[摘要] 本文通过对机械磨损机理的分析,研究了几种机械磨损元素含量的分析方法,试图更加有效利用磨损元素监测对机械设备的运行状态进行状态监测。通过研究分析,提出了科学地取样方式,解决了机械设备加油不定时、不定量、不能定时换油以及各磨损阶段特征不同等带来的问题,并在实际工作中的得到了应用。
[关键词] 状态监测 故障诊断 取样方法 元素绝对含量 元素相对含量 元素含量变化率
为了提高设备的可利用率,降低维修费用,各种状态监测和故障诊断技术逐步得到了应用。设备维修体系相应经历事后维修、预防性维修,发展到以状态监测为基准的预测性维修。油样直接与机械设备的运转部件相关,因此,它可以更加直接、客观地反映机械设备的运行状况。在状态监测和故障诊断上,油夜分析已经得到了广泛的应用。
机械磨损是机械故障的主要根源,润滑油中磨粒浓度的大小和形态直接反映了机械设备的运行状态。目前,对油样中微粒的分析,主要有两种:即光谱分析(包括原子发射光谱分析和原子吸收光谱分析)和铁谱分析。铁谱分析主要是定性分析,可以进行粗略地定量分析,分析磨粒较大。光谱分析可以对润滑油(脂)的微量元素进行准确的定量分析。显然,对于机械设备的状态监测和故障诊断的早期预报上,光谱分析具有着十分重要的意义。因此,本文着重于讨论光谱磨粒分析技术。由于光谱分析仪器比较昂贵,现场难以推广,它主要应用于大型机械设备的状态监测和故障诊断上。
1、机械磨损规律及润滑油磨粒含量的理论分析
1.1 机械磨损规律及其分析
存在机械运动,就会有摩擦,摩擦一定产生磨损,磨损遵从三个定律:即体积磨损量与摩擦副相对滑动的距离成正比;与法向载荷成正比;与屈服强度或硬度成反比。机械理论和试验表明:磨损率与摩擦因数之间的关系甚微,通常摩擦因数最多相差一个数量级,而磨损率可以相差3个数量级,这就是说,摩擦因数的变化是很小的,导致摩擦率变化范围大的原因在于法向载荷的变化。因此,摩擦因数的变化可以忽略。
我们知道,机械设备的磨损一般分为三个阶段,在磨合阶段,由于摩擦副表面粗糙及几何形状和装配的微量误差,导致润滑不良,法向载荷很大,摩擦副表面磨损迅速,这也取决摩擦副的状况;在正常磨损阶段,摩擦副配合趋于正常,磨损趋于正常状态,摩擦最小,磨损量最小;经过长期运行,磨损到达一定的量时,进入极限磨损阶段,磨损量急剧增大。
从以上分析可以得知,对于一台设备而言,在正常运转时,法向载荷趋于稳定,摩擦副机械磨损量和时间是一个正比变化的关系;在磨合期,各摩擦副的运行未达到稳定状态,各摩擦副的磨损量与时间是一个正变关系,各摩擦副磨损率趋小,但是,各摩擦副的磨损率趋小的速度是不一样的;在极限磨合期,各摩擦副的运行进入了不稳定稳定状态,摩擦副的磨损量与时间同样时一个正变关系,但各摩擦副磨损率趋大。这些分析为我们通过分析润滑油中的磨粒含量,做趋势分析,进行状态监测和故障诊断,提供了科学的依据。
1.2 润滑油磨粒含量的理论分析
从以上的讨论中,我们知道,摩擦副的磨损量与时间是一个正变的关系,在正常运行状态下,它们成正比关系,按照机械润滑理论,在磨粒溶入润滑油和磨粒沉降达到平衡时,并且,保持机械设备内润滑油的总量一定,润滑油中的磨粒含量与时间的关系也符合磨损量与时间的关系。换句话说,润滑油中的磨粒含量与时间成正变增加,在正常运行状态下,呈正比关系,润滑油中磨粒含量的变化率是一样的。
但在实际应用中,我们发现有时出现反常的情况,有时候,甚至于导致错误的结论,这主要和加油量的控制、取样的时机和取样的位置有关。
因此,要做好润滑油的磨粒含量分析,保持机械设备内润滑油的总量一定,严格遵守取样取样规范是非常重要的。
2、磨粒元素含量反映机械运行状态的机理
2.1 机理
