1 引言 无梭织机的主传动一般都采用高转矩三相交流电动机驱动,通过三角皮带和离合器来传动主轴和其它的机构,变速时更换皮带轮,停车时采用制动装置。传统的织机主传动系统中离合器和刹车片的磨损以及皮带的打滑都会使起停性能逐渐变差,需要定时更换维修;另外,使用交流异步电动机织机只能通过更换皮带轮实现有级调速。当织机在慢速寻纬时还需专配一台小电机带动相关机构完成,从而增加了机械的复杂程度和维护难度。中低档挠性剑杆织机的电控系统一般都采用电子元件或集成线路板与继电器组成的电控系统。织机停车故障的引入信号主要为断经和断纬,其中由压电陶瓷传感器引入的纬纱信号为连续模拟小信号,而上述电控系统是通过继电器实现逻辑控制的,不能对该模拟量进行有效的运算处理;在现场控制中,由于电网电压波动、机器振动等干扰因素,使断纬电信号检测失误,造成织机无故停车,直接影响到织造质量和机器效率。 近年来比利时毕佳乐公司引入了一种新型交流调速电动机传动系统—开关型磁阻电动机(SRM,称作Sumo马达)传动系统,该公司生产的无梭织机均将Sumo马达作为织机的标准配置。由于该类电动机结构简单坚固、工作可靠、效率高,因此由其构成的传动系统运行性能和经济指标比普通的交流电动机,甚至比晶闸管-直流电动机系统都好。Sumo马达基于可调节磁阻技术,可直接启动织机,无需离合器和制动装置,有相当快的响应速度。 针对现有剑杆织机电控系统的上述缺陷,本文提出了一种利用可编程控制器系统取代原电子元件、集成线路板、继电器的开关磁阻电机控制系统,使其性能得到进一步的改善。 2 无梭织机主传动系统控制要求 2.1 织机的启动 按下启动按钮,能够正常启动开车;织机正常开车的前提条件是:左右墙板上安装的光电安全装置处无障碍物,找纬信号开关断开,经停、纬停装置处于无断经、断纬状态,紧急停车按钮释放。 可实现点动操作。当按下点动按钮时,剑杆织机剑头动程和速度大小由手控按钮的时间长短来决定。
2.2 织机的制动 断经停车:断经可能发生在织机的任何角度,其停车按图1所示时序进行。这里涉及到一个“刹车角”的概念,即刹车动作开始到织机完全刹停的角度,本课题的织机刹车角为90°(310°~40°)。当检测到断经发生时,织机一直运行到310°时开始刹车,40°时刹车动作完成(此时织机负载最大,有利于刹车),然后再返回到320°综平位置(有利于穿经),至此断经定位停车动作完成。 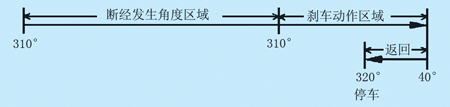
图1 断经停车 断纬停车:断纬一般发生在织机的引纬过程中,其停车按图2所示时序进行。在织机的90°—290°区域检测纬纱状态(正常时该区域内有纬纱信号输出),织机一直运行到310°时开始刹车,40°时刹车动作完成,然后再返回到前一纬的40°(开口最大位置,有利于处理纬纱),至此断纬定位停车动作完成。
