |
1430 |
850 |
1468 |
1355 |
1590 | 表4.7 改善提案数量
从以上数据可以分析可看出,提案活动经历了刚开始启动、逐步升温、到年底的提案高潮、年后大幅度回落。为什么会这样呢?要解决这个问题,还要从人的行为特点进行分析。行为学研究发现,一个人或一个集体在面对一个新事物的时候,都会经历三个阶段,改善活动的推进过程也不例外。 ①第一个阶段是抗拒期,在此阶段,多数人不能很好地接受改善活动,只有少数人在强力推动下,才勉强提出一些提案。 ②第二个阶段是降服期,当推动力足够强大并持续一定的时间之后,多数人在被动中接受了这样一个事实,放弃抗拒,根据要求或随多数人一起提出改善提案。 ③第三个阶段是就是我们要追求的主动活动期,在这个阶段,员工已经能从改善提案活动中体会到充分的成就感和乐趣等等,他们能在没有任何外力要求的情况下主动参与活动。 了解了人的行为模式后,我们就能够理解为什么提案活动会经常出现反复了。活动开始时抓得紧,人均提案件数逐步增长,到年底提案奖励要兑现时提案空前增多,到了降服期,但年后员工对奖励兑现怀疑性增加,活动推动力不足,加上通过前期大量提案把显而易见的问题都解决了,很难找出问题,提案件数将立刻降下来。这是个很典型的问题困扰着许多活动的推进者,又如何面对这种局面呢?我们通过具体分析后采取了以下措施: ①提案奖励兑现形式 提案奖励资金一定到位,并将每年年底奖励改为每月兑现,奖金的支付方式改为现金支付,实践证明现金支付要比把奖金计入工资更能发挥作用。除了物质奖励之外,同时辅以精神鼓励,如月度、季度、年度冠军 奖状、锦旗、优胜者展示等形式。 ②引导员工制作高水平提案 培养员工强烈的问题意识,倡导把习惯当问题看的思维。通过定期交流,评比、辅导等多种活动,提高员工提案的水平。 新措施采用后,提案质量明显提高。长期坚持开展改善提案活动,塑造了积极向上的企业文化,为下一步成功实施TPM奠定了很好的基础。
第5章 天津石化TPM实施过程
根据日本和韩国企业TPM的实施经验,推广TPM比推广5S和提案活动的难度更大,一般都会遇到较多的障碍。产生这种情况的主要原因是TPM的推广过程中活动太多,涉及面过广, TPM的推广活动体系相当复杂,会使员工感觉过于繁琐,心里产生抵触情绪。而且推广时间过长,容易产生持续推动力不足,造成半途而废。此外员工对于TPM不了解也是TPM推行困难的原因之一,对于大部分普通员工来说,他们并不清楚TPM实施后会给自身带来何种利益,对TPM的重要性认识不足。为此我们结合天津石化特点,将TPM的八大支柱中四个主要部分单独来执行,这四个主要部分分别为:自主保全、计划保全、个别改善、事务部门效率化活动。另外培训和安全环保两大支柱内容融入公司原来的管理体系中,将原来的教育培训作为全过程的手段,与公司原有的教育培训工作整合,安全环保活动与公司实行的HSE体系相整合,将TPM的要求项目写入HSE文件中。由于我公司TQM体系推进效果较好,故TPM的品质保全支柱我们不再开展。MP支柱活动与我公司的设备在线监控系统S8000相类似,故也没有开展。 TPM各个支柱的都是通过各自的小组活动来推进实现的,各小组的进度,进行内容都是不同的,所以我们对各阶段的活动结合具体的小组事例进行了简要的介绍。
5.1 自主保全
自主保全是指企业员工自主地对企业实施全面的管理、维护和保全。自主保全是TPM实施的重要一环,通过自主保全活动,不但能提升员工的维修保全技能,还能培养了他们责任心和自豪感。自主保全的关键之处在于真正做到“自主”,使现场设备的保全、维护成为操作人员的自觉行为,使之成为工作人员一种良好的工作习惯和内在素质。 自主保全活动的理论基础是“故障是冰山的顶峰”,如图5. 1显示出故障冰山的潜伏问题,即设备故障只是设备劣化的冰山露出水面的部分,而在故障发生之前,一些潜在的隐患己深藏在设备之中。所以说故障只是冰山的顶峰。
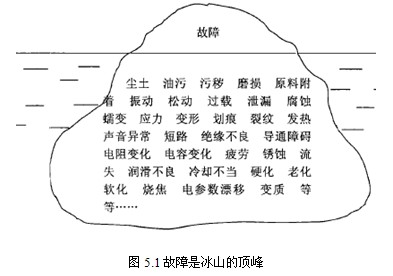 从图中我们可以看出,消灭和减少隐患可以减少故障发生,改善设备运行环境可以防患于未然。而自主保全活动就是消灭和减少这些隐患的简单可行办法。由于操作者与自己所使用的设备朝夕相伴,对设备性能及运行状况的了解、故障的早期发现、维护工作的及时进行等方面可以发挥其他人员不可替代的作用。同时,开展自主保全活动有利于提高操作者对设备使用的责任感。因此,开展自主保全活动对提高现场管理水平的重要意义是不言而喻的。 自主保全活动是以生产现场操作人员为主,将操作者的积极性调动起来,通过不断的培训和学习,使现场操作人员逐渐熟悉设备构造和性能,不但会正确操作,而且会诊断和处理故障。在操作中逐步确立作业人“自己设备自己维护”的观念。活动开展的目的是通过操作者的广泛参与,追求设备的“0”故障,达到设备的极限效率。目前,按照天津石化公司的原来的岗位责任制,操作工只负责使用设备,设备的维护工作由设备技术人员来完成。为此我们按照自主保全的要求完善了公司管理制度。 天津石化生产现场的自主保全是以生产现场操作人员为主,按照人的感觉(听、触、嗅、视、味)对于设备进行检查,并对加油、紧固等维修技能加以训练,使员工有能力对小故障进行修理。通过不断的培训和学习,使现场操作人员逐渐熟悉设备构造和性能,不但会正确操作、保养和诊断故障,而且会处理小故障。自主保全是深化推行TPM的一个重要部分,自主保全活动的展开,需要稳扎稳打、有条不紊地进行。经过咨询公司的诊断和建议,天津石化公司TPM实施自主保全按照TPM手册要求分为七个步骤实施,如表5.1所示。
步骤 |
阶段名称 |
工作要点 |
预期效果 |
1 |
设备初期清扫 |
通过清扫发掘6大不合理及复原改善 设备基本条件(润滑, 注油, 油量表, 连接状态 等)整备 |
消耗品费节减 作业环境改善 |
2 |
发生源/困难部位对策 |
清扫困难地点及不合理的根本改善 污染发生源的去除 |
去除设备的污染 D/T 减少 pit 不良的减少 |
3 |
基准的制定 |
清扫/注油基准的制定及注油困难地点的改善 学习正确的注油技能 |
用水/能源费的减少 安全事故的减少 外加工费用的减少 |
4 |
设备总点检 |
设备点检point及点检技能的学习 清扫/注油/点检技术的统合及点检困难地点的改善 |
油种的单纯化 oil 使用量的减少 产业废弃物的减少 |
5 |
自主点检 |