由于机械设备的各个摩擦副在强度、刚度、耐磨性等方面的要求不同,它们对组成材料的要求也有差别,元素构成也就不一样。因此,当某一种或多种磨损元素的含量出现异常时,它必然反映了含有这些元素的一个或多个摩擦副磨损异常。这为我们定位某摩擦副的磨损状态和故障诊断分析提供了分析基础。
2.2 磨粒及污染微粒主要来源(见表1)
对于不同设备而言,磨粒元素可能有一定的差别,在进行分析时,一定要了解设备的实际情况。
表1 主要磨粒的来源
元素种类 |
可能来源 |
元素种类 |
可能来源 |
铁(Fe) |
钢铁类摩擦副,如缸套、齿轮等,和腐蚀磨损也有密切关系。 |
钠(Na) |
油品添加剂的钠盐,或冷却水中的处理剂。 |
铜(Cu) |
铜类摩擦副,如,青铜轴承、铜止推环等,或油品添加剂。 |
银(Ag) |
含银摩擦副,如银合金轴承等 |
铅(Pb) |
铅类摩擦副,如铅锡合金轴承等。 |
钒(V) |
重油(催化剂残留物)。 |
铬(Cr) |
镀铬摩擦副,如活塞环等。 |
硼(B) |
冷却水处理剂。 |
锡(Sn) |
锡类摩擦副,如铅锡合金轴承等 |
钡(Ba) |
油品添加剂。 |
硅(Si) |
空气中的尘埃、润滑油中的消泡剂。 |
镁(Mg) |
油品添加剂,含镁摩擦副。 |
钼(Mo) |
油品中的添加剂。含钼摩擦副 |
钙(Ca) |
油品添加剂 |
铝(Al) |
铝合金摩擦副,如铝活塞等 |
锌(Zn) |
油品添加剂,含锌摩擦副。 |
镍(Ni) |
镍钢摩擦副,如曲轴、齿轮等 |
磷(P) |
油品添加剂。 |
钛(Ti) |
钛合金摩擦副。 |
锑(Sb) |
锑合金摩擦副,或油品添加剂。 |
钨(W) |
含合金摩擦副。 |
|
|
3、几种磨粒含量分析方法的比较
3.1 磨粒元素绝对含量分析法及分析应用
3.1.1 磨粒元素绝对含量分析法
磨粒绝对含量,指的是光谱分析分析浓度含量。这种方法已经广泛被大家所接受。如果能够严格控制设备内润滑油总量,遵守取样规则,我们用磨粒绝对含量的极限分析法,或者用趋势分析,都可以达到满意的目的。但是在现场工作中,由于多种因素,比如,定时换油、定时取样、加油量的控制、往往不能控制润滑油总量和遵守取样规则,它的应用受到了很大限制,有时甚至于导致错误的结论。
3.1.1 磨粒绝对元素分析法的应用
在用绝对元素含量分析法趋判断机械磨损的工作状态时,需要确定它的警告值和故障值,是由大量的同一机械设备的光谱分析数据和经验统计的来的。
表2是采油一厂3#压缩机的光谱监测数据
从表2中,我们可以看出,磨粒元素的绝对含量并不符合我们以上的规律,某些元素的绝对含量几乎没有变化,甚至于变小。这是由于没有遵照规则的结果,无法作趋势分析,只能用某一次的绝对含量根据极限值判断机械的运行磨损状态。难以实现早期故障诊断的目的。
在15号油样之后进行大修时发现,3#压缩机连杆上端(小头)的黄铜衬套已经严重磨损,活塞环与缸套也有不同程度的磨损,大修之后,磨损元素绝对含量恢复正常,但是,铁元素含量居高不下,这可能是因为大修时对铁摩擦副的润滑油道清洗不够造成的。
表2 采油一厂3#压缩机的光谱监测数据
油样编号 |
取样日期 |
运行
机时数 |
磨粒元素含量(ppm) |
Fe |
Cr |
Cu |
Al |
10 |
2001.5.6 |
|
9.8 |
0.7 |
7.1 |
1.2 |
11 |
2001.6.10 |
|
17 |
1.5 |
15.6 |
3.7 |
12 |
2001.7.3 |
|
22.5 |
1.5 |
21.3 |
5.8 |
13 |
2001.8.16 |
|
28.5 |
1.3 |
27 |
5.6 |
14 |
