摘要: 电站锅炉燃烧优化控制技术能在不进行锅炉设备改造的前提下,利用锅炉运行数据和集散控制系统(DCS),通过一系列先进建模、优化和控制技术的应用,提高锅炉运行效率,降低NOx排放。由于这种技术投资少,能够充分挖掘机组运行的节能潜力,使机组始终处于最佳的运行工况,因而受到电站用户的广泛关注,并代表了下一代热工自动化发展的方向。文章就这一新技术在国内外的研究和应用情况做了阐述,简要说明了其实现原理和应用情况,并介绍了作者所在课题组在这方面所进行的一些研究和实践工作。最后对这一技术应用时遇到的困难进行了总结。
关键词: 燃烧优化;神经网络;预测控制;在线监测;均衡燃烧
0 引言
当前,我国电力行业正在由计划经济体制逐步向市场经济体制过渡,发电企业一方面面临厂网分开、竞价上网的电力市场竞争,另一方面由于能源紧张导致煤价上涨,进一步加大了发电企业的生产成本。因此发电企业迫切要求挖掘机组运行的潜力,提高机组运行效率,降低生产成本,提高企业竞争能力。同时,随着国家对电站NOx排放的限制,如何有效降低NOx排放的技术也是电厂当前关注的热点。由于锅炉燃烧优化技术能够有效提高机组运行效率,降低发电成本,并能够降低锅炉NOx排放,因此得到发电企业的普遍关注。
电站锅炉燃烧是个复杂的物理化学过程,涉及到燃烧学、流体力学、热力学、传热传质学等学科领域。任何与燃烧相关参数的检测、与燃烧相关设备的改造,都可以称为燃烧优化,包括DCS控制逻辑的优化、控制模型的设计[1]。从锅炉燃烧优化技术角度看,锅炉燃烧优化技术可以分为三类:第一类通过在线检测锅炉燃烧的重要参数,指导运行人员调节锅炉燃烧,这类燃烧优化技术目前在国内占据着主导地位。第二类燃烧优化技术是在DCS的基础上,作为锅炉运行的监督控制系统,通过采用先进的控制逻辑、控制算法或人工智能技术,实现锅炉的燃烧优化。随着先进控制和人工智能技术的逐步成熟和在工业上成功的应用,这类燃烧优化技术发展迅猛。第三类燃烧优化技术在设备层面,通过对燃烧器、受热面等的改造实现锅炉的燃烧优化调整[2]。上述三类技术在实际中各有优点和应用,但其中第二类技术不需要对锅炉设备进行任何改造,能够充分利用锅炉的运行数据,在DCS控制的基础上,通过先进建模、优化、控制技术的应用,直接提高锅炉运行效率,降低NOx排放,具有投资少、风险小、效果明显的优点,因而成为很多电厂首选的燃烧优化技术。本文主要阐述这一燃烧优化控制技术在国内外的研究、应用和发展,以及作者所在课题组在这方面所进行的一些研究和实践工作。
1 国外的燃烧优化控制技术及其应用
1.1 Ultramax公司的燃烧优化技术
美国俄亥俄州Ultramax公司开发的Ultramax系统又称为先进过程管理系统,是一个对生产操作进行日常管理的系统,能应用于各种生产过程,在此只介绍其在电厂燃烧优化方面的应用。Ultramax燃烧优化系统是将一系列代表锅炉燃烧工况的参数,比如烟气氧量、排烟温度、烟气排放物等,作为系统的输入数据,当系统取得这些样本数据后,建立锅炉燃烧特性模型,并经过软件分析,给运行人员一个优化燃烧的操作指导,运行人员根据这些操作指导进行手动操作,或将操作指导纳入到自动控制系统中进行优化调整。该系统的工作原理如图1所示。
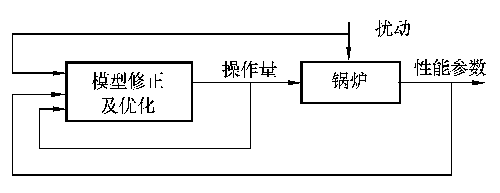
图1 Ultramax系统工作原理图
Ultramax采用了贝叶斯统计和加权非线性回归分析相结合的建模方法,可快速精确地辨识出锅炉的运行特性,并在最优化原理指导下快速寻找到最佳的控制量组合。回归模型是一个“黑箱”模型,所以为了建立初始回归模型,需要做很多性能试验。该系统最大的特点就是在每次优化后都会对数据进行分析并相应的修正模型。这样,没有起到优化效果的控制量组合就会在下一次优化时被舍弃,进而实现真正的持续优化,而且对于新的运行工况该系统也能进行优化。这种优化性能得以实现的核心就在于运用了贝叶斯统计的建模方法。该系统的优化实际上是一个在模型实时更新基础上的稳态优化。