4STEP block 展开及标准化 设备要素别点检技能的完全体会 设备影响品质的因子的发掘 |
消耗品更换次数的减少 平均故障间隔时间(MTBF)的提高 设备故障件数的急剧减少 |
6 |
标准化 |
制定不发生故障和不良的基准 品质保全基准的标准化, system化 运转员的专业化(日常点检及补修) |
设备 trouble时可以紧急采取措施 平均修理时间(MTTR)的缩短 设备信赖性的提高 |
7 |
自主管理 |
现工程/设备状态的维持 维持基准的改善及标准化 |
设备突发故障zero状态的维持 设备突发不良zero状态的维持 高品质工程、高生产性设备状态的维持 |
表5.1 自主保全步骤
自主保全活动的七个步骤都有其各自不同的活动要点,只有对每个步骤的活动要点全面的理解,才能对自主保全活动有一个整体的把握,从而更好地做好自主保全活动,为企业挽回不必要的损失。在各阶段的实施过程中,都要经过小组、厂级、TOP三级诊断(见图5.2),合格后才能进行下一个阶段的活动。
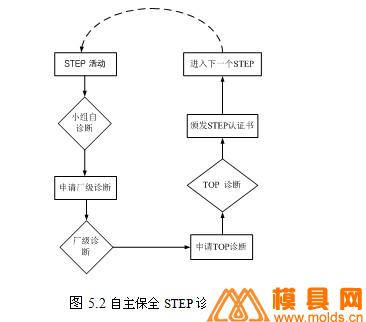 5.1.1 第1阶段 : 初期清扫 初期清扫是5S活动的延续,初期清扫活动的目标是通过清扫发现问题点,通过参与 My-Machine/My-Area活动制定活动小组的MAP,全员共同参与,寻找生产现场的不合理,寻找各种浪费要素的根源,确保品质及高生产性的活动。图5.3为化纤厂红旗小组MAP。
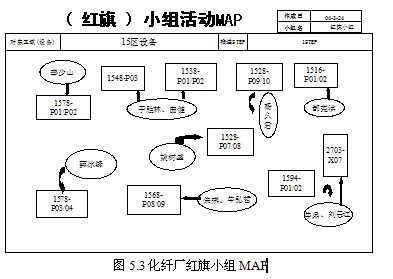 5.1.2 发生源、困难部位对策 发生源、困难部位对策活动主要是寻找引起问题的根本原因,分析真正原因。这个阶段的主要目的就是创造舒适的作业环境,降低作业者的作业负荷,延长设备使用周期,提高生产性,使操作人员具备改善设备的能力,形成挑战更高水准的改善的自信心,培养解决问题能力,制定出防止不良再发的对策。 这个阶段的主要活动方式为对发生源、困难部位进行Why - Why分析。Why - Why分析不同于传统的思考方式,Why-Why分析是对设备运转不良、故障现象所产生的原因, 通过重复Why的形式,系统地、彻底地追究原因和结果的关系,寻找其根本原因,并得到防止再发对策。Why-Why分析是针对设备问题展开的思维活动,它的意义不仅仅表现在改善设备状况上,还在于Why-Why分析使人的逻辑思维水平趋于理性和规范。图5.4为化纤厂红旗小组的针对泵轴承箱温度过高进行的一项Why - Why分析。
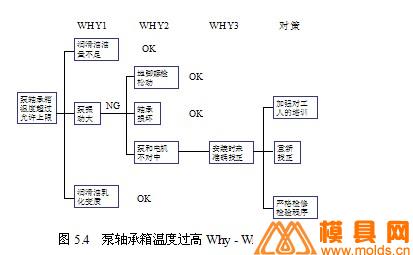 5.1.3 自主保全基准书的制定 活动的目的提高设备的可靠性和保全性,同时制定容易遵守的基准。建立自主管理体系,防止设备劣化。自主保全基准书的制定是一个不断循环、不断完善的过程。自主保全基准书的制定有以下几个步骤: ①MY AREA的再指定 小组内My area的再次指定,责任分担,并对设备进行充分了解,调查过去的故障、不良履历等。 ②制作自主管理基准书 结合中石化总公司设备完好制度制规范各设备自主管理基准书。 ③制定自主管理实行计划 制作个人、小组自主管理实行计划书,制定每月活动计划。 ④提高自主管理能力 小组成员之间传达教育自主管理基准书的内容(利用基础知识OPL),评价教育结果。按标准实行,提高现场管理水平,提高不合理改善、目视化管理、各种标示管理的水平,集中改善小组担当区域中薄弱工程。 ⑤完善自主管理基准书 通过实践找出自主管理基准书内容的不合理,进行改正。
5.1.4 总点检 总点检是进一步培养操作人员设备技能的活动,通过学习构成设备的6大系统的结构与功能, 理解正确的操作方法,成为熟练操作者的过程。总点检步骤如图5.5所示:
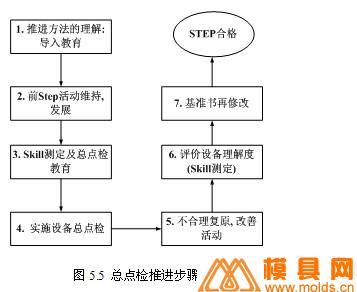 所谓的设备6大系统是指润滑系统、油压系统、空压系统、驱动传动系统、电装控制系统、插入部件等系统,工作点指设备进行生产活动的控制点。如下图5.6所示:
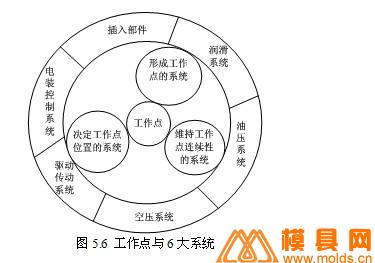 正确理解掌握关于设备的知识和功能,理解设备的构造、机能、原理,清楚什么是设备的良好状态,如何保证设备的良好状态等知识。
5.1.5 自主点检 重新研究到现在为止制定的各种基准,明确点检项目,调查到现在为止的故障、不良、点检失误及防止内容,通过重新研究点检项目是否有遗漏,持续改善,使设备的可靠性要不断的提高,形成点检的效率化和没有点检错误的状态。制定自主保全新基准
5.1.6 标准化 在自主点检维持的状态也要推进改善,记录不良、故障、临时停止,把对策和复发防止包括到基准的改正。然后着眼于人的技能,把自己的业务按责任联系起来,要确实的进行对此的持续管理,把操作人员的作用延伸到设备的相关工作,寻求更彻底的损失减少。
5.1.7 自主管理的彻底化 在这个阶段,以“改善是无限的”的思考继续挑战,把各个人都看成是公司的动力系统,把他们发展成为可执行公司方针、课题的人员。这是自主保全的最高境界。
5.2 计划保全
为了防止生产设备的意外故障,按照预定的计划进行一系列的预防性修理,这就是计划保全。计划保全的主要目的是消除故障的发生,也就是提高设备的可信赖性,防止故障的发生,以求达到零故障和零不良;另一个目的是在实现零故障及零不良的过程中,使保全人员的技术能力得到提升。 计划保全和自主保全是设备保全的两个方面,缺一不可。自主保全强调企业的员工自发、自主地对企业实施全面地管理、维护和保全;计划保全则是企业有计划地对设备进行预防性的管理、维护和保全。因此,两者的实施主体有所区别。与自主保全类似,计划保全也有几个主要的推行步骤。这些步骤将计划保全具体化,使之变成可执行的方法,使管理者有重点、有内容的推广和管理。这五个步骤分别是保全情报的整理、计划保全的导入、故障解析及改良保全、计划保全的扩大、计划保全质的提升。