2001.9.30 |
|
21 |
1 |
25 |
6 |
15 |
2001.10.25 |
|
21.4 |
1.1 |
28.5 |
5.4 |
16 |
2001.11.4 |
|
34.4 |
2.3 |
8.1 |
3 |
3.2 磨粒元素相对含量分析法
3.2.1 概念
从前面的讨论我们知道,机械设备在正常运行状态下,磨粒含量的变化率是一个常量,也就是说各个摩擦副的磨粒含量增加的比例是一样的。从这个思路出发,我们可以对一种磨粒元素占总体磨粒元素的比例进行研究。假如磨粒元素包括n中元素,它们的对应绝对元素含量时 C1, C2, C3, C4, C5,… CN,对应于Ci 的比例用Si表示。则第I种元素的Si如下表示:
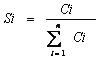
我们称Si为第I种元素的相对含量
3.2.2 相对含量反映机械运行状态的的机理
由于机械设备在正常运行状态下,各个摩擦副的磨粒含量增加的比例是一样的,假设是β倍。则:
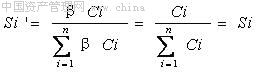
由上式可见,元素相对含量在机械设备处于正常工作状态时趋于稳定。当某一种磨损元素或几种含量异常时,元素相对含量就会增大,而其他磨损员的含量就会缩小。拉大了元素含量的相对差距。因此,有关元素相对含量的变化反映了机械设备的运行状态。由公式可见,元素的相对含量与润滑油总量无关,与换油和加油的量都没有多大关系。因此,它克服了绝对元素含量分析的缺点,并且,可以用于机械磨损的任何磨损阶段。
3.2.3 相对含量的分析应用
在理想的情况下,正常运行机械设备的相对含量是一个不变的量。但是,由于光谱分析、取样等误差的存在,每一种元素相对含量都服从正态分布。因此,我们可以对正常运行状态的相对含量进行统计分析,算出平均值和标准方差。确定警告值和故障值。公式如下:
警告值=平均值+x1*标准方差 故障值=平均值+x2*标准方差
其中x1、x2是由经验确定的值。一般x2取为x1的两倍。 按前人的研究经验和统计学、机械相关理论,x1、x2推荐按下表3取值。
表3 x1、x2推荐值
|
x1推荐值 |
X2推荐值 |
连续运转机械设备(如天然气压缩机组) |
2 |
3 |
其他机械设备 |
2 |
4 |
工程机械 |
2.5 |
5 |
将表1的数据转换成磨粒相对含量,见表4
表4 采油一厂3#压缩机的磨粒相对含量
|
10 |
11 |
12 |
13 |
14 |
15 |
16 |
Fe |
0.52 |
0.45 |
0.44 |
0.45 |
0.40 |
0.38 |
0.72 |
Cr |
0.04 |
0.04 |
0.03 |
0.02 |
0.02 |
0.02 |
0.05 |
Cu |
0.38 |
0.41 |
0.42 |
0.44 |
0.47 |
0.51 |
0.17 |
Al |
0.06 |
0.10 |
0.11 |
0.09 |
0.11 |
0.10 |
0.06 |
从表4可以看出,从10#油样到15#是持续增加的,因此,这个表不能用来统计正常运行状态的相对含量,显然,含铜的摩擦副早进入了异常磨损状态。因此,按照绝对含量的预报有些偏晚。
前人曾经对74W挖掘机做过研究,并且,得出了各磨粒元素的相对含量标准,见表5
表5 74W挖掘机发动机相对含量标准
|
Fe |
Cu |
Cr |
Al |
Si |
Pb |
警告值 |
0.693 |
0.103 |
0.042 |
0.052 |
0.113 |
0.145 |
故障值 |
0.740 |
0.130 |
0.054 |
0.064 |
