|
设
备
管
理
网
s
b
g
l
.
j
d
z
j
.
c
o
m
|
 |
RAM一体化基本内容(1) |
|
|
RAM一体化基本内容(1) |
|
作者:佚名 文章来源:不详 点击数: 更新时间:2008-9-24 8:45:36  |
|
一、任务自上而下传递 正如系统可靠度分配一样,系统中的各级子系统、孙系统要有明确的任务且上下级的关系要非常清晰,这里的任务是泛指各种可控变量。 任务自上而下传递的前提是,在只考虑工厂一装置级功能性任务与故障时,保持问题的维数最低。工厂一装置级功能任务(如:在T期间内生产质量为Q的乙烯P吨),可被分解到单个流程装置的功能任务指标上。至于输出变量,可区分粗的(生产率)和细的(质量及与环境有关的变量)。区别这种类别的理由是,当其它变量保持在很小变化范围内时,工厂生产率易于控制。如果一台装置的物理输出变量保持在一定的事先设置的范围内,它就能完成其功能性任务。为了使功能性任务能顺利完成,装置的内部物理状态(如:温度、压力、组成、供应、混合效应)一定要限制在一定的状态范围内。这种状态范围的限制只有通过一定的活动(如:提供进料、冷却、封装、混合)才可完成。因此,工厂一装置级功能性任务所需要的可靠性(或可用度)必须转换成为所包含设备功能的可靠性(或可用度)。这个流程模型在转换过程中是至关重要的,因为它将物理输出行为与设备的内部状态及设备的输入动作联系在一起。图1-1所描述的是这种分自上而下任务分解的探索。
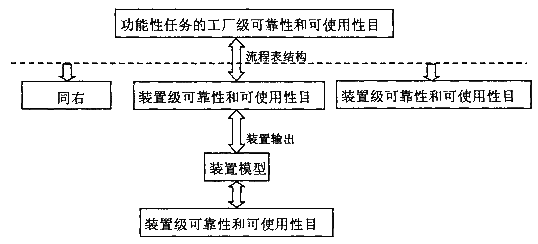
图1-1
二、设计分析与维修策略的关系 设计中要考虑维修策略是RAM一体化的基本步骤,现代化企业尤其要这样做。 随着对流程合成分解的研究,有必要应用一些可靠性理论,来识别设备部件对整个流程性能、对故障率的“浴盆”特性或其类型特性进行敏感度分析,产生不同的维修选择,并在维修费用与系统效率方面做出折衷。当给出与工厂生产方面有关的设备参数临界点信息后,就会识别或评价出以费用/效益形式表示的最佳策略(无维修设计、状态监测、计划或事后修理)。这些研究为新安全条例所需的程序打下了基础。进一步说,这些分析构成的可控结构可以引导系统本身定义一些数据存贮和经验的反馈。 三、以RAM为目标的一体化设计中维修管理的作用 有计划的、有针对性的、有层次的维修管理是RAM一体化中的“神经网络”,它能够敏感的觉察系统中某一级的问题。 表1-1所示的是以活动为导向的维修工作。把功能流程设计与RCM、维修概念、寿命周期费用(LCC)为中心的设计联系在一起。将产品的寿命周期大致分为系统的性能指标地确定、概念/基本设计(装置级)、详细工程(部件级)、工厂的建立和运行使用等五个时期。在每一时期末,经检查和认可(或批准),本时期的产品指标将确定。同样,每一时期的费用估算或预算也就被估计或计算出来。
表1-1 功能流程设计与维修概念及费用设计
寿命周期
功能设计
RCM的设计
维修概念设计
LCC评价与设计
指标(系统级)
功能指标
RCM的指标
维修概念需求
LCC指标
概念性基本设计
(装置级)
功能指标
可靠性模型分配预测
维修概念指标
LCC模型分配预测
详细工程(部件级)
部件/材料指标
可靠性模型风险分析
RCM
[1] [2] 下一页
|
|
资讯录入:admin 责任编辑:admin |
|
|
上一篇资讯: RAM一体化基本内容(2)
下一篇资讯: RAM一体化设计问题可行性 |
|
|
【字体:小 大】【发表评论】【加入收藏】【告诉好友】【打印此文】【关闭窗口】 |
|
网友评论:(只显示最新10条。评论内容只代表网友观点,与本站立场无关!) |
|
|
|
|