5.2.1 保全情报的整理 只有对每台设备具备充分的认识和了解,根据设备的使用年限、操作要点等数据,才能制定相应的保全和维护的措施和计划。天津石化公司这方面基础较好,制度很完善,设备与生产的数据完整,设备的购买、验收情况,平时的保全,故障产生的时间、状况、原因及解决方法等记录得很详细。 对于设备的保全记录,应进行科学详细的分析,分析数据的规律、机器故障发生的环境、故障原因等,由此制定出合适的保全计划,从而防止故障的发生。天津石化公司进行平均故障时间、保全月报、计划保全比率等多种数据的统计。 ◎平均故障时间 MIBF,是Mean Time Between Failures的缩写,即平均故障时间,是指设备在一般的情况下平均出现一次故障的时间,它的用处主要有四种:对零件寿命周期推估、给最佳修理计划的制定提供依据、是点检项目基准的设定依据、是修理备品的库存基准。 ◎保全月报 保全月报就是每个月对设备的计划保全情况编写的报告,包括已经解决的问题和尚未解决的问题,以及下一步设定的保全目标。根据设备的性能及保全是否良好,参考设备每月的故障发生次数来制定目标。 ◎计划保全比率 计划保全比率是指已实施预防保全设备占工厂设备总量的百分比。计划保全比率越大,说明已实施预防保全的设备越多,计划保全工作做得越好。
5.2.2 计划保全的导入 设备的计划保全导入主要包括设备的选定,保全基准的制定,保全方式的选择和保全计划表的制定。中石化行业有一套严格的行业标准,其检修维护规程严格规定了保全基准和保全方式等,天津石化各分厂据此制定出保全计划表之后,根据表中的内容逐项检查,确定保全计划的实施。
5.2.3 故障的解析和改良保全 通过专业人员向普通员工讲解,使员工了解到故障的原因,确定是多发故障、经常发生故障还是重大故障,然后找出排除故障的方法。解决了一次故障之后,防止故障的再次发生成为首要问题。通过分析由设备管理部制定新的标准,最后根据标准进行日常的管理,防止故障的再次发生,这就是改良保全。
5.2.4 计划保全的扩大 计划保全不仅要在生产设备上实施,而且应推广到其他方面。如天津石化进行保全效率化的研究、制定生产历程表和保全历程表。这些规章制度的确定可以大大缩短整修的时间。
5.2.5 计划保全质的提升 计划保全质的提升是计划保全的最后一个步骤,计划保全体系的确立,对计划保全工作进行检查,并在计划保全的整个过程中不断地完善。通过这样的计划保全活动,能够使计划保全产生质的提升。
5.3 个别改善
个别改善的定义是为了获得经营成果,而进行的课题解决活动。 所谓生产效率就是对生产所需投入(投入:材料、人员、设备、能源等)最小化,获得最大产量(产出)的同时提高附加值和降低制造成本。 设备综合效率OEE(Overall Equipment Effectiveness)是国际上评估企业管理水平的常用指标。计算公式如下: 设备综合效率(OEE) = 时间稼动率 × 性能稼动率 × 良品率 其中:时间稼动率= 100% 性能稼动率= 100% 良品率= 100% 设备综合效率是TPM活动的一项重要管理评价指标。从硬性方面来看,它是从阻碍设备效率的损失着手,藉由自主保全、计划保全、个别改善活动,使设备更有效率地运作;从软性方面来看,对自主保全活动及计划保全体制的健全,能够产生一定的效果。其步骤如图5.7所示:
 5.3.1 天津石化公司个别改善活动通过以下方面谋求数量上的提高 ① 提高设备效率 开展设备效率化活动使设备在单位时间内产量最大化。 ② 提高人的效率的活动 通过提案改善制度,使员工不断改进作业方法和手段,提升工作效率。 ③ 提高管理效率的活动 确保生产的通畅,把物流损失降低到最小。
5.3.2 天津石化公司个别改善活动通过以下方面谋求质量上的提高 ①提高品质的活动 通过减少不良或返修作业,减少品质的不稳定性。 ②推进无人化活动 追求无人运转的条件,进一步谋求在此基础上提高生产量的活动。 个别改善的最终目的是为了充分发挥设备固有能力,发挥人员自身能力,把人与设备系统维持在最高极限状态。以此结果在不影响设备协调性的情况下增加附加值、达到降低成本。
5.4 教育训练
对各个层次的员工进行系统的TPM培训,对于企业深入开展TPM活动是很有必要的。培训的目的主要有两个:让员工理解TPM活动的基本内容和推进程序,使员工充分理解开展这项活动的重要性,改变员工的旧有观念。TPM的培训应贯穿TPM的全过程,在调查研究的基础上有准备,有实施,有检查,有修正。培训的内容应紧密结合设备保养和维护,联系生产现场实际。 为了提高各级管理人员对TPM活动的理解及掌握如何开展TPM活动的方法,使公司TPM活动能有效、深入地推进,天津石化公司聘请我国TPM专家李葆文教授进行了TPM管理培训,另外国际TPM活动咨询机构----韩国TMI咨询公司也对天津石化公司TPM活动定期进行相关知识进行培训,培训对象包括公司相关领导、各职能处室主管、专业人员,以及各二级单位主要领导、相关科室负责人、生产车间主任、设备主任、技术员等。培训结束后,公司还组织了知识竞赛、考试等。除了正规的集体学习,天津石化在TPM活动中广泛开展了OPL(One Point Lesson)的小组教育活动。图5.8为乙烯装置辉煌小组的一项OPL。 OPL 别名叫“ 10分钟教育”,是指把一个项目在一张纸上进行整理后,以小组成员为对象进行5~10分钟的教育,解除疑问点的教育方法。教育内容主要包括: ① 基础教育 : 设备的结构、点检、处理方法等的基础知识内容。 ② 改善事例 : 适用其他工程的改善事例。 ③ 事故事例 : 其他工程的故障事例、灾害事例等。 OPL教材由每个小组成员自己制作,可以包括设备知识,TPM理论知识,改善事例,安全等各方面的内容,目的是提高每个员工的素质。每个员工在亲自制作教材的过程中,通过查找资料,可以提高自己的知识水平,另外活动时,为小组其他成员讲解,可以使大家共同提高。OPL的内容应该针对一个点详细具体的说明,可以利用图表等手段,清晰明了,易于讲解、易于接受。小组对每名成员OPL制作数量和质量进行管理,促进员工不断学习,提高自己对现场的认知水平。天津石化TPM活动中,各个小组根据自身的情况,创造了一些具有特色的教育形式,例如乙烯厂辉煌小组,在进行OPL教育的基础上,创立了LL(Local Lesson)现场教育模式,即以TPM活动小组为单位,由车间技术人员到设备现场实地进行讲解,以设备的结构、性能、原理、用途、维护保养、操作注意事项等为主要内容,取得了很好的培训效果。
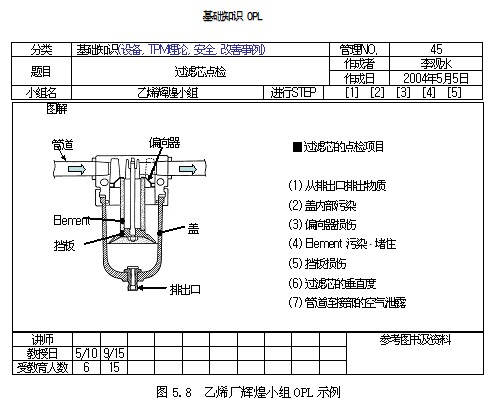 5.5 间接部门事务效率
