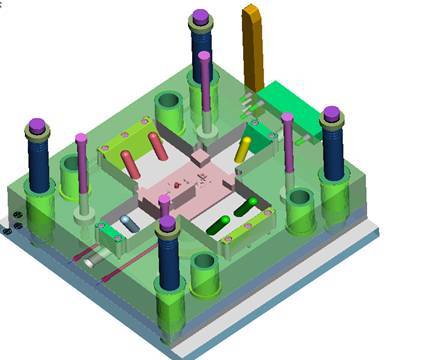
模具设计最大的困难和挑战是如何减少磨损。毕竟,磨损得越厉害,模具的修理费用越高,模具寿命越短。因此对于模具设计者和制造者来说,减少磨损是其重要目标之一,但是这又是一个难以克服的难题,尤其是模具在进行成型生产时会有各种不利的情况发生。
磨损的挑战
模具设计者和制造者试图使用一些典型的方法以减少磨损,如使用不同的金属材料,使用低磨损的涂层,指定高硬度的金属材料,合模的设计要增大角度以避免合模锁死,以及更多基于经验的方法。然而,不能够被设计者和模具制造者很好理解的一种设计原则是:由成型过程中的一些负载和应力引起的模具零部件磨损,也应该被消除。
1、动态条件
模具设计者和制造者关注模具制造环节特别是模具装配阶段。他们进行多次尝试以使模具零部件能够通过手工装配在一起。在较好的模具制造厂中,锤子、撬杠和夹钳是严格被禁止使用或者使用受限的。虽然大多数模具是通过手工装配的,模具部件拥有紧密的公差配合。但是这是在没有考虑应力的前提下的。也就是说,模具处于一种静态条件下。
注塑加工商注意到了模具处于动态条件下的状态。由于成型条件的不断改变,模具部件可能移动了位置,例如,被锁模、开模与合模、不同的加热和冷却引起的热力学改变以及注射压力引起的应力变化使部件移位。因此,对于注塑加工商来说,模具是活动的或者说是一种动态设备,它在生产中不是静止不动的。
经过多年的实践,注塑加工商和模具制造商已经认识到模具是动态设备,而动态条件能够引起模具部件偏离原来的位置。当一个力加在模具部件上时,这些部件会移出原来的位置,与相邻的部件碰撞,从而使这些部件之间产生了高负荷和高应力。这些应力产生的一个严重的后果就是造成模具的磨损。
2、准确合模的途径
注塑加工商已认识到过度的磨损是由不可预期的应力引起的,因此他们开始使用多种设计来解决问题。其中一个最常见的办法就是采用成本日益增加的准确合模技术,如采用高成本的直线联动装置,其原理是增加了复杂的合模调整,这种调整使模具内部件尽管受力也不会发生移动。基于这种装置的昂贵性,注塑加工商还试图采用别的方法阻止模具内部件的运动。
将磨损最小化的解决方案
其实,解决由运动引起的应力的最好方法非常简单。如果部件A处于部件B的压迫之下使两个部件都处于压力之下,那么去除压力也就解决了问题。去除应力可通过一种革命性的方法来完成,也就是通过组合的设计使部件在模具内可以移动。
可以肯定的是,如果部件A由于压力而移动,那就允许部件B随着A同时移动。因为两个部件同时移动,其应力可被减少或者消除,进而使磨损迅速降低。这种设计依赖于特殊的设计概念,即悬浮的概念。
允许部件移动或者悬浮的概念与模具制造商的传统理念是完全背离的。这是一种与经验和传统理念无关的概念。业界逐渐认识到一种可旋开的模具类型对于降低磨损最有效(例如,为带有内螺纹的制品设计的模具)。今天,那些已经采纳了这个概念并将其运用到模具设计中的注塑加工商,正在打造异常成功的模具,以大大节约模具维修的费用。
注塑加工商使用含有铜合金的模具用以提高冷却效果,可是发现铜合金容易损坏。于是又想方设法提高铜合金的耐磨性,然而这又会显著降低热传导性能。因此注塑加工商只能被迫选择快速成型来提高模具冷却性能或者更好地对抗磨损。成功使用铜合金模具的注塑加工商已经意识到,悬浮的模具部件可能是将模具的磨损减至最小的设计概念。悬浮模具部件可使注塑加工商获得最小的磨损和高速的成型周期。
成功的关键及举例
悬浮模具部件成功的关键是确定哪个部件将被悬浮起来,以及怎样设计使它们悬浮起来。注塑加工商在成功确定这两个方案后,就能够获得快速的成型周期和较低的模具修理费用。
以下图为例,如果部件向注塑模具内部移动,那么移动部件发生磨损的概率将会非常高。在本案例中,最可能受到磨损的部件是A部件(喷管芯)、B部件(顶出套筒)及C部件(B 侧芯)。其中,喷管芯A的磨损发生在外径处,因为顶出套筒B与喷管芯A很紧;顶出套筒B内径会磨损,因为其与喷管芯A配合太紧密。顶出套筒B的外径会因为部件C,即B侧芯内部的摩擦而引起磨损;B侧芯的内径会因为顶出套筒外侧的摩擦而引起磨损。
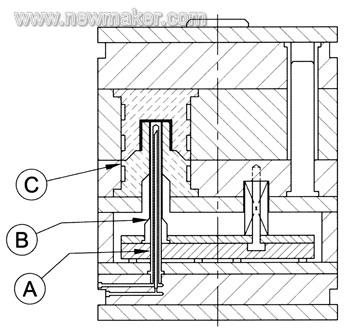
基于以上的分析,我们可以给出以下建议:每一个部件都采用 “悬浮”或者更加特殊的设计,从而使它们都能够轻微移动,进而消除部件之间的应力;与其他两个部件运动方向相反的是顶出套筒,在设计这个部件时,应该尽量减小它在移动时的应力,从而显著减少磨损;在设计部件C时,也应该使其能够轻微悬浮(使用带子和吊杆固定),以此减少摩损的可能性。
|