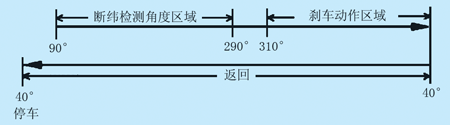
图2 断纬停车 在织布达到预先设定的长度后或当遇到换班、临时检修等时,可使织机停于经停位置;出现紧急状态时,按下停车按钮使织机停车,此时停车位置不受主轴转角的限制。
2.3 织机的调速 当织制不同品种需要改变织机转速的时候,可以通过直接调节电机转速来实现。 3 系统的硬件设计 3.1 织机的选取 织机选用实验室样机,其额定转速300r/min。用开关磁阻电机取代原有的电机、皮带轮、离合器和制动器。 3.2 开关磁阻电机 试验选用国产的通用开关磁阻电机。其主要技术参数如下:额定功率3kW,额定转矩19.1N·M,额定转速1500r/min,转速范围30~2000r/min,输出特性:恒转矩(30~1500),启动转矩28.6N·M,制动转矩19.1N·M。 3.3 自动寻纬功能的实现方案 传统剑杆织机配备有辅助传动机构,由一功率较小的电动机驱动,使织机以较低的转速正转或反转。当经停或纬停发生时,低速电机将以预定的方式驱动织机的有关机构进行找断纬和对织口等操作。在本系统中,由于主电动机采用开关磁阻电动机,并由PLC进行控制,调速方便。因此,省去原来的辅助传动机构。直接由主电机完成原来辅助传动机构的操作。 其方案示意图见图3: 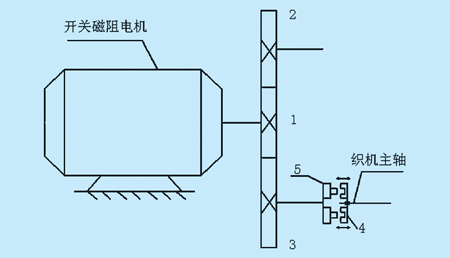
图3 方案示意图 在织机正常运行时,图中4向左移动和5啮合,电动机通过齿轮3带动主轴、齿轮2带动开口机构等运转。当需要做寻纬等慢速动作时,控制器发出信号,图3中4向右轴向移动,于是4和5脱开,主轴脱离电机转动系统。电动机通过齿轮1、2只带动开口等机构慢速反转。慢速反转结束后,在正常开车前,4再向左轴向移动与5啮合,从而再次带动主轴正常运转。在织机正常启动运转时,其主轴转速为300r/min,试验用齿轮模数为6,齿数分别为Z1=23、Z2=57、Z3=57,从电机到织机主轴的传动比为2.5。
3.4 PLC控制系统的优势及选取 与传统的继电器逻辑控制相比,PLC具有的主要优势为:可靠性高,逻辑功能强,体积小;采用软件编程来实现控制任务,改变控制功能只需改变程序;PLC以继电器逻辑梯形图为编程语言,学习方便;抗干扰能力强,能够在恶劣的环境下可靠运作。现代PLC已经成为工业自动化领域中最重要、应用最多的控制设备。从国内纺机厂的生产状况分析看,江苏高淳、山西经纬、无锡龙力等,均采用以PLC为核心并配以旋转光电编码器为检测元件作为主要电控器件,既简化了硬件设计,减少故障点,又提高了系统的可靠性和稳定性,得到了用户肯定。这表明该系统设计已趋成熟。 PLC的选取考虑两个问题:PLC的容量和选择何家公司的PLC及外设。本系统包括以下输入输出点,见表1: 表1 I/O点数 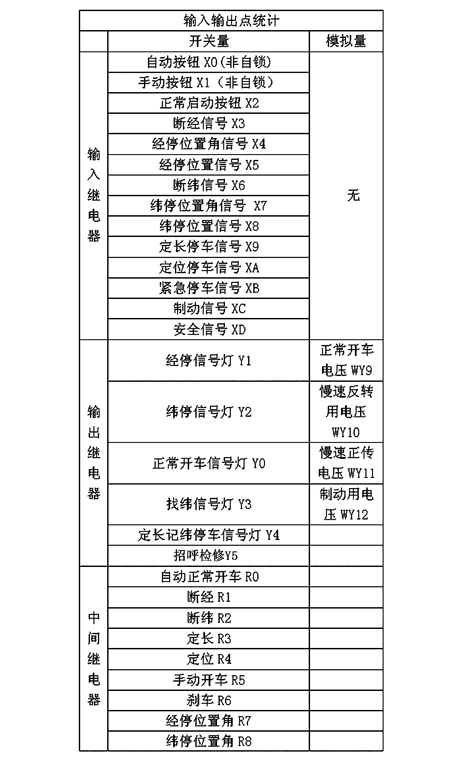