间接部门是指那些不直接参与生产活动的部门,间接部门的效率改善活动可以参考生产部门的改善活动进行。间接部门进行效率改善的目的是:追求间接业务的效率化,充分发挥赋予组织各部门的机能,以及为企业培养维持长期改善活动的优秀人才。 当TPM现场管理被应用到事务间接部门的时候,实施关键是树立事务工厂的观念,即将一个部门视为一个工厂,大力倡导员工的自主合作。实施TPM的主要目的是实现所有生产过程的效率最大化,有效地满足客户需求。因此,在事务间接部门实施TPM,就应该将整个工作流程视为产品的生产过程,把该部门当作一个收集、加工、提供情报的事务工厂,从降低损失的角度出发开展好TPM活动,如图5.9所示:
图5.9 树立事务工厂观念
天津石化公司在事务部门中推行TPM,简化操作规程,力求所有生产过程的效率最大化,将整个工作流程视为产品的生产过程,从降低损失的角度出发开展TPM活动,从而追求事务效率的最大化。
5.6 安全环保
自主保全、计划保全、个别改善以及事务间接部门的效率化,全员知识技能的提升等这些目标达成后,并不能代表整个TPM活动的成功,因为还有一项最重要的就是“职业安全”,所以在八大支柱中特别强调安全环境的管理。依据TPM的工业安全管理原则:凡可能导致劳动灾害、工业安全事故的发生源,务必使其明确化,且要用心考虑其对策并加以实施。正如将“以设备来确保品质”的TPM活动运用在工业安全上的话,那么TPM的工业安全管理即成为“工业安全的达成要以设备来确保”,以达到工业安全管理的终极目标。 在TPM的改善范畴里,有关自主保全、个别改善的进步非常惊人。但关于工业安全的部分,TPM却未得到有效运用。由于化工生产工艺复杂,介质高温高压、易燃易爆,操作连续性强,设备大型化,自动化程度高等特点。安全问题往往不能容忍TPM初期的学习过程。 天津石化对安全工作十分重视,于2002年在全公司推行了HSE管理体系。HSE是健康(Health)、安全(Safety)和环境(Environment)三个词的首字母缩写。H(健康)是指人身体上没有疾病,在心理上保持一种完好的状态;S(安全)是指在劳动生产过程中,努力改善劳动条件、克服不安全因素,使劳动生产在保证劳动者健康、企业财产不受损失、人民生命安全的前提下顺利进行;E(环境)是指与人类密切相关的、影响人类生活和生产活动的各种自然力量或作用的总和,它不仅包括各种自然因素,还包括人类与自然因素间相互形成的生态关系的组合。 HSE管理体系从其功能上讲,它是一种事前进行风险分析,确定其自身活动可能发生的危害和后果,从而采取有效的防范手段和控制措施防止其发生,以便减少可能引起的人员伤害、财产损失和环境污染的有效管理模式。它突出强调了事前预防和持续改进,具有高度自我约束、自我完善、自我激励机制,因此是一种现代化的管理模式,是现代企业制度之一。从当前的发展状况来看,世界各国石油石化公司HSE管理的重视程度普遍提高,HSE管理成为世界性的潮流与主题,作为大型国有企业的天津石化以HSE为管理体系开展TPM安全活动,在国内尚属首例,天津石化HSE体系中的TPM活动如图5.10所示:
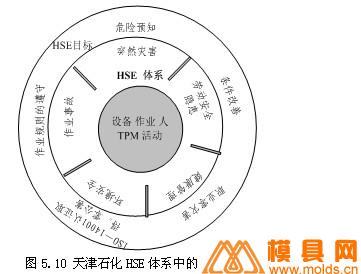
天津石化公司将安全卫生环保观念融入日常生产生活中。天津石化依照TPM安全卫生环境管理分科的活动,并遵循HSE体系要求制定了若干活动计划及实施了各项零事故、零灾害的活动,具体项目如表5.2所示:
活动项目 |
活动内容 |
劳动灾害预防 |
.零灾害奖励活动
.安全巡查的实施(回/月)
.定期的自动检查实施 |
健康管理 |
.特别作业者的健康检查
.一般人员的定期健康检查 |
环境管理 |
.ISO-14001认证取得
.一般环境测定的实施(照明、噪音等) |
安全卫生
教育训练 |
.新人安全卫生教育训练
.特殊疾病、危险的教育
.危险预知训练
.紧急应变组织的教育训练
.火灾预防的教育训练 |
表5.2 天津石化安全活动内容
第6章 天津石化TPM实施分析
通过推行TPM活动,天津石化建立了生产和设备监护管理统一网络,改变了过去生产工人只管操作,修理工只管修理的局面,使设备的清洁保养,成为修理工、操作工自觉自愿的行为。生产组织体系和设备管理组织体系发生了本 质的变化,如图6.1所示:
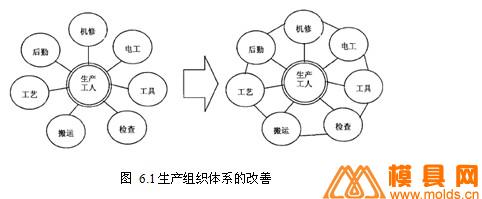
TPM管理理念倡导全员的参与,引导自主的工作,追求最高的生产效率,营造绿色的工作环境,努力实现设备故障为零,事故为零和缺陷为零等管理目标。TPM推行三年来,TPM活动得到了公司领导层的大力支持,无论是推行氛围、领导的认知程度、员工的自主参与和工作环境、现场设备管理都发生了明显的变化。设备综合效率明显提升,装置非计划停机率大幅下降,见表6.1。
时间 |
生产装置非计划停车时间(小时) |
2003 |
908 |
2004 |
101 |
2005 |
42 |
表6.1 天津石化公司生产装置非计划停机统计
通过小组重复的5S、自主保全、个别改善等活动,改善了现场面貌和工作环境,方便了员工操作和日常巡检,减少了误操作;员工从初始的不理解、不支持,有情绪逐步转变为自觉对设备进行维护保养;同时员工通过持续的OPL教育,对设备的结构、原理、设备点检内容、TPM知识等有了进一步的理解。另外各活动小组成员集思广益,开发和研制了一些实用的清扫工具,大大提高了活动的效率。同时也提高了员工关心现场、研究现场的热情。2004到2005年期间,公司发现不合理项24865项,改善复原不合理项21914项(数据详见附表1和附表2)。下面我们针对推行过程中的实际问题,从管理制度、企业文化、TPM本土化等方面加以分析。
6.1 公司管理模式的改善
天津石化在推行TPM过程中,不断完善管理制度,根据新的IEE指标对设备进行了分级管理,备件工作中引入了3A模式,收到了良好效果。
6.1.1 TPM指标修正 在TPM推行过程中,我们发现直接引用TPM的三大指标对于化工企业不太适合,OEE缺乏系统性,MTTR和MTBF缺乏经济性,造成保全活动中,为了追求维修速度产生了“以换代修”、“集成配件”等现象,导致维修费用大幅提高。针对这些问题,我们对OEE指标进行了修正,不再片面追求MTTR和MTBF。由于化工生产过程均在密闭容器进行,属于连续化生产,一般的设备都有备用设备(一般为一开一备),而对于生产系统来说,关键设备停车1分钟和停车5小时区别不大,因为一旦停机,原因分析确认、整个系统的恢复等需要很长时间,对于化工企业而言,在制造业很适用的OEE指标缺乏系统性,所以我们,提出了基于 TOC 理论的 IEE 应用模型,将定性与定量相结合,以期弥补OEE的不足,提高其有效性。在企业的整个经营业务流程中,任何一个阻碍企业去更大程度增加有效产出或减少库存和运行费的环节,就是一个“约束”,通常也称作“瓶颈”。TOC 的管理思想就是首先抓瓶颈,使最严重的制约因素凸现出来,从而从技术上消除了“避重就轻”、“一刀切”等管理弊病发生的可能。由此,短期的效果是“抓大放小”,长期的效果是大问题、小问题都没忽略,从而使企业整体生产水平和管理水平日益提高。