1995年,Ultramax系统就在美国德克萨斯州弗农市的奥克拉联合发电厂666MW的一号机组上进行了开环测试,当时最多能减少18%的NOx排放,同时飞灰含碳量降低85%。目前全世界已经有30多个电厂运用了此系统,其中包括我国邹县电厂[3]。
1.2 Pegasus公司的燃烧优化技术
1.2.1 NeuSIGHT系统
NeuSIGHT系统为美国Pegasus公司应用人工智能神经网络技术设计的燃煤电厂燃烧优化控制系统,其主要功能是以提高锅炉热效率和降低NOx排放为目标的稳态优化。
NeuSIGHT系统利用DCS本身具有的数据库的数据作为数据分析的基础,经过神经网络模型在线分析,迅速得出运行参数的最优值,然后输出到DCS,DCS系统通过控制偏移量,进而实现NeuSIGHT对锅炉燃烧的优化控制。但是,这种燃烧优化控制技术并没有考虑机组运行的动态特性和过程,所以这种优化也只是稳态优化。该系统的工作原理如图2所示。
图2 NeuSIGHT系统工作原理图
NeuSIGHT系统是基于神经网络模型设计的,而神经网络模型也是一个“黑箱”模型,因此一般建立神经网络模型前要经过2~4周的锅炉变参数测试,在测试数据的基础上建立原始模型。由于煤种、积灰、结渣等因素的变化,锅炉燃烧情况要随之改变,这就造成原始模型很快就和实际情况产生偏离,因此在优化过程中NeuSIGHT系统使用了2套神经网络系统,其中1套系统的模型进行过程优化,同时另1套根据DCS的历史数据和测试数据建立新模型,一旦新模型建立就能通过模型切换完成模型的在线更新,由于神经网络训练的时间较长,所以模型更新的周期比较长。在模型基础上,NeuSIGHT系统运用GESA算法等工具实现了同时对锅炉当前工况的各个控制量进行在线优化。
NeuSIGHT系统在美国市场的占有率为40%。对于没有排放控制的电厂,Pegasus公司预计应用NeuSIGHT系统可降低NOx排放达20%~60%(一般为25%~35%)。如果电厂已经安装了低NOx燃烧器,使用NeuSIGHT系统可再降低NOx排放10%~40%。NeuSIGHT系统可降低煤耗0.5%~5%,这相当于减少了相同的CO2和SO2的排放。NeuSIGHT燃烧优化控制系统以前大多应用于旧机组的优化控制方面。目前Pegasus公司已经和许多世界知名的电力成套设备供应商,如B&W、Foster Wheeler、Siemens-Westinghouse、ABB Centrum等建立了合作伙伴关系。Pegasus的合作伙伴中的锅炉制造商对燃烧方面比较了解,他们将把NeuSIGHT系统作为其产品的附加增值来应用于最新供应合同中。但作者目前尚未检索到该产品在国内应用介绍的文献资料。
1.2.2 Power Perfecter系统
Power Perfecter系统是美国Pegasus公司另一个锅炉运行优化控制软件,国外也称它为DeltaE3系统。它基于与NeuSIGHT系统类似的神经网络技术,并增加了模型预测控制(MPC)技术,能通过建立多目标的动态优化控制器,动态调整DCS设定参数与偏置,实现锅炉燃烧优化动态闭环控制。该系统的工作原理如图3所示[7]。
图3 Power Perfecter系统工作原理图
由于Power Perfecter系统的核心技术也都来自Pegasus公司,所以相比NeuSIGHT系统,在硬件上没有变化,主要增加了动态预测功能和离线仿真功能。此外,该系统可以用来查找模型的失谐和提供偏差扰动的纠正能力。同时,该系统还可以采用动态反馈来升级模型,通过使用动态反馈,可以迅速地消除扰动偏差、模型的失谐以及传感器的噪声。
Pegasus公司称该系统可以提升0.5%~2.5%的锅炉热效率,降低氮氧化物排放量10%~30%,降低飞灰含碳量7%~9%,系统还可以改善过热、再热蒸汽品质,改善燃烧均衡性等。该系统可广泛应用于各种装机容量和类型的燃煤锅炉的优化控制,目前该产品已应用于我国山东省的华电莱城电厂1号锅炉和华能天津杨柳青电厂5号锅炉(300MW机组)上,测试报告表明应用效果良好。
2 国内燃烧优化控制技术的研究和应用情况
2.1 锅炉烟气含氧量的优化控制技术