本系统共包括24路开关量,4路模拟量。因此选用松下电工的型号为FP1C40的PLC。其有24个输入点和16个输出点,另加一FP1-2D/A扩展单元,扩展单元可扩展4个模拟点,可以满足本系统的要求。 FP1是松下电工的FP系列产品中一种功能很强的小型机,虽然其进入中国市场较晚,但由于设计上的独到之处和优良的控制功能,一经推出就很受欢迎。FP1主控单元内有高速计数器,可输入高达10kHz的脉冲,并可同时输入两路脉冲。还可输出频率可调的脉冲信号,具有8个中断源的中断优先权管理。通过主机上配有的RS-422或RS-232接口,可实现PLC和PC机之间的通信。FP1的硬件配置较全,主机可通过外接I/O扩展单元(扩展单元为一些扩展I/O点数的模块,由E8~E40系列组成)。FP1的智能单元主要有A/D、D/A模块。当需要对模拟量进行测量和控制时,可以连接智能单元。
4 系统软件设计 该系统软件程序的流程框图如图4所示: 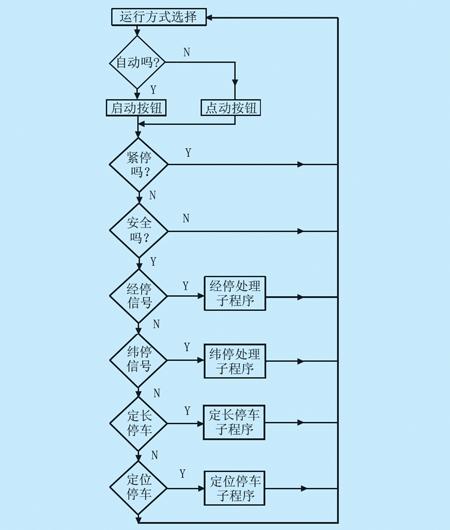
图4 系统软件程序的流程 程序开始首先选择系统的运行方式,即自动还是点动。选择自动按钮时,系统将进入自动运行状态,首先判断紧急停车信号、安全信号、经停、纬停、定长和定位信号的状态,如果上述信号都未接通,则PLC通过输出继电器向电机输出正常启动所需要的电压,织机在电机带动下迅速启动。如上述任一信号接通,则程序立即转向相应的子程序。待子程序执行完毕,相应的信号复位后可重新开车。 由此由主轴正常转速400r/min,得电机正常转速为400×2.5=1000r/min。在电机需要慢速倒转带动开口等机构运动时候,同理可得电机的转速应该为30×2.5=75r/min。所选的开关磁阻电动机的调速控制由电位器的给定电压来控制,向电位器给定正向电压则电动机正转,反之则反转。电位器给定的电压范围为-10V~+10V,对应输出转速从-2000n/m~+2000n/m成比例变化。从PLC控制的角度看,所选用的松下FP1模拟量输出电压范围为0~10V和0~5V两档,选择第一档,对正常启动时向电位器输出5V电压;对慢速转动时输出电压0.375V。对于输出负电压则在接线时反结电位器即可。
5 结束语 通过本系统设计、试验,得到如下结论:采用PLC控制,使主传动控制系统硬件电路大为简化,系统运行可靠;同时还可扩展为整台织机的控制器,以实现整机的协调工作,提高织机的自动化程度。采用开关磁阻电动机调速方便,省去了电磁离合器等零部件,当织机在慢速运转和寻纬时无需专配小电机,由主电机直接带动主轴完成,降低了机械的复杂程度和维护难度,生产效率也同时提高。
|