OEE由三个基本元素构成:可用效率(AE)、性能效率(PE )、合格品率(RE )。
OEE 计算模型如下
OEE=AE×PE ×RE
修正后的指标:设备固有效率(IEE)=AE×IOE×RE×PE
其中:固有操作效率(IOE)=(AH-IHW)/AH
AH- 设备完好且能进行工艺的时间
IHW- 设备因缺料而闲置的时间
从上述的公式推导中可知,OEE≧ IEE(此处OEE 指企业根据历史数据定出的计划 OEE值),当IEE的值越接近OEE值 ,则该设备就越有可能成为瓶颈机台,因此,可以通过比较两者的值进行瓶颈识别。 针对以上问题,天津石化采取了以下措施, ① 设备分级 按照IEE值的不同,天津石化将现场设备按照特种设备、重要设备、一般设备分成ABC三级进行管理,其中特种设备是生产装置的核心设备,重要设备会对装置的运行效率产生较大的影响,一般设备对生产影响较小。针对不同的设备分类实行不同的管理制度,以提高有限资源的合理利用。 ②考核指标多样化 对于A类设备,考核指标为故障停机次数,通过检查和监测,逐步由直接预防维修过渡到预知维修;对于B类设备,考核指标为MTTR和MTBF,以直接预防维修为主,兼顾采用预知维修;对于C类设备,考核指标为设备完好率和维修费用,以事后维修为主。
6.1.2 备件3A管理模式 在TPM的实际推行中,在进行5S、自主保全、个别改善等活动时,一个显著的趋向是TPM活动本身有“改善过度”之嫌,反映在备件管理工作中,合理甄别备件购买和储备量在实际操作中意义重大。我们按照IEE 理论,对设备进行ABC分类后,又对部件作ABC分类,最后对零件作ABC分类。需要说明的是,IEE指导下ABC分类更加重视设备在生产流程中的作用,注重设备停机对生产的影响,造成的后果。详细分类如下: 设备的ABC分类 A类设备(特维设备),对生产直接影响、影响很大的设备; B类设备(重要设备):对生产影响较大的设备,如能源、气体供应设备;或虽在主流程上,但不构成很大影响的设备等等; C类设备(一般设备):对生产影响不大,故障后可以等待修复的设备。 部件的ABC分类: A类部件:设备的核心、主要负载部位,对设备生产运行影响直接,影响重要,发生故障后果严重、停机损失严重; B类部件:设备的较重要部位,发生故障影响设备功能、产品质量、生产效率和安全环保,但不会造成严重停机损失; C类部件:设备的辅助部位,发生故障暂不会对设备功能、产品质量、生产效率和安全环保产生即时的影响。 零件的ABC分类: A类零件:部件的核心、主要负载部位,对设备生产运行影响直接,影响重要,发生故障后果严重、停机损失严重; B类零件:部件的较重要部位,发生故障影响设备功能、产品质量、生产效率和安全环保,但不会造成严重停机损失; C类零件:部件的辅助部位,发生故障暂不会对设备功能、产品质量、生产效率和安全环保产生即时的影响。 我们可以由设备、部件和零件的ABC分类派生出从AAA,到CCC共27种零件类别。然而,为了压缩库存,仅有若干类纳入库存结构模型管理范畴,其余类均作零库存处理, 第一级:AAA,BAA,ABA,AAB;即靠近三维坐标系原点小三角形里的四个点,代表了最重要,需要做冗余库存的零件。 第二级:ABB,ACA,BCA,ACB,ABC,AAC,BAC,BBA,CAB,CBA,BAB,CAA,BBB;即夹在靠近原点小三角形和中间大三角形之间的点,代表了较重要,可以做一般库存的零件。 第三级:ACC,BCB,CCA,CBB,CAC,BBC;即夹在中间大三角形到原离原点小三角形之间的点,代表了不重要,可以做短缺库存的零件。 第四级:BCC,CCB,CBC,CCC;代表最不重要,可以只存信息,不存实物的零件。 为了便于分析,我们可以用一个三维正方体来表示备件库存结构,正方体在原点的顶点代表AAA,即最重要备件,远离原点的顶点代表CCC,即最不重要的备件。我们以靠近原点的远近来区分重要程度,以两个垂直AAA-CCC对角线的三角形为分界面,如图6.2所示。这样得到四个不同的级别。
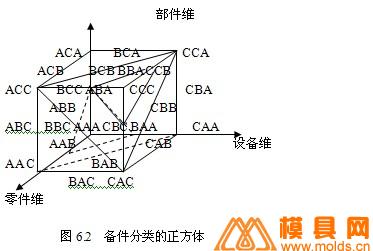 从2005年5月起,我们对备件管理引入了3A管理模式,有效地解决了库存增加,更好地保证了TPM的推进。
6.2 TPM本土化的分析
任何一种企业管理理论和管理模式都有一定的适用条件和范围,管理模式是特定的社会、经济、文化、历史传统等诸多因素作用的结果。因而现代企业管理虽有共同的一般性原则,但企业管理模式没有也绝对不可能有普遍适用的、一成不变的最佳模式。福特公司向日本学习TPM,形成了一套适合福特公司的TPM模式,称为FTPM。在FTPM中最显著的一点就是“首先取得工会的支持”是推进FTPM的一个重要前提条件,这是结合美国国情提出的。英国TPM专家Pieter Will Mont撰写了《TPM西方模式》(TPM-The Western Way)一书,专门介绍了英国企业推行TPM需注意的问题。各国学习TPM都应结合各自的国情、厂情作了适应性的改变。坐落于中国境内的日资企业(如天津三菱化学、日野电机等),虽然带来了日本原装的TPM,但在推进中仍有困难,推进效果虽好于一般的中国企业,但是生产现场与日本国内无法相比。可见如果不能对应中国国情适应性地改变TPM,即使是“行家”也会栽跟头。中国许多企业在这方面做得也不是很好,要么生搬硬套教条主义,不敢改动;要么不知该改什么,该坚持什么,往往迁就落后放弃TPM管理原则。天津石化TPM推进中,我们对小组活动和企业文化建设方面进行了有益的尝试。