国内早期燃烧优化控制技术的研究主要为锅炉烟气含氧量的优化控制研究。烟气含氧量代表了锅炉燃烧的风煤比,是影响锅炉燃烧效率和污染排放的关键参数。早期的燃烧优化控制主要以提高锅炉运行效率为目的,一般情况下,锅炉的效率与烟气含氧量成凸的二次曲线关系,因此这些运行优化控制的研究都是采用这一关系曲线对锅炉的烟气含氧量进行在线的寻优控制,以保证锅炉的最佳燃烧效率。由于早期锅炉效率不可在线测量,因此很多研究采用了烟气中CO含量与锅炉效率的关系作为间接寻优烟气氧量的依据。这类控制系统简单、有效,但是比较粗糙,实际应用很少,这主要是受早期锅炉可控性较差、各种分析测量仪表尚没有成熟的影响。
2.2 闭环均衡燃烧控制系统
国内另一种可以被称为燃烧优化控制的技术为闭环均衡燃烧控制系统(BCCS)。传统的燃烧控制系统的主要任务是保证进入锅炉炉膛的燃料总量与机组所需的燃料量相符,但这并不能确保燃料能平均分配至锅炉的每个燃烧器。燃料分配的非均衡性造成了燃烧的不稳定、炉膛火焰中心的偏移以及水冷壁的结焦等现象。均衡燃烧控制系统能在风粉浓度在线监测系统基础上,通过对每个给粉机转速进行控制,较好地解决上述问题。若锅炉以四角切圆方式进行燃烧,均衡燃烧控制系统能保证流经同层的每个燃烧器的煤粉浓度相等,并能够控制各个工况下总的煤粉量以最优的比例分配给各层燃烧器[8,9]。
该系统是由以主蒸汽压力为被调节量、总给粉量(燃料)为调节手段的主调节系统和以煤粉浓度为被调节量、给粉机转速为调节手段的若干个副调节系统组成的一个闭环控制系统。其工作原理见图4[10]。
图4 均衡燃烧控制系统工作原理图
由于该控制系统采用一次风管煤粉浓度作为反馈信号,增加独立的煤粉浓度控制回路,不但可消除煤粉浓度变化增加的扰动,增加主蒸汽压力控制的稳定性,同时可保证每层燃烧器风速、煤粉浓度均衡,达到优化燃烧的目的。
均衡燃烧控制系统已经在多家电厂得到应用,起到了燃烧优化控制的效果,提高了锅炉燃烧的效率和安全性。但由于该系统以燃烧器煤粉浓度测量为基础,而这一测量技术的研究目前进展很慢,只是在热风送粉的锅炉中得到实际应用,并且可靠性也不是很高,严重影响了均衡燃烧控制系统的实际使用效果和广泛推广。
2.3 电站锅炉燃烧优化控制软件OCP3
我国拥有世界上最多的燃煤电站机组,随着国家建立节约型社会的号召以及发电企业自身降低生产成本的要求,电站锅炉燃烧优化控制软件将会得到更加广泛的研究和应用。相对于国外燃煤电站锅炉,目前我国电站锅炉具有煤质多变,负荷大范围变化的特点,这导致一些进口的燃烧优化控制软件在国内应用存在很多问题,主要表现为对煤种多变的适应性差,对负荷大范围变化的适应性差,当然价格昂贵也是进口软件的一个缺点。对此,作者所在课题组经过多年的研究和开发,研制了具有自主知识产权的电站锅炉燃烧优化控制软件OCP3,与国外燃烧优化控制软件相比,该软件包是专门针对我国电站锅炉机组的运行特点而研究的,具有很好的适应性。在软件包的研究、开发和应用过程中,着重针对我国电站锅炉的燃烧特点进行了研究,并解决了下述问题[11]:
(1) 锅炉燃烧煤质的自动辨识问题。煤质多变是我国电站锅炉的特点,不同的煤质下锅炉表现出不同的燃烧特性,必须首先辨识出不同的煤质,进而进行相应的优化控制。
(2) 锅炉运行特性的非线性动态建模问题,并研究了模型的自适应更新问题。锅炉燃烧是一个非线性的动态过程,如果只是建立线性模型或者稳态模型,往往不能进行很好的燃烧优化控制。并且模型自适应也是成功进行燃烧优化控制的关键。
(3) 基于多目标优化的锅炉运行优化控制问题。针对我国目前电力市场特点,研究了多种优化目标下的优化控制算法。燃烧优化目标包括锅炉效率最佳,NOx排放最低,锅炉运行成本最低等。
(4) 锅炉机组负荷大范围快速变化中的燃烧优化实现算法。由于电力市场的原因,使得很多燃煤机组参与调峰,因此仅仅考虑锅炉燃烧的稳态优化是不够的,一个能够长期投运有效的燃烧优化控制软件必须能够实现机组动态变化过程中的燃烧优化控制。
目前该软件包已经在国产20万kW机组和进口35万kW机组上得到应用,初步测试表明,采用该软件包能够使锅炉运行效率提高0.5%左右,NOx排放降低10%~20%左右。