0.133 |
0.170 |
表6和表7分别一台74#挖掘机光谱分析的绝对含量数据和相对含量数据
表6 012#挖掘机的磨粒绝对含量
|
0034 |
0082 |
0145 |
0169 |
0232 |
0274 |
Fe |
97.7 |
111.5 |
136.5 |
163.7 |
209.4 |
312.3 |
Cu |
11.6 |
14.9 |
16.3 |
18.7 |
20.9 |
22.5 |
Cr |
5.2 |
5.6 |
6.1 |
7.1 |
7.4 |
8.1 |
Al |
4.7 |
6.4 |
7.2 |
8.1 |
9.2 |
10.6 |
Si |
13.6 |
15.5 |
18.4 |
21.3 |
23.6 |
26 |
Pb |
20 |
23.5 |
26.5 |
30.6 |
33.6 |
37.4 |
表7 012#挖掘机的磨粒相对含量
|
0034 |
0082 |
0145 |
0169 |
0232 |
0274 |
Fe |
0.639398 |
0.628523 |
0.646919 |
0.656112 |
0.688589 |
0.749101 |
Cu |
0.075916 |
0.083991 |
0.077251 |
0.07495 |
0.068727 |
0.05397 |
Cr |
0.034031 |
0.031567 |
0.02891 |
0.028457 |
0.024334 |
0.019429 |
Al |
0.030759 |
0.036077 |
0.034123 |
0.032465 |
0.030253 |
0.025426 |
Si |
0.089005 |
0.087373 |
0.087204 |
0.085371 |
0.077606 |
0.062365 |
Pb |
0.13089 |
0.132469 |
0.125592 |
0.122645 |
0.11049 |
0.08971 |
从表6中,很难判断挖掘机磨损异常状况,而从表7可以很明显地看出,各元素在0034#油样到0169#油样,各种磨粒元素的相对含量变化是无常的。从0169#样到0274#样,磨损增加明显,到了0274#样,Fe元素相对含量已经超过故障值(参见表5)
由此可知,使用磨粒元素相对含量的分析方法比绝对含量要灵敏、准确,而且,对于现场操作的要求要简单得多。
4、重要取样规则
无论使用何种方法,遵守取样规则,都会大大提高光谱磨粒分析的准确性和可靠性,从而,做到对状态监测和故障诊断准确预测和预报。必须遵守取样规则如下
1)应该选择恰当的取样位置,使其能够反映机械设备的真实磨损情况。如,润滑油主油道、润滑油盘的中部。 2)记录取样时间和运行小时数,相对含量分析方法不需要这个要求 3)定时取样。相对含量分析方法,不需要严格的定时取样。当分析结果异常时,加密取样间隔。 4)选择取样的时机。在加油时、换油时、重新开机时,要等到所有润滑油都能进行体循环时取样。 5)如果采用磨粒绝对含量分析方法,一定要严格控制每一次的加油量,保证机械设备体内润滑油的总量一定。 只有这样,才能够早期、准确、可靠地预测预报机械磨损状态,使得光谱分析技术充分发挥效益。
5、结束语 通过以上分析,我们认为,磨粒相对含量分析法比绝对含量分析法更加有效,而且,适用于各个磨损阶段。从标准的建立上,也是非常可行的。这为各种大型机械设备的状态监测和故障诊断提供了广阔的空间。
参考文献 1、《机械工程师》第二版,机械工业出版社出版,2000.5 2、《设备状态监测和故障诊断技术》 陈可兴 李川奇 科学技书出版社 1991.8
|