6.2.1 TPM的小组活动的改进 TPM实施中强调生产管理的全员参与。“全员”成为这一管理模式的理念和精髓,也是最难跨越阶梯。无论在欧洲、美洲,还是在中国,TPM在不少企业的推行或者是虎头蛇尾,或者是流于形式,也主要因为“全员”不彻底。这主要是由于各国的国情不同,文化不同,对“全员”理念的认同程度、贯彻力度有所不同所至。例如,一些西方国家认为TPM使工人劳动强度增加,企业的工会或劳工组织出面对TPM加以抵制。还有一些西方国家的工人并不情愿做超过工资所得的“额外”工作,执行TPM十分勉强。中国的企业在推行TPM时,也遇到两方面的困难:一是操作工人缺乏自主、主动参与TPM活动的积极性;二是工人的文化素质偏低,很难适应越来越先进的设备维修,使TPM的“自主维修”难于操作。一般来说,TPM小组活动逐渐成熟的过程由四个阶段组成: 自我发展和启蒙阶段 员工从原来的被动参与被逐渐诱导进入要求学习技能,要求掌握设备结构和原理的状况。员工从清扫之中发现了不少问题,产生了解决问题的欲望。 改善活动参与阶段 通过有组织地提案改善活动,使员工由动手改向动脑。当某些改善行为取得成功时,就更增加了员工的信心和成就感。 难题攻关和自主学习阶段 一些简单的问题解决之后,会有一些比较棘手的复杂问题暴露出来,这是员工现有的知识不足以解决,这使得员工产生强烈的学习愿望,经过自学或公司组织的技术培训,员工尝试用所学的知识来解决比较困难的问题,团队协作共同解决难题的风气逐渐形成。 自主维修和自主管理阶段 小组积极的解决工作中的问题,小组成员的技术水平已经可以对设备进行自主维修,而且大部分的维修项目都能由员工自主解决。 如果没有员工的广泛参与,TPM就难免掉入形式主义的深渊。TPM通过自愿的小组活动来实现,这种自愿不是想做就做,不想做就可以不做的自愿活动。 由于中国和日本等国的国情不同,在天津石化这样的中国国企内完全依靠员工的自主参与很不现实。我们通过研究,采取了以下措施:提倡和鼓励“全员”参与意识,但是不完全寄托在员工的“自主”参与上,而是根据企业的设备状况、工人素质和技术水平,制定可以指导操作工人、维修人员及生产辅助人员“全员”参加的设备管理作业规范,通过宣传、推广和培训,形成可执行的制度准则。在具体工作方式上不是从一开始就一味地追求全员的概念,而是对小组活动的成熟过程进行客观分析,通过小组成员的提案、OPL等多种形式,在全公司内形成学习TPM的氛围,吸引员工的兴趣,并通过奖励以及其它有效的激励方式,调动员工的积极性。 在天津石化除了采用了专用项目奖金的物质奖励与TPM评比奖励的激励方式外,还按照TPM推进手册还尝试了实行了以下几种激励方式: ①冠名法 是指以员工的名字命名一个优秀班组、提案改善、作业程序等,如“某某作业法”、“某某班组”等。 ②视板法 即设计一块面板,将TPM活动的计划和取得的成绩,以及提案改善等内容展示出来,树立模范,激励员工把工作做好。 ③口号法 即全体人员,高呼TPM活动确定的目标,来激励人心,鼓舞士气。 通过实践,我们发现冠名法和视板法很符合中国人的传统心理,是很好的激励方式。,而在国外作用最大的口号法在天津石化并不灵验,相反员工们手执TPM手册,全体高呼口号时,却都显得迷惑和热情不足。这是为什么呢?据日本TPM文献记载,TPM产生于上世纪70年代左右,TPM的口号法是借鉴了当时中国的实际经验,中国几亿人通过每天喊口号,凝聚人心方面效果出奇的好。但在经过文革洗礼后的中国,人们的观念已经发生了变化。我们通过在公司内的调查发现大约80%以上的人认为这种手举书本、高喊口号的行为是不理智的,是愚蠢的。这和我们的社会文化与历史文化有关。通过和TMI公司协商,我们去掉了喊口号的环节。由此不难看出,在TPM推进过程中,不能一味机械模仿,应该深刻认识中外社会和历史文化的差异。
6.2.2 TPM与企业文化 任何管理都植根于一种文化之上,社会文化背景是管理赖以生存的土壤,有什么样的社会文化环境,就要求有什么样的管理行为和方式与之相适应。任何一个国家的企业管理都建立在本国国情基础之上,被本国人民接受。由生产关系和传统文化决定了不同国家企业管理的特殊性,这也正是企业管理生命力的重要表现。 企业文化是指在一定的社会经济条件下通过社会实践所形成的并为全体成员遵循的共同意识、价值观念、职业道德、行为规范和准则的总和(Schein,1984),是一个企业或一个组织在自身发展过程中形成的以价值为核心的独特的文化管理模式。企业文化是社会文化与组织管理实践融合的产物。企业文化是西方管理理论在经历了“经济人”、“社会人”、“自我实现人”与“复杂人”假设之后,对组织的管理理念、管理过程与组织长期业绩的关系的又一次重新审视。 推行TPM产生的有形效果主要是提高设备综合效率和降低各种损耗等,这是显而易见的。推行TPM所产生无形资产对企业的的影响很大。而TPM所产生的无形资产与企业文化的又是不可分割的。员工是企业文化的载体,而推进TPM和建设企业文化的关键是企业能否调动员工的工作积极性。一个人是被制度约束着工作的效率高,还是发自内心的被使命感驱动工作的效率高?这个答案不言而喻,被使命感驱动的工作激情,是任何奖惩制度无法达到的。 TPM已经在天津石化公司全面推行,但应清醒地认识到TPM推行不仅是物质层面上的内容,而更多在精神层面。不能只看到小组活动进行的如火如荼就认为TPM推进的很好,还要着眼于企业文化的建设和员工素质的提升,如果只在技术层面上推行TPM显然不能实现我们预期的目的。 企业文化要为企业发展、员工利益和社会带来物质和精神利益。企业文化建设是务实而不是务虚,也不是一般的政治宣传,而是企业管理的一项根本措施。需要领导者的提倡、策划以及实施、检查等具体工作。企业文化是一项以人为本的复杂工程,不是几个领导讨论制定的标语口号,也不是一时的经验总结,而是在长期的工作实践中逐渐形成的。天津石化还应充分认识到建设优秀企业文化对TPM推进的重要作用。
6.3 TPM与公司其它管理制度
天津石化在学习国外先进管理制度方面,一直走在同行业前列,从80年代以来一直推行由政府部门倡导的TQM,2000年通过ISO9000认证,2002年通过ISO14000认证,2002年推行HSE管理体系, 2003年导入TPM。2005年3月在全公司内启动了ERP(企业资源计划)。下面就它们的相互关系分别讨论。
