燕山石化公司某供水车间承担为化工装置供水的任务。近几年,随着企业发展,装置扩能改造及节水减排等设施的投用,工业水负荷有较大波动,尤其自2005年11月份以来,工业水平均负荷多在900-1300t/h之间变化,该车间的水泵配置情况与设备经济运行要求之间的矛盾愈发突出;该车间水泵配置为2台小流量泵(1#、2#泵,额定出力792m3/h)、1台大流量泵(3#泵,额定出力2016m3/h),在正常负荷情况下,需2台小流量泵同时运行或1台大流量泵运行,而依靠调节水泵出口阀门进行负荷调整,导致该车间供水成本之单位水耗电大幅上扬,由0.20kW·h/t上升至0.28kw,h/t,造成巨大的电能损耗。2006年,经论证,决定采用高压变频技术进行泵的调速节能改造。
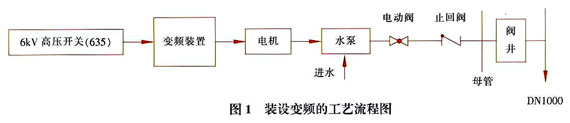
近年来,各种高压变频器不断出现,到目前为止高压变频器还没有像低压变频器那样的近乎统一的拓扑结构。根据高压组成方式,可以分为直接高压型和高-低-高型;根据有无中间直流环节,可以分为交-交变频器和交-直-交变频器。在交-直-交变频器中,按照中间直流滤波环节的不同,可分为电压源型(也称电压型)和电流源型(也称电流型)。
经调研,我们选用北京四方清能电气电子有限公司的ONMVD100M-SAN0066高压变频调速装置(为直接高压交-直-交变频器)来驱动水泵。
1 现场工艺情况
1.1 装设变频工艺流程
供水系统设量高压变频调速装量的工艺流程如图1所示。
1.2工艺控制描述
选用3#水泵(大流量泵)为改造对象;控制母管压力在规定的0.4-0.6MPa范围内,电机为JS2148-6型,560kW,配20sh-9型离心清水泵、额定流量2016t/h、扬程59m,效率为77%-83%。考虑运行安全性,变频器加装自动旁路控制柜。正常运行时,3#电机处于变频运行:当变频故障时,变频调速装置自动断开变频器的输入和输出连接,自动闭合旁路开关,实现电机工频运行,以保证水泵正常运行。
2 系统方案
2.1 主回路方案
根据使用需求并经技术方案论证,采用的系统主回路方案如图2所示。
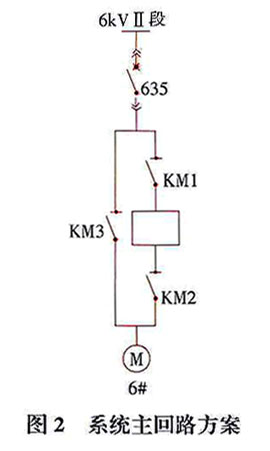
主回路采用变频调速装置加配套自动旁路开关柜配置方式。可实现电动机通过变频器的变频运行方式,或通过旁路柜的工频运行方式。图中635为6kV高压开关,KMl、KM2、KM3为旁路开关柜内高压真空接触器。
变频装置的主电路拓扑如图3所示,为H桥级联多电平逆变器。采用移相隔离变压器将三相6kV高压交流电,变换成3×5组错相的三相低压交流电,分别经功率单元整流、逆变、串联叠加形成0-6kV、0-50Hz的变频高电压输出至异步电动机。由于移相对电网侧形成了30脉动整流,即产生的谐波主要为29次和31次,输入电压、电流谐波的含量仅有1.2%左右,远低于GB/T14549-93规定小于4%的要求:功率因数均能达到0.95,效率96%以上;PWM方波的叠加使输出电压的谐波含量很小,电流波形近似为正弦波,几乎没有脉动转矩。