3 应用中的难点分析
(1) 测量问题。飞灰含碳的测量是锅炉效率计算的关键点,但目前国内的此类设备的测量滞后比较大,导致在线计算的锅炉效率不准确,成为锅炉运行优化控制的一大障碍。要实现NOx的闭环控制,同样也要求NOx的精确和快速测量,这种烟气分析仪表虽然技术和应用都比较成熟,但是设备的价格比较贵,运行维护工作量大,成为燃烧优化控制的又一个难题。现场一般都安装了氧化锆氧量计来进行烟气含氧量的实时测量,但是普遍存在测量误差大、短时间内波动大的问题,这严重影响了锅炉效率计算的准确性和闭环控制的效果。
(2) 自适应建模很有必要。入炉煤种的不稳定,再加上锅炉检修、积灰、结渣等因素的影响,使得在性能试验数据基础上建立的锅炉模型失配严重,所以如何利用最新的燃烧数据进行模型的在线自适应修正显得格外重要。
(3) 如何保证燃烧稳定下实现最大范围的寻优。燃烧优化控制的寻优范围太窄,优化后效果可能会不明显;寻优范围太广,将可能影响燃烧的稳定性。由于近年煤炭资源的紧缺,煤质经常得不到保证,因此燃烧稳定性往往被优先考虑。这使得燃烧优化控制软件需要对燃烧的稳定性进行充分考虑,而不只是简单的性能目标的寻优问题。
4 结论
随着测量和控制技术的不断进步,电站锅炉燃烧优化系统能运用先进的控制技术,在投资较少的情况下实现锅炉运行成本最低,它是提高发电企业竞争能力,建立节约型社会的重要技术手段。针对我国电力市场的特点,研究、开发和完善符合我国电站锅炉实际运行情况的,具有自主知识产权的燃烧优化控制软件势在必行。
5 参考文献
[1] 周仪琳.锅炉燃烧系统优化控制及实现方法[J].工业仪表与自动化装置,1998(4):50~53.
[2] 徐军伟,宋兆龙,王磊.电站锅炉燃烧优化技术现状和发展动向[J].江苏电机工程,2005,24,(3):6~7.
[3] 牛拥军,闫国庆.优化燃烧技术在邹县电厂中的应用[J].发电设备,2004增刊:102~105.
[4] Christopher A J, Roger L. Using closed-loop dynamic optimization to improve boiler efficiency at chemopetrol’s litvinov plant[A].Int’l Joint Power Generation Conference,Baltimore,Maryland,Aug 24,1998.
[5] R Brad J.应用神经网络控制系统在燃煤电厂上降低热耗和优化操作控制.中美清洁能源技术论坛.
[6] Booth R C, Roland W B. Neural network-based combustion optimization reduces NOx emissions while improving performance[A]. Oynamic Modeling Control Applications for Industry workshop.1998.IEEE Industry Applications 1998.30 April -1 May 1998:1 ~6.
[7] Jianhu J.Applying artificial intelligence, advanced control,and optimizaion technologies in coal fired generating units[R].2nd U S-China NOx and SO2 Control Workshop.Dalian,Liaoning Prorince.P.R.China:Pegasus Technologies.Inc,August 2~5,2005.
[8] 吕震中,沈炯.采用变频调速的均衡燃烧计算机控制系统[J].动力工程,1996,16(2):47~50.
[9] 李益国,沈炯,吕震中.均衡燃烧控制系统总体设计及关键技术问题研究[J].热能动力工程,2001(7):386~388.
|