6.3.1 TPM与TQM TPM是TQM的设备保障体系,当TQM要求将设备维修作为其中一项检验要素时,发现TQM本身似乎并不适合维修环境。这是由于在相当一段时间内,人们重视的是预防性维修(PM)措施,多数工厂也都采用PM,而且,通过采用PM技术制定维修计划以保持设备正常运转的技术业已成熟。 而在通常的维修过程中,很少或根本就不考虑操作人员的作用,维修人员也只是就常用的并不完善的维修手册规定的内容进行培训,并不涉及额外的知识。许多公司很快意识到要想仅仅通过对维修进行规划来满足制造需求是远远不够的。 从理论上讲,TPM侧重于维修。它与TQM相比有以下几点相似之处:(1)要求将包括高级管理层在内的公司全员参与;(2)要求必须授权公司员工可以自主进行校正作业;(3)要求有一个较长的作业期限,这是因为TPM自身有一个发展过程,贯彻TPM需要约一年甚至更多的时间,而且使公司员工从思想上转变也需要时间。 TPM将维修变成了企业中必不可少和极其重要的组成部分,维修停机时间也成了工作日计划表中不可缺少的一项,而维修也不再是一项没有效益的作业。在某些情况下可将维修视为整个制造过程的组成部分,而不是简单地在流水线出现故障后进行,其目的是将应急的和计划外的维修最小化。
6.3.2 TPM与ISO9000/14000 ISO9000/14000是 TQM和TPM的标准化框架。ISO9000系列标准的核心是产品质量。 ISO1400标准借鉴和吸收了ISO9000,ISO14000管理的核心是环境因素。概念上 ISO9000 属于标准范畴,而 TPM与TQM 则属于实践科学的范畴。TPM与ISO9000的区别见表:
区分项目 |
ISO9000 |
TPM |
目的 |
追求质量管理体系的持续改进,增强客户满意。 |
通过全面生产保养,追求生产系统效率的最大化 |
管理的对象 |
从品质入手 |
从生产设备入手 |
管理的方式 |
输出管理,以结果来测量 |
输入管理,以原因来分析 |
达到目的的方式 |
管理的体系化(系统化、标准化)-软体指向- |
实现现场、各生产要素(含设备等)的应有状态以及不断的改善。-硬体指向- |
人才培养 |
管理中心(质量技术如新旧QC手法) |
技术中心(设备技术、保养技能) |
活动范围 |
全员参与 |
小集团活动,并请间接部门支援 |
目标 |
稳定并提升品质 |
零故障、零不良、零灾害 |
表6.1 TPM与ISO9000的关系
PDCA 循环是 TQM 的基本方法,通用的工作程序。整个 ISO9000 标准基本上也是按此循环构筑质量管理和质量保证体系。客观地说,TQM和TPM对个案来说比ISO9000要细致,但每个企业的TQM和TPM实施方法肯定不同,ISO9000通过对TQM和TPM质量管理核心标准的认证解决了标准化的问题。图6.2为它们的关系图。
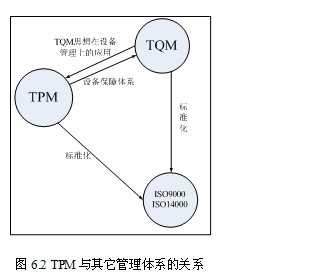 如果孤立地去推行TPM,那么TPM只能是附加的工作任务,甚至会造成与现有管理制度的冲突。推行TPM就必须将TPM与公司其它的管理体系有机融合,建立起自己的体系。如果几种管理机制各自独立运行,不知道该谁制约谁,谁包容谁,极容易造成管理上的混乱,在实际生产中形成多头管理,不可避免地造成一项生产活动要针对不同的管理体系重复管理。 从全系统的观点构建企业管理模式,天津石化在运行中对此问题进行了改进,对ISO9000内控文件进行了修正,将TPM方面的规范化文件整合为ISO贯标的C级、D级文件,编制了一体化HSE管理制度。
6.4 天津石化TPM的局限性
经过了一年多的精心准备,2005年3月天津石化在全公司内启动了ERP(企业资源计划)。天津石化采用了SAP公司的R/3系统。 ERP实现了管理的信息化,ERP不仅仅是一个软件系统,更是一种先进的管理思想、管理手段。通过ERP系统可以将很多先进的管理思想变成现实中可以实施应用的计算机软件系统,也使得许多先进的管理理念有了一种载体贯彻到企业管理的实际之中。ERP同样也深刻的影响了企业管理的方方面面。它整合了企业管理理念、业务流程、基础数据、人力物力、计算机硬件和软件于一体的企业资源管理系统。 ERP对产品的开发设计、原材料的采购、产品生产过程、销售和客户服务全过程实现质量监控。质量管理功能和物料管理、生产计划、销售、客户服务、成本等各个业务模块的集成,可以控制相应业务的操作。 TPM在实际应用中,已经形成了一整套成熟的方法和规范。但是,传统的TPM应用中,存在两个重要的缺点:一个是过于依赖手工作业、依赖大量记录在纸介质上的数据和资料,没有实现“电子化”。这种操作方法,虽然是按照TPM的规范来进行的,操作步骤也符合TPM的要求。但是,完全的手工作业显然在数据准确、缜密等方面难以尽如人意。其二是维护工作涉及到生产企业的其他职能和系统的时候,特别在这些系统是由软件系统来控制的时候,没有适当的“数据接口”,以便实现TPM与其他信息系统之间的整合。 ERP的成功应用很好地解决了这些问题。 精益生产(Lean Production,简称LP)是美国麻省理工学院数位国际汽车计划组织(IMVP)的专家对日本“丰田JIT(Just In Time)生产方式”的赞誉之称。对生产过程而言,LP与JIT的实质相同,但对于整个生产系统,LP比JIT具有更广泛、更深刻的意义,它包括了组织结构以及整个系统的改善活动。 精益生产既是一种以最大限度地减少企业生产所占用的资源和降低企业管理和运营成本为主要目标的生产方式,同时它又是一种理念,一种文化。[47]实施精益生产的过程就是追求完美的过程,也是追求卓越的过程,它是支撑个人与企业生命的一种精神力量,也是在永无止境的学习过程中获得自我满足的一种境界。其目标是精益求精,尽善尽美,永无止境的追求七个零的终极目标,即零切换浪费、零库存、零浪费、零不良、零故障、零停滞、零灾害。 ERP应该是基于企业精益生产管理系统下的信息化,它并不是简单地将现有的管理系统电子化就可成功实施的。它是在成功地进行了管理革新的基础上。事实上不在JIT模式下构建的ERP从某种意义上讲本身就不是先进的ERP。如果实施了ERP后库存依然庞大,生产工时依然不能有效控制,企业花巨资导入ERP的效果要大打折扣。当然,建立了ERP再全面推行JIT会相对容易一些,但是当企业在实现了精益生产方式后,又要请回原软件公司,再次花巨额费用追加ERP软件的功能(软件业称其为升级)来适应已改善的新的生产管理方式。 国际上众多的知名企业都是上世纪70年代至80年代初期建立了精益生产方式,然后在上世纪80年代中后期才逐渐开始实施MRP(ERP)系统。通过精益生产强化生产管理机能,通过ERP使得工作效率化、整合企业资源管理。在日本盛行的TPM,在90年代后期,随着三星、LG、现代等韩国企业,以及福特、柯达等欧美企业的成功推行,在全世界掀起了TPM热潮。 上世纪80年代以前,我国同工业化国家在企业管理方面几乎没有交流,更谈不上实际运用。