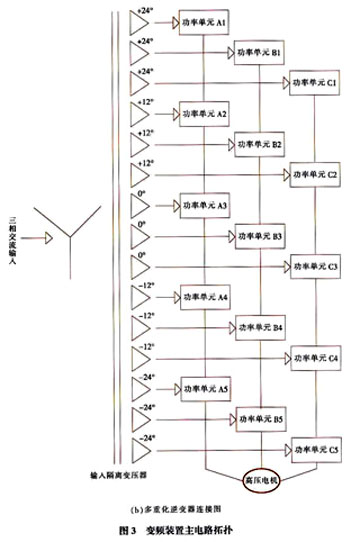
2.2控制系统方案
根据现场工艺控制要求,方案设计如下:
调速装置具有闭环,开环运行方式选择功能。选择开环运行模式,可直接对运行频率进行设定。选择闭环运行模式,可直接对水泵出口压力进行设定。
变频调速装置可控制水泵出口电动阀门的开、关操作。阀门的联动具有选择功能,允许选择“有效”或“无效”。变频器控制柜有“本地/远程”控制选择开关,可以方便地选择本地操作或远程操作,变频器支持各种通用的通讯协议。
变频调速装置可以实现在装置故障的时候自动判断、及切换到工频运行的功能,最大限度满足运行可靠性的要求。变频调速装置具备输入欠压时继续运行的功能,输入侧电压完全失电不超过3s变频装置仍然能够继续运行。
变频调速装置整合有电机综合保护系统可对变频、工频两种运行工况保护。
变频调速装置控制电源采用双AC整流、可靠性高保证不受电压跌落影响。
变频词速装置的功率单元部分采用2SD315A驱动保护电路,性能高且保护功能可靠;主控单元采用现场可编程门阵列FPGA芯片,属于硬逻辑可靠性更高;系统采用全数字化设计全中文界面。
3 变频调速装置运行及节能效果分析
通过进一步总结该车间生产工艺参数及运行情况,确定以下运行方式:
供水量小于850t/h,采用1#泵或2#泵工频运行;
供水量在850-1800t/h,采用3#泵变频运行;
供水量在1800-2100t/h,采用3#泵工频运行;
供水量在2100-3000t/h,采用1#泵或2#泵工频加3#泵变频运行。
该运行方式下,设备经济运行水平最佳。而根据该车间往年运行记录——水负荷多在900t/h-1300t/h之间波动的状况,3#泵变频调速装置具有较长的运行时间。
该供水系统主要工艺参数:母管压力0.4-0.6MPa,有较大的水压调节范围:而用水装置在短时间内负荷的变化较小,满足变频调速装置的及时反馈调节;以上两个情况为该系统经济节能运行提供了条件,经运行测试,在3#泵变频调速装置设置闭环运行方式下,其水压可设定在0.42-0.44MPa之间,能够保障系统的安全稳定供水。

一般变频调速节能计算原理是,通过流体力学的基本定律可知:风机、泵类设备均属平方转矩负载,其转速n与流量Q,压力H以及轴功率P具有如下关系:Q∝n,H∝n2,P∝n3;即,流量与转速成正比,压力与转速的平方成正比,轴功率与转速的立方成正比。
根据水泵工作特性:原来系统采用阀门调节水量时,工作点将由A沿曲线向B点移动;目前系统采用变频调速控制时,电机转速下降时,工作点将由B点降至C点。因此采用高压变频调速装置控制,其节电量如图4中阴影部分所示。
根据工艺要求,电机转速降为额定转速的80%时,调速系统从电网侧吸收功率约为额定转速时的51%,即0.83×100%=51%。因此当工艺许可系统水压下降即电机转速下降时,节能效果将十分明显。
我们利用实际运行数据进行比较,有相同结论。3#泵工频、变频两种工况纵向比较有明显节能效果,而横向比较3#泵变频运行工况与1#、2#泵同时工频运行工况更具实际意义;实际运行数据如表1、2所列。
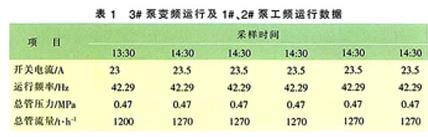

3#泵变频运行共计3小时18分,总输出水量4000t(小时平均1212t),耗电量765kW·h,单位水耗电为0.19kW·h/t;远低于同样工况下,1#、2#泵同时运行时的单位水耗电0.28kW·h/t(2006年度总平均数据)。以2006年总供水量1000万t计算,年节约电量90万kW·h,以0.65元/kW·h计算,年节约电费58.50万元。
4 小结
通过对该车间的变频节能分析测算表明,设备进行变频改造后,具有显著的经济效益;
(1)采用变频调节后,系统实现软启动,电机启动电流只是额定电流,启动时间相应延长,对电网和变压器无大的冲击,减轻了起动机械转矩对电机机械损伤,有效的延长了电机的使用寿命;
(2)变频改造前,水压的调节要靠调整阀门的开度来完成,一次水压的改变通常要反复调节多次才能完成。变频改造后,电机转速的改变只要在远程界面设定即可,大大降低了劳动强度,提高了生产效率,水压调节更平稳、精确;
(3)机泵改变频后,由于变频器采用单元串联移相技术,因此在理论上可以消除29次以下谐波。电网侧电压谐波总含量可以控制在2%以内,电流谐波总含量小于4%;输出电压谐波总含量小于1%,满足IEEE-519国际电能质量谐波标准要求;该变频器为电压源型结构,系统侧功率因数高达0.95。
|