因此在管理升级的道路上,国内绝大部分企业跨越了国外几十年实践精益生产的历史,直接实施TPM。国内外的咨询机构似乎没有人指出TPM这种模式是不仅有TQM的思想,更重要的是融合了精益生产的管理思想。JIT和TPM有不可分割的密切关系。推进JIT,必须避免突发性故障和瞬间停止或出现不良情况,TPM将使其成为现实;JIT在TPM的支持下将得到完全实施。从TPM在世界范围内的实例来看,越是搞JIT生产的工厂,TPM取得的成果就越好。 TQM由于中国政府多年的大力推行,在中国应用很广,效果虽达不到尽善尽美,但中国企业身体力行20余年,毕竟理论研究深入,实践经验丰富。与此相反JIT在中国几乎是一片空白,国内缺少对精益生产精通的人才,成功推行JIT的国内企业如凤毛麟角。如今国内企业导入TPM,需不需要补精益生产这一课呢?这也是国内大多数推行TPM企业面临的重大问题。我们可以不循别人所走的路,但有些地方是必须经过的。笔者认为要走精益生产、ERP与TPM一体化的道路,才能保证TPM的实施效果。 如何在天津石化这样的国企推行精益生产呢?精益生产管理方法和理论是为了解决日本企业管理过程中出现的问题而提出的,中国企业的体制不同于日本企业,中国企业的发展过程也不同于日本企业,面临的问题也不同于日本企业。IE 是精益生产的基础,近年来工业工程(IE)的一些单项技术或成果,如上面提到JIT、精益生产、5S管理,以及6σ、TPM、网络制造(CIM)、ERP等等,得到了广泛应用,但如果缺乏工业工程(IE)整个理论体系和方法的支持,忽略了应用对象的自身背景,甚至出于经济利益驱使,不负责任的炒作,往往会是急功近利、生搬硬套,这也是国内大部分企业推行TPM或ERP等效果不理想的主要原因。 国外的工业工程(IE)十分成熟和发达,作为当前工业最发达的国家,美国工业工程(IE)的发展最具有代表性。可以说,美国是工业工程(IE)的发源地,工业工程(IE)对美国的国民经济一直产生着重要的影响。在美国,企业中都设有工业工程部门。在德国,工业工程(IE)有时称为生产工程,大学里所有工程类专业的学生,都被要求在运筹学、物流或后勤学、系统工程等方面进行学习。与英国、法国等其它欧洲国家一样,工业工程(IE)师是十分受企业欢迎的,企业中的工业工程(IE)师在系统分析、系统优化、系统集成方面发挥着重要的作用。 日本自六十年代从美国引进了工业工程技术,根据本国民族文化特色加以发展、应用,创造了如准时制、精益制造、5S管理、丰田生产方式等一系列先进的生产管理模式,使企业效益成倍增长,对日本的经济腾飞起了重大作用。 尽管工业工程(IE)在工业化发达国家有着长期的发展历史,但在我国,长达半个世纪的计划经济体制以及从计划经济向市场经济过渡下的企业发展和竞争一直是在追求产品和服务的数量,而没有对效益和效率产生迫切的需求,因此工业工程(IE)这门以“软”为特征的工程技术一直没有得到普遍的认识和推广。 在改革开放经历了二十年的发展之后,中国的经济已进入了一个崭新的发展时期。从过去的资金引进,转变成为现在对技术、对管理、对人才的引进,但对管理和技术研究体系工业工程(IE)的引进意义更为深远。 结合本企业现场实际,通过IE研究制定出适合本企业的TPM和精益生产模式,这是天津石化TPM进一步成功推进的有利保障。当然有了国外几十年的成熟经验,我们只要善于学习,也许只需要几年时间。 TPM体系的发展趋势是向集成化、全员化、计算机化、网络化、智能化、专业化、规范化方向的发展。TPM在天津石化推进还不到3年时间,有些项目的的推行刚刚开始,对推进中出现问题的认识还不太全面,对其分析研究还有待进一步深入。加之本人理论水平所限,对一些问题的分析还停留在表面上,文中观点不一定成熟,在此,殷切希望得到有关专家和同行们的批评指正。
结 论
随着中国经济体制改革的深入,中国政府对石化行业保护的壁垒将逐步消失,中国的石油市场将逐步开放。天津石化公司充分认识到企业自身存在的各种弊端,借鉴国外企业的成功经验,积极推行TPM。本文运用运营管理及相关的工商管理理论知识,在对天津石化公司进行详细调研的基础上,研究了天津石化公司TPM实施过程,对实施中遇到的问题进行了深入分析和实际论证,并提出了相应的对策。 本课题取得以下主要研究成果: ①分析了天津石化公司管理现状、存在的问题与实际需要,在深入研究的基础上,明确了活动的需要。 ②在深入分析现有TPM活动体系的基础上,制定了天津石化公司TPM活动的推进步骤和具体措施,在较短时间内取得现场改善的效果。 ③在推进过程中针对国情、厂情成功地作了一些适应性的改动,保证了TPM的推进效果;修正了OEE指标,提出了适合化工行业的IEE指标,对情况相似的中国企业或中国境内企业推进TPM活动有很强的借鉴意义。 ④在HSE管理框架下整合了TPM、ISO9000/ISO14000以及和TQM等管理制度。紧密结合自身生产特点和管理实际情况建立了一体化管理体系,避免了重复性工作,取得了良好效果,对国内企业,尤其是石化企业具有很强的实践指导意义。 ⑤分析了ERP与TPM的关系,对天津石化公司TPM活动的局限性进行了深入探讨,提出了应用IE研究适合本企业的生产模式管理体系的迫切性和必要性。 本文的研究成果(除了精益生产方面)均已在天津石化公司开展的TPM活动进行了运用,取得了良好的应用效果。 本文对精益生产方面的论证,由于在天津石化没有生产实践,不能不说是一个很大的缺憾。另外本文对与TPM推行有重要影响的公司治理结构、绩效考核、新酬制度等方面,未作相关研究,也是一个不足之处。
致 谢
本论文是在导师焦叔斌教授和丁静高级工程师的亲切关怀和精心指导下完成的。导师还在百忙中,就论文的修改、课题的研究、论文的写作等进行了专门的面授。导师严谨的治学作风、广博的学识,一直激励着我,导师实事求是的科研作风和高度的责任感使我终身受益。 在收集本论文所需资料和相关数据的过程中,天津石化公司TPM活动推进领导小组、设备管理部、人教部、生产部等部门,以及各分厂均提供了极大的帮助,公司TPM推进干事孙林峰给予了无私的帮助。在此,我深表感谢。 在作者调研和论文写作期间,还得到了广州大学李葆文教授,LG化工天津公司黄国强博士,日本三菱化学天津公司奥山正美部长,以及韩国TMI公司李京斌、郑爀鎬两位TPM专门委员的指导和帮助,在此表示衷心感谢。 在论文完成之际,谨向导师焦叔斌教授和丁静高级工程师表示崇高的敬意和衷心的感谢。同时感谢本文引用文献、资料的作者!
|